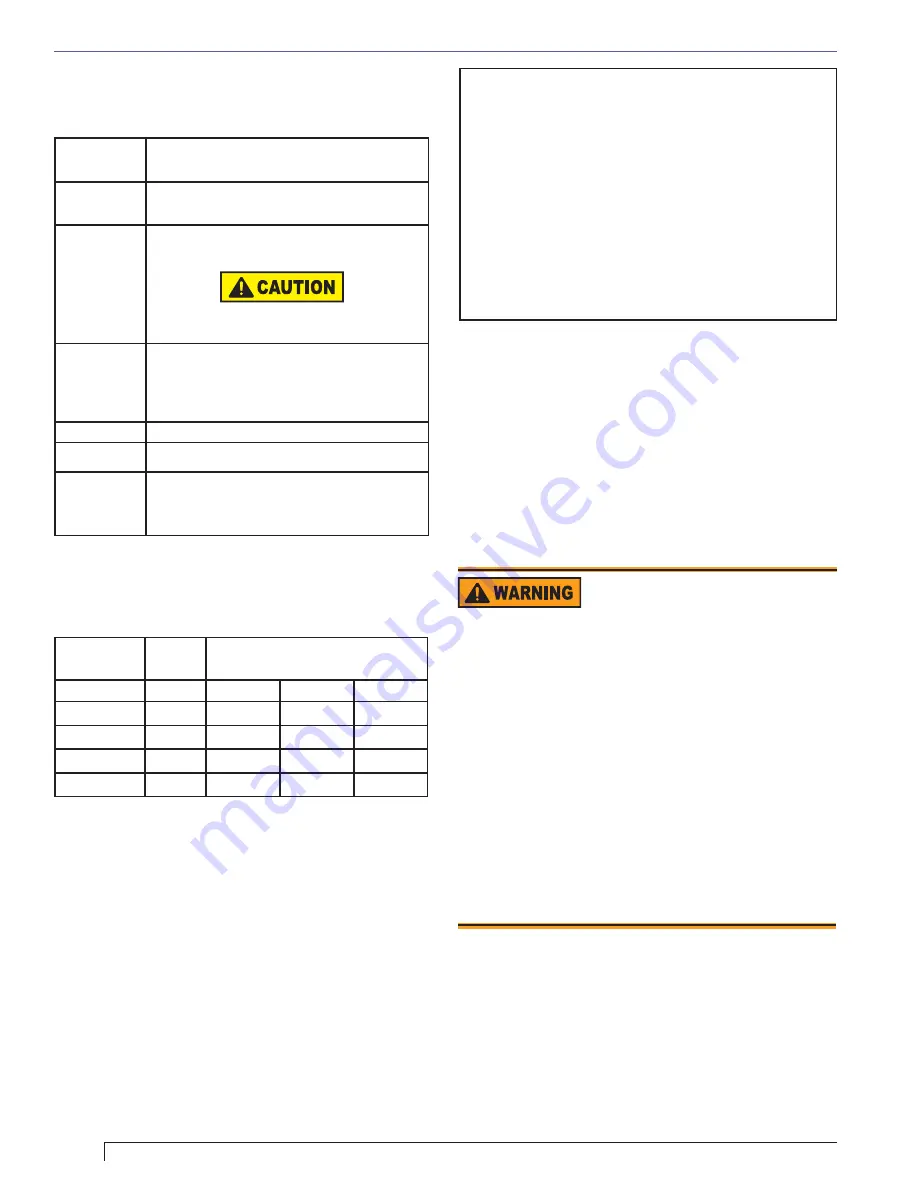
6
Certifi cations/approvals
Underwriters Laboratories has certi
fi
ed this burner
to comply with ANSI/UL 296 and CSA-B139.
Low
sulfur #1 and #2 fuel oils reduce heat exchanger
deposits with all burners compared to the standard
fuels. Reduced deposits extend the service
interval for cleaning and improve the effi ciency of
the appliance over time. Low sulfur fuels reduce
particulate and oxides of nitrogen emissions as
well. The Oilheat Manufacturers’ Association
recommends these fuels as the preferred fuels for
this burner.
