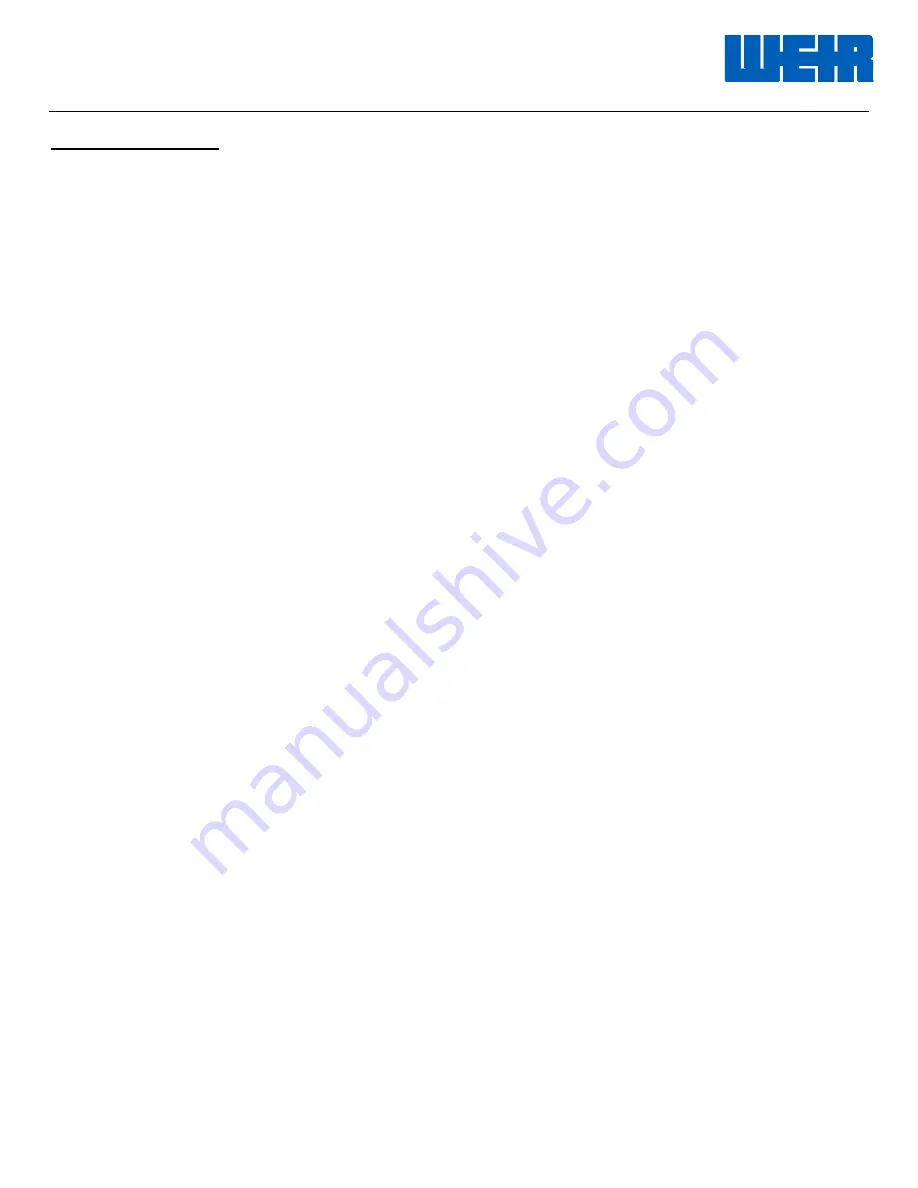
Document P/N: 2P136539
Release Date: 05/25/2017
Revision: F
5 of 42
Inspection & Testing:
1. Each pump, its drive system, and its fluid piping should be visually checked each time before operating.
All worn, damaged or missing parts should be remedied before starting the pump.
2. All fluid cylinder mounting nuts must be checked routinely with a certified torque wrench. Loose fluid
cylinder mounting nuts can cause the fluid end to separate from the power end resulting in
SERIOUS
INJURY OR DEATH.
3. All studs and stay rods require tightening to the proper torque. Without proper torque, the fluid end will
"breathe" or flex against the power end resulting in stud failure, stay rod failure and/or even premature
fatigue failure in the power or fluid end. Ensure all stay rods are not damaged, cracked, or loose.
Consult Weir Oil & Gas for torque information (see assembly drawings for torque values).
4. All covers must be tight and properly torqued. Otherwise, premature fatigue and possible fluid end or
component failure can result.
5. All fluid ends must be disassembled, and dimensionally inspected routinely. Any fluid cylinder or
discharge flanges which exhibits any loss in wall thickness due to washing or corrosion pitting in any
area must be returned to Weir Oil & Gas for repair and recertification prior to operating again.
6. All fluid cylinders in operation must be disassembled and inspected for cracks. Fluid cylinder inspection
should occur on a monthly basis or every 100 hours of operation. The operation of any pump with even
small surface cracks in any area of the fluid cylinder can result in equipment failure and
SERIOUS
INJURY OR DEATH
.
7. All fluid cylinders should be hydrostatically tested at least twice each year by a qualified technician.
Prior to any pressure testing, all air must be evacuated from the system. Failure to do so could result in
PERSONAL INJURY OR DEATH.
The maximum test pressure must not exceed the equipment's rated
working pressure. The hydrostatic pressure test must be followed with an ultraviolet light/magnetic
particle inspection of the internal bores prior to reinstalling and operating under pressure.
8. Once an SPM
®
fluid end assembly has been pressurized, transfer of the following components into any
other fluid end assembly is prohibited:
Packing
Nuts
Retainer
Nuts
Discharge
Flanges
Discharge Gauge Connections
Discharge Gauge Connection Retainer Nuts
Discharge Flange Studs and Nuts
Suction
Covers
Discharge
covers.
NOTE
: It is always best practice that sealing/ soft components such as D-Rings, O-Rings, and Discharge
Flange Seal Rings be replaced each time they are disassembled.