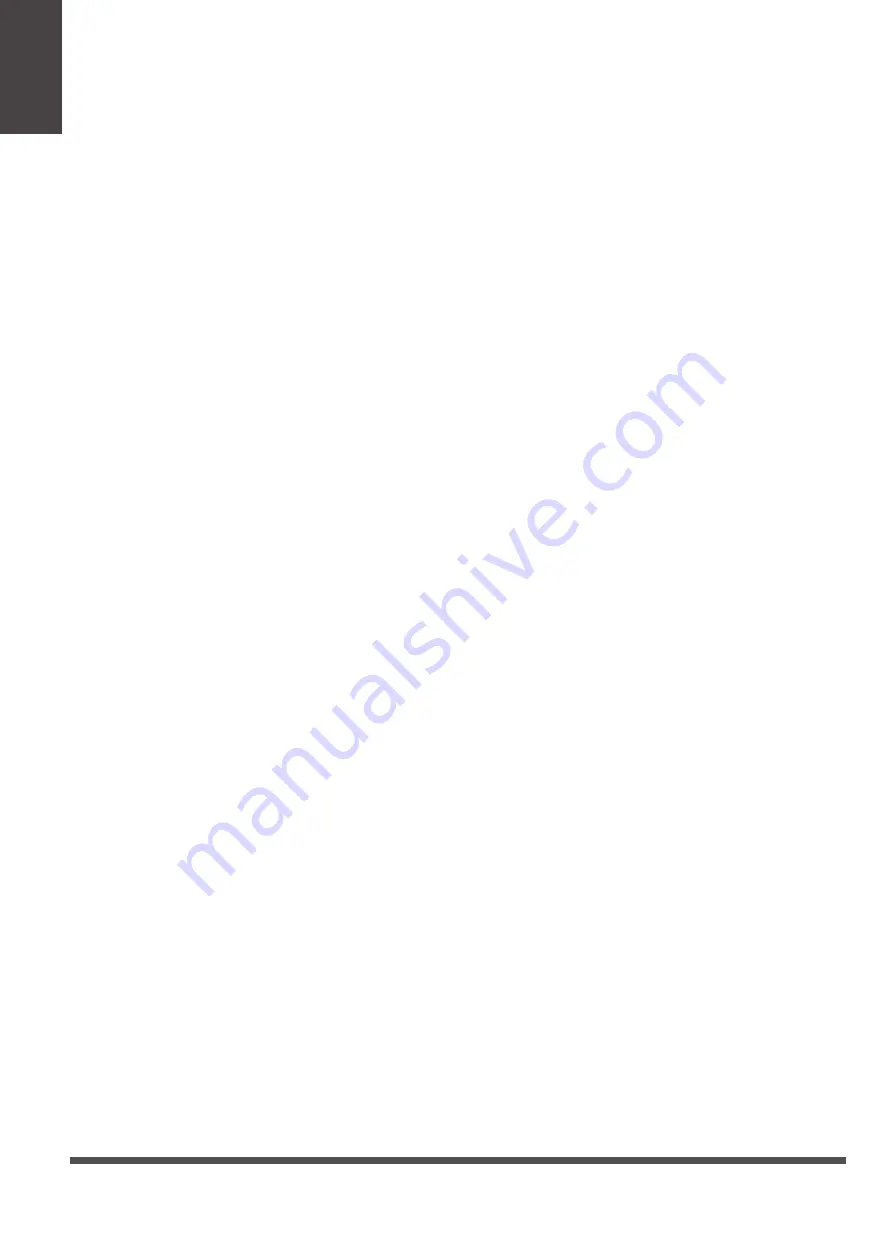
Safety
Precautions
15.
Labelling
Equipment shall be labelled stating that it has been decommissioned and emptied of refrigerant. The
label
shall be dated and signed. Ensure that there are labels on the equipment stating the equipment
contains
flammable refrigerant.
16.
Recovery
When removing refrigerant from a system, either for servicing or decommissioning, it is recommended
good practice that all refrigerants are removed safely. When transferring refrigerant into cylinders,
ensure
that only appropriate refrigerant recovery cylinders are employed. Ensure that the correct
number of
cylinders for holding the total system charge is available. All cylinders to be used are
designated for the
recovered refrigerant and labelled for that refrigerant (i.e. special cylinders for the
recovery of refrigerant).
Cylinders shall be complete with pressure relief valve and associated shut-off
valves in good working
order. Empty recovery cylinders are evacuated and, if possible, cooled before
13.
Charging procedures
In addition to conventional charging procedures, the following requirements shall be followed. Ensure
that contamination of different refrigerants does not occur when using charging equipment. Hoses or
lines shall be as short as possible to minimise the amount of refrigerant contained in them.
Cylinders shall be kept upright.
Ensure that the refrigeration system is earthed prior to charging the system with refrigerant.
Label the system when charging is complete (if not already).
Extreme care shall be taken not to overfill the refrigeration system. Prior to recharging the system it
shall
be pressure tested with OFN. The system shall be leak tested on completion of charging but prior
to
commissioning. A follow up leak test shall be carried out prior to leaving the site.
14.
Decommissioning
Before carrying out this procedure, it is essential that the technician is completely familiar with the
equipment and all its detail. It is recommended good practice that all refrigerants are recovered safely.
Prior to the task being carried out, an oil and refrigerant sample shall be taken in case analysis is
required
prior to re-use of reclaimed refrigerant. It is essential that electrical power is available before
the task is
commenced.
a)
Become familiar with the equipment and its operation. b) Isolate system electrically. c) Before
attempting the procedure ensure that: Mechanical handling equipment is available, if required, for
handling refrigerant cylinders;All personal protective equipment is available and being used correctly;
The recovery process is supervised at all times by a competent person; Recovery equipment and
cylinders
conform to the appropriate standards. d) Pump down refrigerant system, if possible. e) If a
vacuum is
not possible, make a manifold so that refrigerant can be removed from various parts of the
system. f)
Make sure that cylinder is situated on the scales before recovery takes place. g) Start the
recovery
machine and operate in accordance with manufacturer's instructions. h) Do not overfill
cylinders. (No
more than 80 % volume liquid charge). i) Do not exceed the maximum working
pressure of thecylinder,
even temporarily. j) When the cylinders have been filled correctly and the
process completed, make
sure that the cylinders and the equipment are removed from site promptly
and all isolation valves on the
equipment are closed off. k) Recovered refrigerant shall not be charged
into another refrigeration
system unless it has been cleaned and checked.
oxygen shall not be used for this task. Flushing shall be achieved by breaking the vacuum in the system
with OFN and continuing to fill until the working pressure is achieved, then venting to atmosphere, and
finally pulling down to a vacuum. This process shall be repeated until no refrigerant is within the system.
When the final OFN charge is used, the system shall be vented down to atmospheric pressure to enable
work to take place. This operation is absolutely vital if brazing operations on the pipe-work are to take
place. Ensure that the outlet for the vacuum pump is not close to any ignition sources and there is
ventilation available.
Page
9