Notice Special Requirements
THE INSTALLATION OF A BURNER SHALL BE IN
ACCORDANCE WITH THE REGULATIONS OF
AUTHORITIES HAVING JURISDICTION.
For recommended installation practices in the U.S.
refer to the latest edition of NFPA 31. (CSA-B139
and CSA-B140 in Canada.
Concealed damage — If you discover damage to
the burner or controls during unpacking, notify the
carrier at once and
fi
le the appropriate claim.
When contacting Beckett for service information
— Please record the burner serial number (and have
available when calling or writing). You will
fi
nd the
serial number on the silver label located on the left
rear of the burner. Refer to Figure 1.
○
○
○
○
Starting with minimum gph
fi
ring rate, the minimum
size recommended is 6”
fl
ue pipe with 8” X 8”
inside chimney, unless speci
fi
ed otherwise by the
appliance manufacturer.
A chimney
fl
ue shall extend at least 3 feet above
the highest point at which the chimney comes in
contact with the roof, and not less than 2 feet above
the highest roof surface or structure within 10 feet
horizontally of the chimney. Refer to Figure 2.
1.
2.
Table 3. – Air Tube Combinations (ATC)
Firing rate
(gph)
Head
ATC codes for usable air tube
lengths:
(min-max)
5”
7”
9”
0.40-1.35
9-Slot
NX50LB
NX70LB
NX90LB
0.40-1.35
6-Slot
NX50LC
NX70LC
NX90LC
1.10-1.75
9-Slot
NX50LD
NX70LD
NX90LD
1.10-1.75
6-Slot
NX50LF
NX70LF
NX90LF
Inspect/Prepare
Installation Site
Clearances to Burner and Appliance
Provide space around burner and appliance for ease
of service and maintenance. Check the minimum
clearances against those shown by the appliance
manufacturer and by applicable building codes.
Inspect Chimney or Direct Vent System
General Information
Table 2. – Burner Specifi cations
Capacity
LB & LC
Firing rate: 0.40 – 1.35 GPH
Input: 56,000 – 189,000 Btu
Capacity
LD & LF
Firing rate: 1.10 - 1.75 GPH
Input: 154,000 – 245,000 Btu/h
Fuels
U. S.
No. 1 or No. 2 heating oil only (ASTM D396)
Canada
No. 1 stove oil or No. 2 furnace oil only
Electrical
Power supply:
120 VAC, 60 Hz, single phase
Operating load:
5.8 Amps max
Motor:
1/7 hp, 3450 rpm, NEMA 48M frame
PSC rotation CCW when facing shaft end
Ignition:
Continuous duty solid-state igniter
Fuel pump
Outlet pressure - See Note 1
Air tube
ATC code - See Table 3
Dimensions
(with cover)
Height (maximum): 12-1/2 inches
Width (maximum): .15 inches
Depth: 9-1/4 inches
Air tube diameter: 3-1/4 inches
*
Note 1. See appliance manufacturer’s burner specifi cations for recom-
mended outlet pressure.
DO NOT USE GASOLINE, CRANKCASE
OIL, OR ANY OIL CONTAINING GASOLINE.
Carefully inspect the chimney or exhaust vent
system.
Make sure it is properly sized and in good working
condition.
Follow the instructions supplied by the appliance
manufacturer.
The installation must strictly comply with all
applicable codes, authorities having jurisdiction and
the latest revision of the National Fire Protection
Association Standard NFPA 31 for the installation of
chimneys and vent sizing, (or CSA-B139 and CSA-
B140 in Canada).
Regulation by these authorities take precedence
over the general instructions provided in this
installation manual.
y
y
y
y
y
Fire, Smoke & Asphyxiation
Hazard
Section: General Information & Inspect/Prepare Installation SIte
Summary of Contents for UO-3 CV
Page 2: ...2...