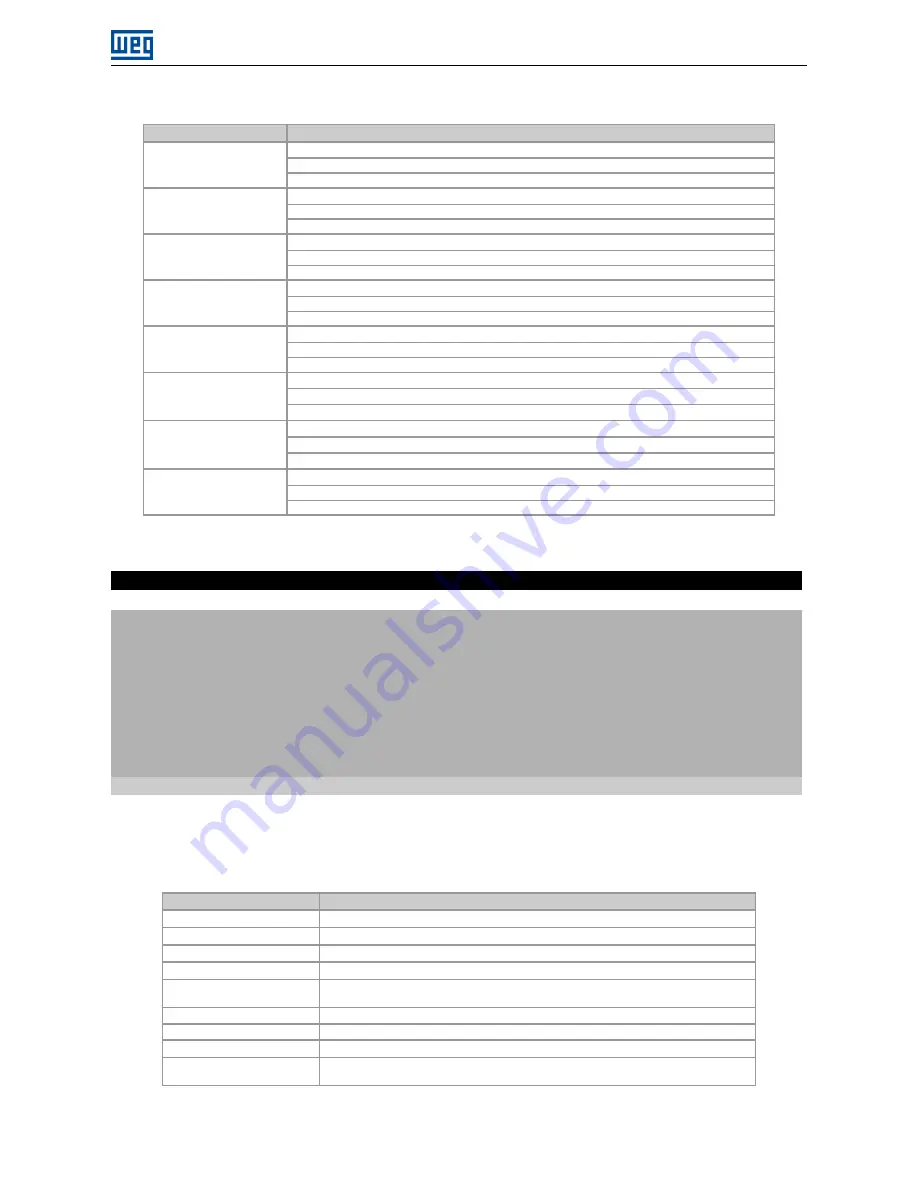
Programming
Table 5.4:
Remote Commands of parameter P0682
Operation Mode
Command
P0202 = 0
Transparent
Command 1
No function.
Command 2
No function.
Command 3
No function.
P0202 = 1
Overload Relay
Command 1
No function.
Command 2
No function.
Command 3
No function.
P0202 = 2
Direct Starter
Command 1
0
→
1 turns off the motor.
Command 2
0
→
1 turns on the motor.
Command 3
No function.
P0202 = 3
Reverse Starter
Command 1
0
→
1 turns off the motor.
Command 2
0
→
1 turns on the motor in forward direction.
Command 3
0
→
1 turns on the motor in reverse direction.
P0202 = 4
Star-Delta Starter
Command 1
0
→
1 turns off the motor.
Command 2
0
→
1 turns on the motor.
Command 3
No function.
P0202 = 5
Dahlander Starter
Command 1
0
→
1 turns off the motor.
Command 2
0
→
1 turns on the motor with high speed.
Command 3
0
→
1 turns on the motor with low speed.
P0202 = 6
Pole-Changing Starter
Command 1
0
→
1 turns off the motor.
Command 2
0
→
1 turns on the motor with high speed.
Command 3
0
→
1 turns on the motor with low speed.
P0202 = 7
PLC Mode
Command 1
No function.
Command 2
No function.
Command 3
No function.
P0751 – ETHERNET COMMUNICATION STATUS
Range:
0 = Setup
1 = Init
2 = Wait Comm
3 = Idle
4 = Data Active
5 = Error
6 = Reserved
7 = Exception
8 = Access Error
Default:
-
Properties:
RO
Description:
It allows identifying the Ethernet communication status.
Table 5.5:
P0751 indications
Indication
Description
0 = Setup
Module identified, waiting configuration data (automatic).
1 = Init
Module performing interface initialization procedure (automatic).
2 = Wait Comm
Initialization finished, but no communication with master.
3 = Idle
Communication with master established, but in Idle mode or Program mode.
4 = Data Active
Communication with master established and performing normal I/O data handling. ”On-
line”.
5 = Error
Communication error detected.
6 = Reserved
Reserved
7 = Exception
Major fault detected by the Ethernet interface. Requires interface reinitialization.
8 = Access error
Major fault detected between device and Ethernet interface. Requires interface reinitia-
lization.
SRW01-ETH | 16