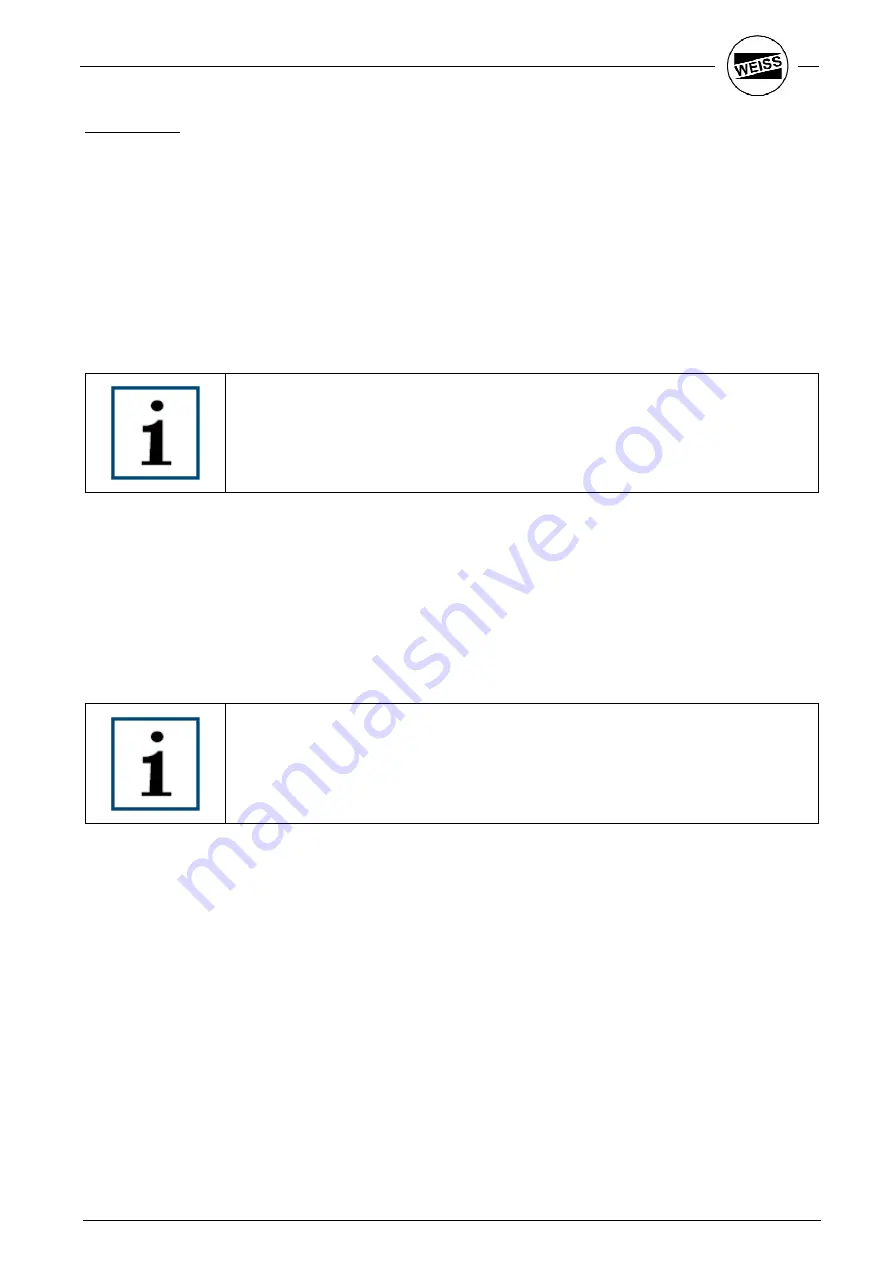
35
WAS.handling Electro Documentation
Reference run
Because the used incremental encoder system is not equipped with a reference signal, a reference search
must be done before the first positioning can start. The only possibility which the mechanics offers consists in
taking the end of the axis as a reference point (reference on limit stop). For this, the axis moves in a specified
direction with slow speed and reduced torque, until it recognizes a block (following error increases). The order
of the axes as well as the torque can be defined.
The disadvantage of this method is that the System does not recognize if it is actually at the end of the axis or
the axis is only blocked by a part in the way.
One must also ensure that the end of the axis is always clean. A pollution (pollution with dust creeping e.g.)
results in a displacement of the reference point (offset), which gives a wrong position.
Because of the small dimensions of the axis and the high dynamics of the linear motors, a crash at full speed
to the mechanical limit may deform it. Normally this is prevented by the Software, but in case of emergency
stop or power loss, the axes could run to their limits.
- Never move with full speed to the mechanical limit!
- Keep the end of the axis clean!
- Make sure that no parts block the way during the reference search!
4.4 Machine Zero Position
Depending on the application, the adjustment of machine zero position could be necessary. After setting up the
hardware and connection of the handling, the machine zero position has to be determined exactly. For this you
move the axes via jog mode exact to the position where 0/0 should be. Then give the command "Set Zero" via
the Windows program or via the digital input. As a result, you will see that the current position is changing to
0.000mm. After mounting the handling you must do this only one time.
The machine zero position is invalid after disassembly of the mechanics,
replacement of the encoder or memory card in the ACOPOS drive!
Note:
Mark this position permanently. So you can find and re-teach the machine zero position quickly after repair.
Summary of Contents for HP140
Page 1: ...04 2010 ...
Page 15: ...WAS handling Electro Documentation 12 Drilling template Fixing screws M5 ...
Page 17: ...WAS handling Electro Documentation 14 Drilling template Fixing screws M5 ...
Page 20: ...17 WAS handling Electro Documentation ACOPOS 1022 three phase connection 3 x 400V 480V ...
Page 46: ...43 WAS handling Electro Documentation ...
Page 47: ......
Page 48: ......