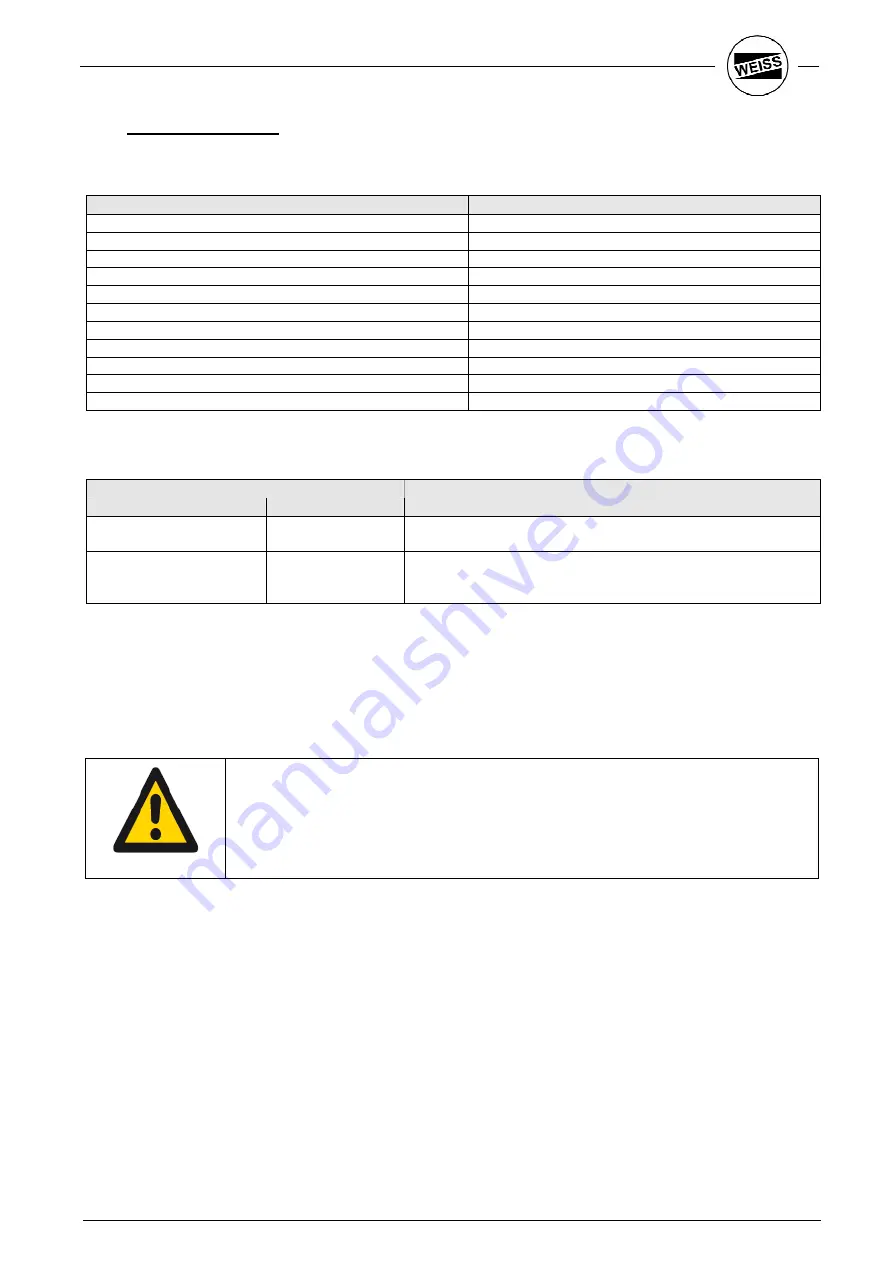
31
WAS.handling Electro Documentation
4.1.2 Secure restart inhibit
ACOPOS servo drives use integrated safe pulse disabling for secure shutdown and to prevent unwanted
startup. This is designed to meet the following safety classifications depending on the external circuit:
Criteria:
Characteristic value
Max. performance level acc. EN ISO 13849
PL d
Max. safety integrity level acc IEC 62061
SIL 2
Max. safety integrity level acc IEC 61508
SIL 2
Max. safety category according to EN 954-1
1)
CAT 3
PFH (Probability of dangerous Failure per Hour)
<4*10
9
HFT (Hardware Fault Tolerance)
0
PT (Proof Test interval)
10 years
DC (Diagnostic Coverage)
99 %
CCF (Common Cause Failure)
5 %
SFF (Safe Failure Fraction)
>99 %
MTTFD (Mean Time To Failure dangerous)
>140 years
1)
Die EN 954-1 is no longer valid and has been replaced by EN ISO 13849.
The following table provides an overview of the individual safety functions that can be implemented:
label according to standard:
EN 61800-5-2
EN 60204-1
Short description
STO (Safe Torque off)
Stop Category 0
Shut-down by immediate switching-off of the energy supply to
the drive machinery (i.e. an uncontrolled shut-down).
SS1 (Safe Stop 1)
Stop Category 1
Introduction of active braking and activation of the STO
function after a defined amount of time has expired.
(Implementation by user)
The restart inhibit interrupts the energy supply to the drive by blocking the pulses to the IGBT’s. This means
that no rotary field can be built up in the servo motor. This function is realized by the terminal X1/9 on the front
of the ACOPOS drive. The terminal X1/10 is the ground (GND) for terminal X1/9, these terminals are
electrically isolated from the 24 V supply.
Danger !
Take note that multiple faults in the IGBT bridge can lead to a brief jerking. The
maximum stroke of the axis depends on the used motor. For the HP140 this is
about 5mm.
Please note that the integrated “secure restart inhibit” does not interrupt the voltage supply to the motor. It only
prevents the development of a rotary field and thus reliably prevents a restart of the motor. If electrical work is
performed on the motor, the mains supply must be cut off by a mains contactor or a master switch.
Please also observe the discharge time of the DC-bus of at least 5 minutes before electrical work can be start.
When the LED’s on the ACOPOS drive go off, this is not an indication that the voltages are shut down and the
DC-bus has discharged to less than 42 V.
Summary of Contents for HP140
Page 1: ...04 2010 ...
Page 15: ...WAS handling Electro Documentation 12 Drilling template Fixing screws M5 ...
Page 17: ...WAS handling Electro Documentation 14 Drilling template Fixing screws M5 ...
Page 20: ...17 WAS handling Electro Documentation ACOPOS 1022 three phase connection 3 x 400V 480V ...
Page 46: ...43 WAS handling Electro Documentation ...
Page 47: ......
Page 48: ......