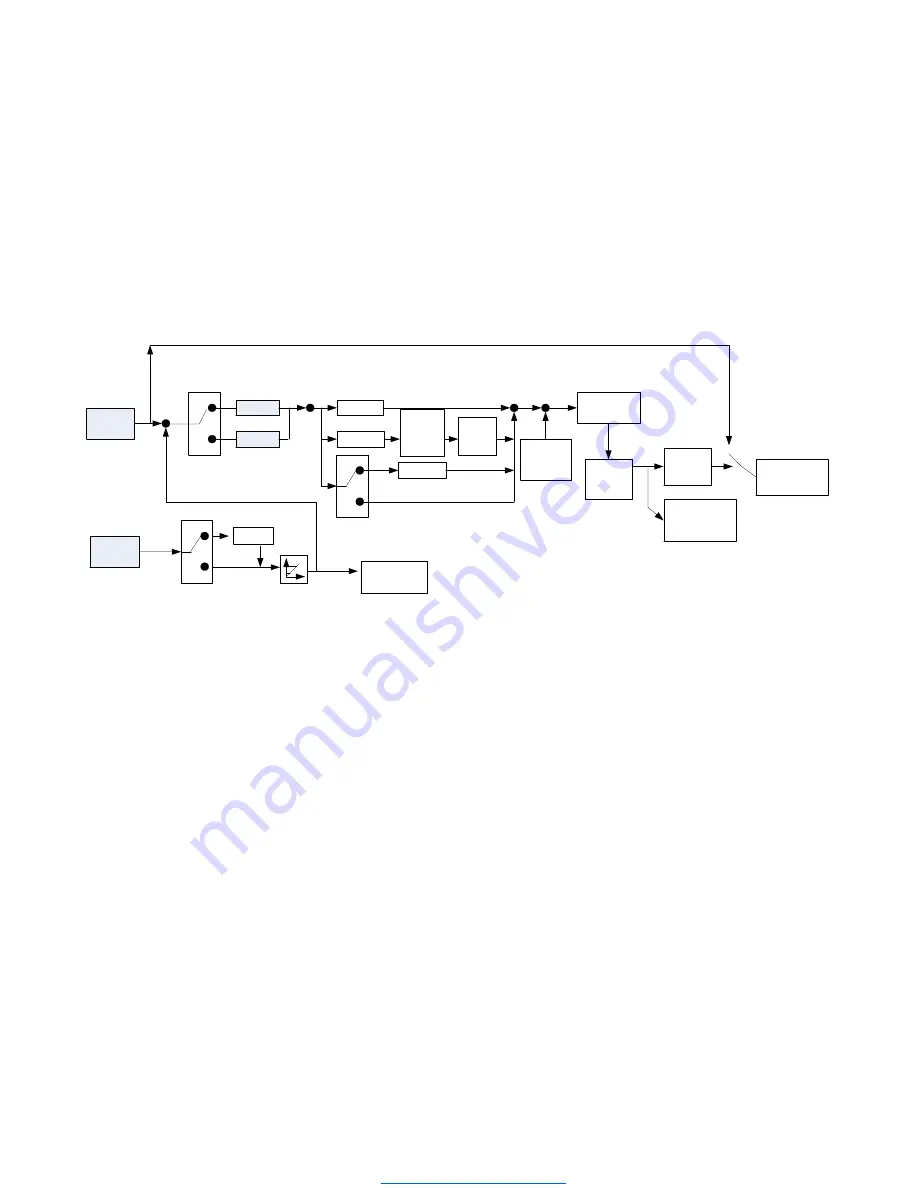
9-1
9. Using PID Control for Constant Flow / Pressure Applications
9.1 What is PID Control?
The PID function in the inverter can be used to maintain a constant process variable such as pressure, flow,
temperature by regulating the output frequency (motor speed). A feedback device (transducer) signal is used to
compare the actual process variable to a specified setpoint. The difference between the set-point and feedback
signal is called the error signal.
The PID control tries to minimize this error to maintain a constant process variable by regulating the output
frequency (motor speed).
1
、
2
3
、
4
Postive
Negative
10- 03
P( 10- 05)
I ( 10- 06)
+
10- 03
-
10-00
Target
value
10-01
Feedback
value
10- 21
10- 22
12 - 00 display
PID feedback
10- 03=0
Or stop
I limiter
(10-14)
1
、
3
2
、
4
D( 10- 07)
+
+
Offset
( 10- 08
10- 09)
+
Delay device
( 10- 10)
PID
communication
read
Sleep
Wake
function
PID frequency
output
2
、
4
1
、
3
10- 03
I Reset
(10-15)
PID Limit
(00-12)
D (10-07)
The amplitude of the error can be adjusted with the Proportional Gain parameter 10-05 and is directly related to
the output of the PID controller, so the larger gain the larger the output correction.
Downloaded from Dealers Industrial Equipment -- Visit