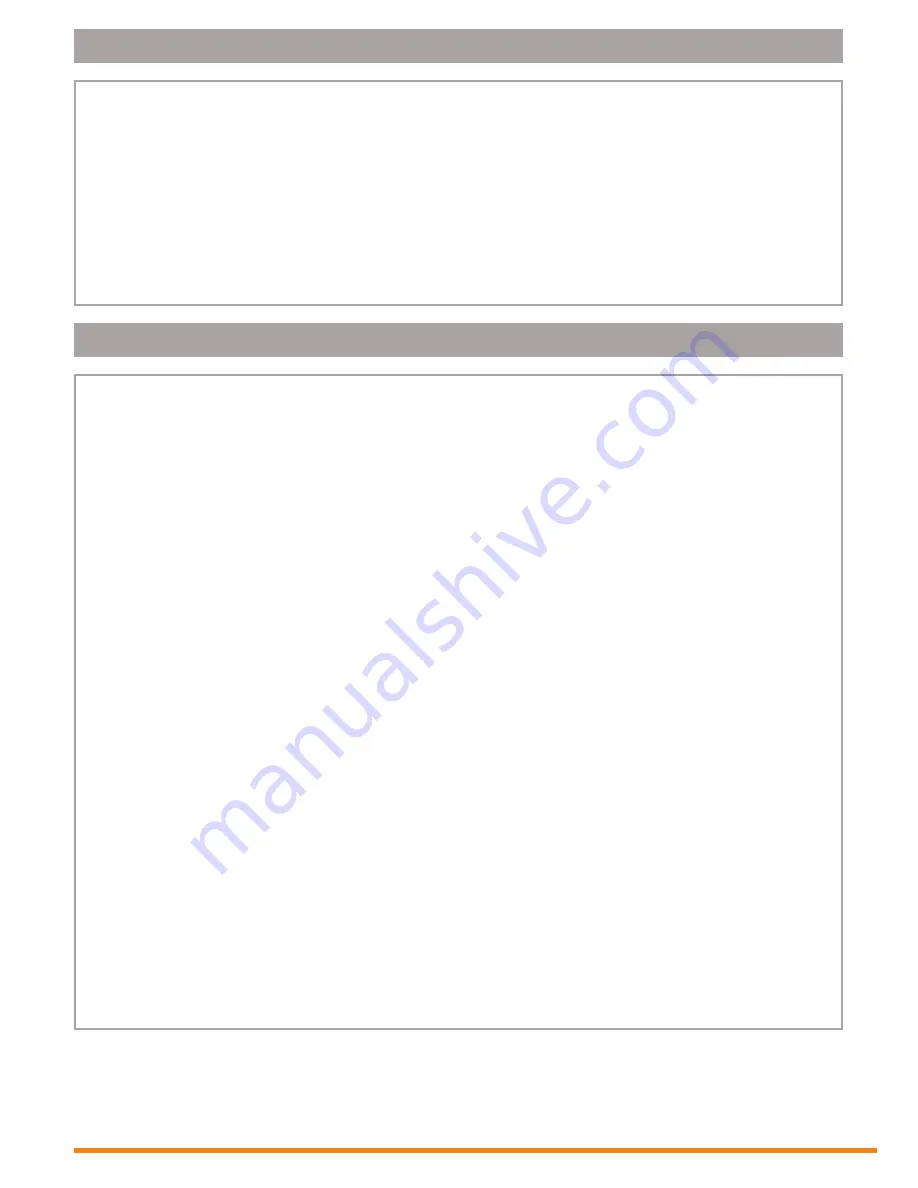
ELECTRICAL CONNECTION
Connection of the shield
For signal transmission always use shielded cables. The cable shielding must be connected properly
to the metal ring nut of the connector in order to ensure a good earthing through the frame of the
device.
Ground connection
Minimize electronic noise by connecting the shield and/or the connector housing and/or the sensor
to ground. Make sure that ground is not affected by electronic noise. The connection point to ground
can be situated both on the device side and/or on user’s side. The best solution to minimize the inter-
ference must be carried out by the user.
SIGNAL DESCRIPTION
0 VDC
0 VDC Power Supply and 0 VDC analog are internally connected.
START input
START input is used to execute the TEACH-IN procedure. It is active at HIGH logic level (voltage greater
than 10 V must be applied). For any further information on using the START and STOP inputs please
refer to the “TEACH-IN procedure” section.
+I out current analog output
+I out provides the current analog signal. AI1 output range is: min. quote = 4 mA, max. quote = 20 mA.
The increment at each step is as follows: 10-bit DAC
4...20 mA: 16000/1024 = 15.625 μA
+V out voltage analog output
+V out provides the voltage analog signal. AV2 output range is: min. quote = 0 V, max. quote = 10 V
The increment at each step is as follows: 10-bit DAC
0...10 V: 10000/1024 = 9.765 mV
STOP input
STOP input is used to execute the TEACH-IN procedure. It is active at HIGH logic level (voltage greater
than 10 V must be applied). For any further information on using the START and STOP inputs please
refer to the “TEACH-IN procedure” section.
Fault output
This Fault output is only available for AI1 current analog output. It is intended to show an error
condition such as a circuit break.
Please pay attention to the value of the R2 resistor.
Imax = 50 mA
R1 = 47 Ω
R2 = (VDC/I) - R1
No encoder error = transistor ON (conducting)
Encoder error = transistor OFF (open)