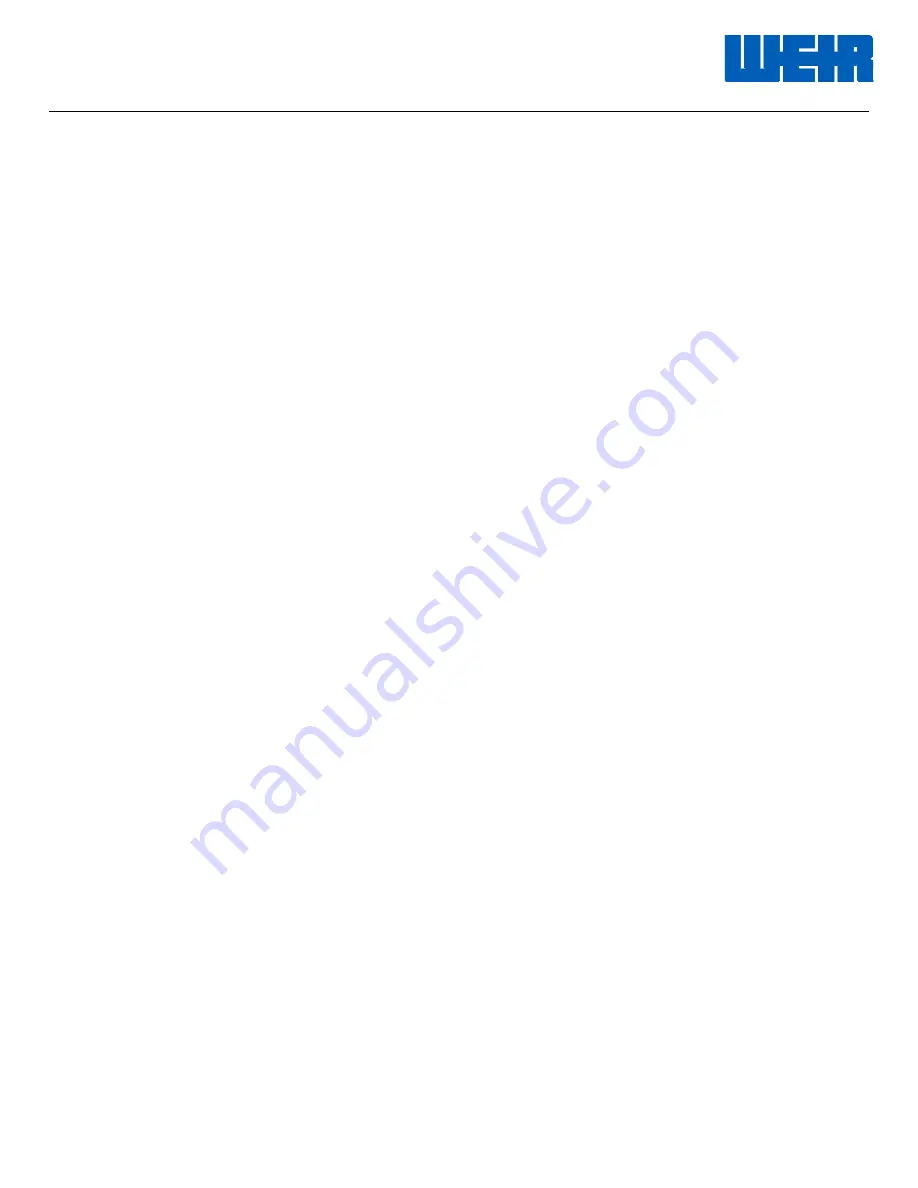
Document P/N: 2P136539
Release Date: 05/25/2017
Revision: F
33 of 42
SPM
®
QWS 2500 Fluid End Repair Procedures:
To remove Valves and seats:
1.
Using the SPM
®
2” hex cover wrench and a 6 pound Hammer, remove the suction and discharge
cover retainer nuts from the fluid cylinder.
2.
Using the SPM
®
butterfly tool, 1”-8 threaded rod and flat bar with nut; remove all five discharge
covers and all five suction covers.
3.
For Grooveless fluid ends; remove the suction valve stops following the reverse order of directions
within pages 37-40
4.
For Grooved fluid ends; turn the five suction valve stops by hand approximately 90 degrees and
remove them from the fluid cylinder. (see page 41)
5.
Remove all valve springs from the fluid cylinder suction side.
6.
Using an SPM
®
Magnetic Valve Removal Tool, cock each valve to one side in order to drain any
fluid trapped above it, and remove the valve from the cylinder. Follow the valve manufacturer’s
recommendation for removing the insert from the valve.
7.
Using an SPM
®
Hydraulic Seat Puller Assembly, remove all five discharge valve seats, and all five
suction valve seats from their tapered bores in the cylinder. The tapered bores should be
inspected, cleaned thoroughly, and lightly hand polished with a 220 to 240 grit emory cloth prior to
installation of new seats.
8.
Install a new o-ring seal on the valve seat prior to its installation in the fluid cylinder.
Each valve
seat must be installed dry –
never use grease, oil, or any other substance to coat the
tapered portion of the valve seat.
After installing the valve seat hand tight in the taper,
hammer it down tight into the taper using an old valve and a heavy steel bar.
9.
When installing new valve inserts, do not install one manufacturer’s valve insert on another
manufacturer’s valve. Likewise, when installing new valves, do not mix one manufacturer’s valve
with another’s valve seat. Install all ten valves in the valve seats.
10. Before installing the suction and discharge springs, check the free height of the spring.
11. Reinstall all ten valve springs carefully centering them on the valve. As you install the springs,
compress them to feel for even tension in the spring. If one is weak, replace it.
12. Reinstall the suction valve stop following the directions on pages 37-40 for Grooveless and 41 for
Grooved cylinders.
13. Before reinstalling the discharge and suction covers, clean the covers thoroughly, install new fluid
seals, and coat them with a light oil or grease. Inspect the primary seal backup for wear. Replace
if the backup has deteriorated. Clean the mating bores in the fluid cylinder and lightly hand polish
them with a 220 to 240 grit emory cloth. Reinstall the discharge covers and suction covers using
the SPM
®
Slide Hammer. Care must be taken to keep the discharge valve springs aligned
properly while installing the discharge covers.
14. Reference
SPM
®
technical bulletin BLLT1760 for proper retainer nut installation procedures.