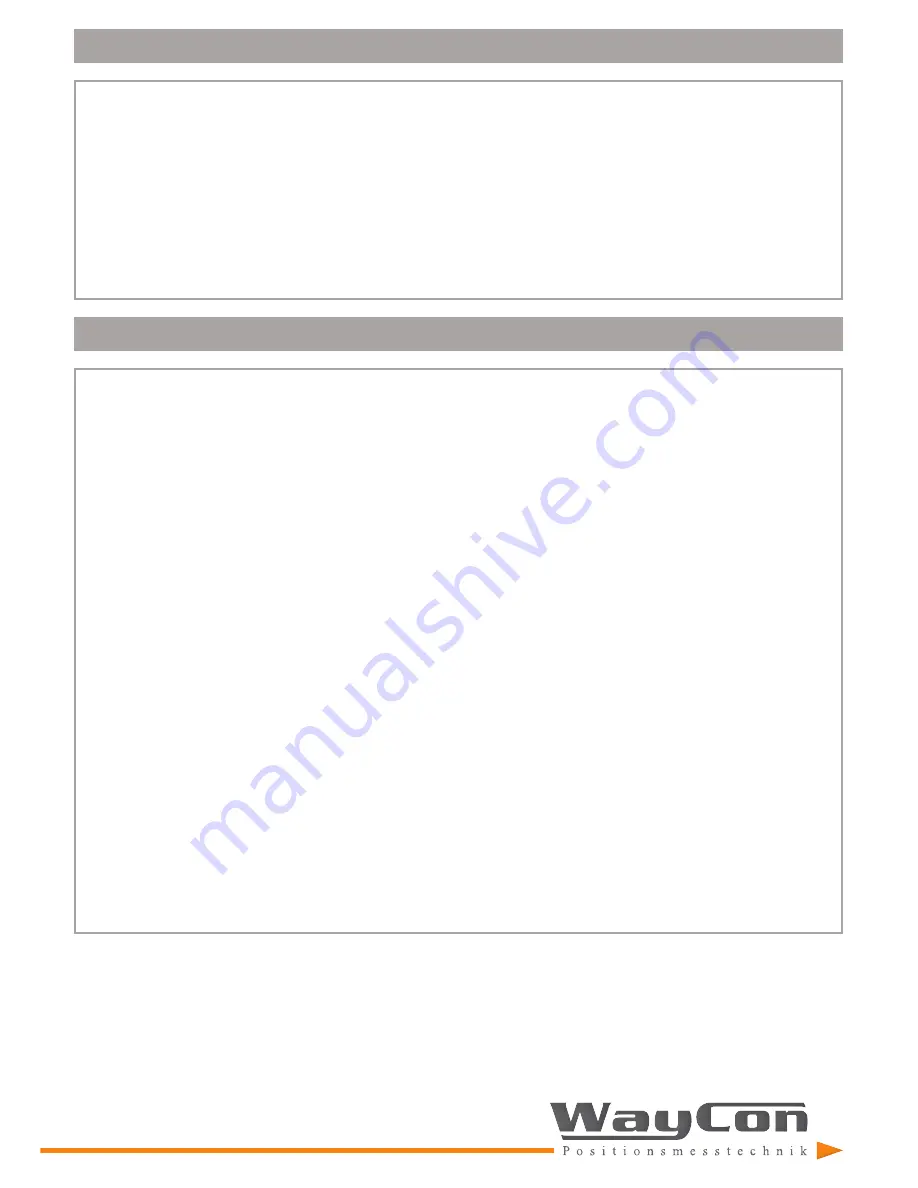
MAINTENANCE
The magnetic measurement system does not need any particular maintenance. Please always consider
it is a sensitive electronic equipment and therefore it must be handled with care. From time to time we
recommend the following operations:
• Periodically check the proper assembly of the sensor system and make sure that there are no loose
screws, tighten them if necessary.
• Check the mounting tolerances between the sensor and the magnetic scale all along the measuring
length. Wear of the machine may increase the tolerances.
• The surface of the magnetic scale should be cleaned periodically by using a soft cloth to remove
dust, chips, moisture etc.
TROUBLESHOOTING
The following list shows some typical faults that may occur during installation and operation of the
magnetic measurement system.
Fault
: The system does not work (no pulse output).
Possible cause:
• The tape or the sensor has been mounted incorrectly (the active part of the tape does not match the
active side of the sensor).
• A magnetic part or a protection surface is interposed between the sensor and the tape. Only non-
magnetic materials are allowed between the sensor and the tape.
• Installation does not comply with the tolerance gap between the sensor and the scale indicated
in this guide. The sensor hits the surface of the scale or is too far from it. Check whether the sensor
sensitive part is damaged.
• The sensor has been damaged by a short circuit or a wrong connection.
Fault
: The measured values are either inaccurate or not provided in the whole length.
Possible cause:
• The mounting tolerances between the sensor and the tape are not met all along the whole
measurement length.
• The connection cable is located next to a high voltage cable. or the shielding is not connected
correctly. Check the earthing point.
• A section of the magnetic scale has been damaged mechanically or magnetically along the
measuring length.
• The measuring error is caused by torsion of the machine structure. Check parallelism and symmetry
of machine movement.