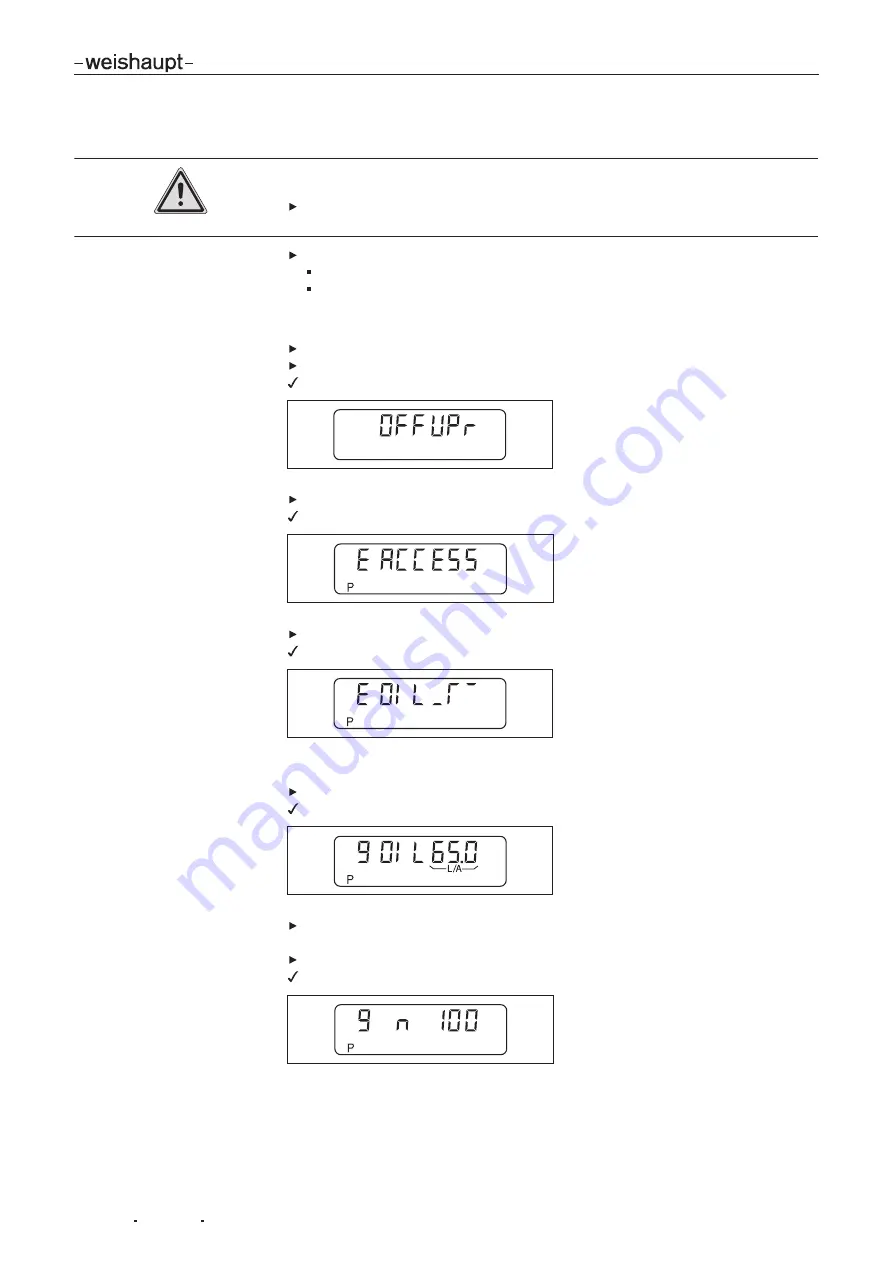
Installation and operating instruction
Oil burner WL40Z-A 1LN
7 Commissioning
83298902 2/2019-05 La
46-112
7.2.2 Burner with variable speed drive (optional)
DANGER
Risk of electric shock
Touching the ignition device can lead to electric shock.
Do not touch ignition device during the ignition process.
During commissioning check:
suction resistance or flow pressure of oil pump [ch. 5.1],
mixing pressure [ch. 7.1.1].
1. Preset combustion manager
Unplug bridging plug No. 7 on combustion manager.
Switch on voltage supply.
Combustion manager drives to Standby.
Press [G] and [L/A] keys simultaneously.
Combustion manager changes to access level.
Press [+] key.
Combustion manager changes into the setting level for step points.
Preset P
9
Press [+] key.
Factory setting operating point P
9
(stage 2) is displayed.
Press and hold [L/A] key and set air damper setting determined using the [–] or
[+] key [ch. 7.1.3].
Press [Enter] and [L/A] simultaneously.
Factory setting fan speed (
100
%) is displayed.