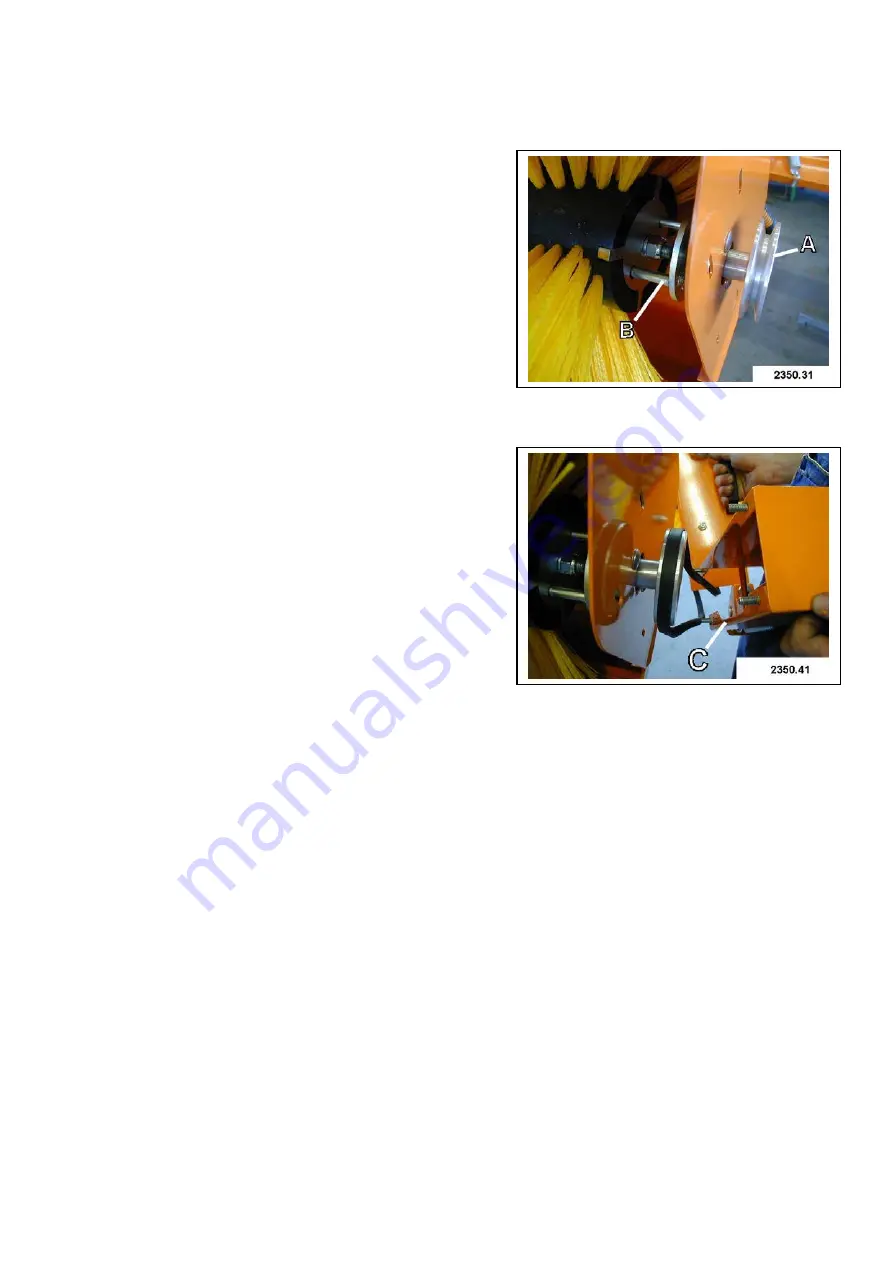
All information, illustrations and specifications in these Operating Instructions are based on the latest information available at the time of
publication. We reserve the right to make design changes at any time without prior notification
23
4.0. Operating
4.4.
INSTALLING LATERAL BROOM
Screw on V-belt pulley (A) to
attachment (B) on the right of
side part.
Insert V-belt into the profile
of the V-belt pulley.
Insert lateral broom retainer
(C) with the screws to side part
(middle slot) and secure with
nuts.
Release nuts to retension. Push
lateral broom retainer forward.
Secure setting by tightening the
nuts.