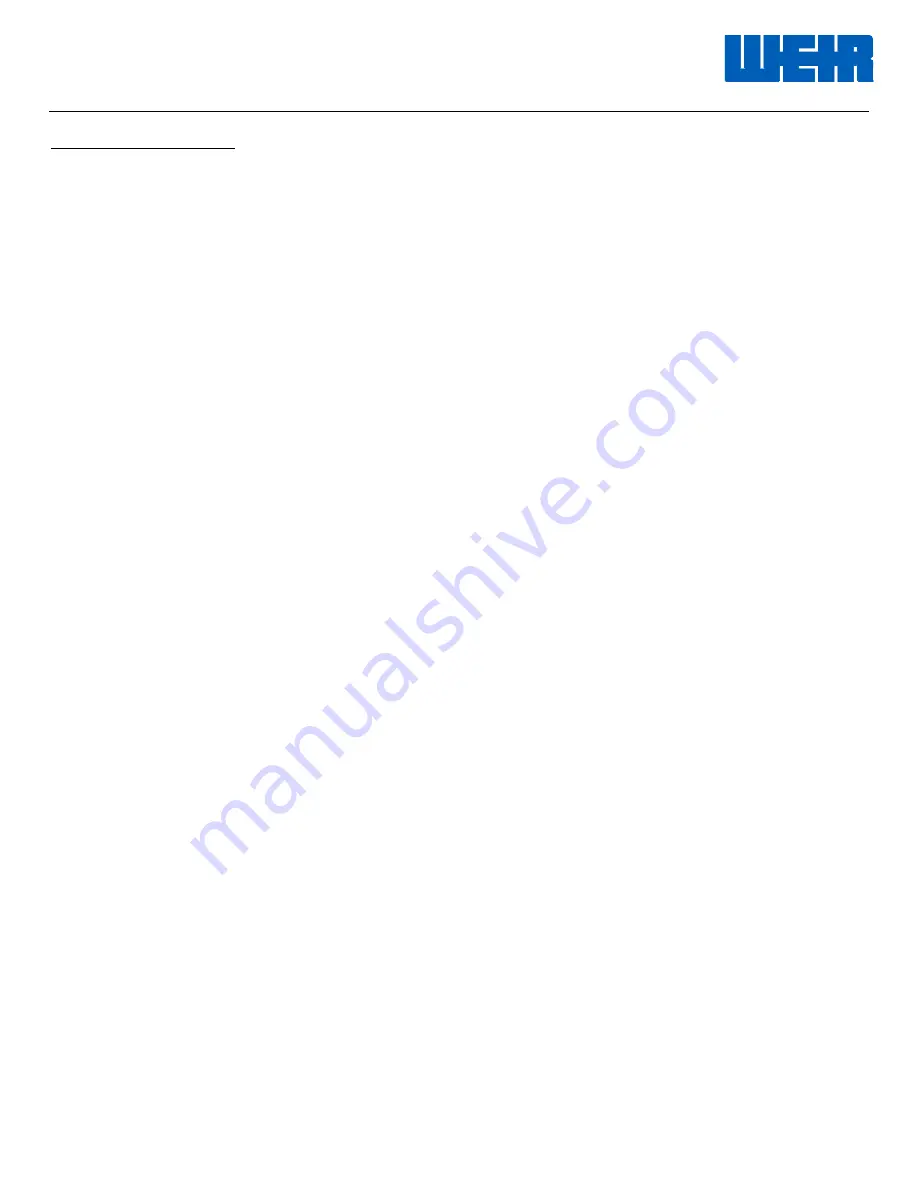
Document P/N: 2P136539
Release Date: 05/25/2017
Revision: F
22 of 42
Adequate Feed To Pump:
The Quintuplex fluid end is a relatively smooth operating unit. Its suction (and discharge) profile reflects a plus
2% and minus 5% variation from its average discharge rate (See Fig. 1). Nevertheless, this continual variation
in fluid demand (as much as 7%) can produce fluid dynamic problems.
The proper supply of fluid to the fluid end inlet is a complex issue. Sufficient initial pressure and recovery
capability of the charge pump (Item 2), and the use of a pulsation dampener (Item 4) only begin to address the
fluid dynamics requirement of the plunger pump.
Inadequate mixture of solids and liquids along with discharge fluid resonance can combine to create cavitation,
water hammer, and ultimate damage to the fluid end.
A balance must be struck as the fluid passes through the suction manifold and enters the fluid cylinder. Fluid
velocity should be sufficiently high to keep the solids in suspension, but not so much that friction robs the
charge pump’s ability to respond to the instantaneous demand of the plunger pump.
Due to space limitations, the suction manifold is generally mounted horizontally (See Fig. 2) and
fluid is usually provided to one end of the manifold. This arrangement requires the fluid to travel
horizontally and then make an abrupt 90
transition to enter the cylinder’s suction valves.
While this is the most popular method for manifolding, its limitations have become evident as rates and
pressures have increased, and liquid/solids compositions have changed. There is a strong evidence that the
fluid mixture can breakdown in the suction manifold resulting in solids separating from the liquid. This tendency
becomes more pronounced the further the fluid has to travel from the manifold inlet.
If there is sufficient solid separation, cavitation will ensue at that location. And resulting suction and discharge
valve damage can occur at the cylinder bore furthest from the manifold inlet. In extreme cases, damage to the
associated power end components can also occur.
SPM
®
strongly recommends the use of either the log style (Figure 2) manifold or the zoomie manifold.
A dual feed system can be created utilizing the standard “log” style manifold with a special attachment. The
sketch in Fig. 3 illustrates how a supplementary device can be added to allow fluid supply to both ends of the
manifold.
The zoomie style manifold is illustrated in Fig. 4.
Contact Weir Oil & Gas engineering for more material on these two styles.