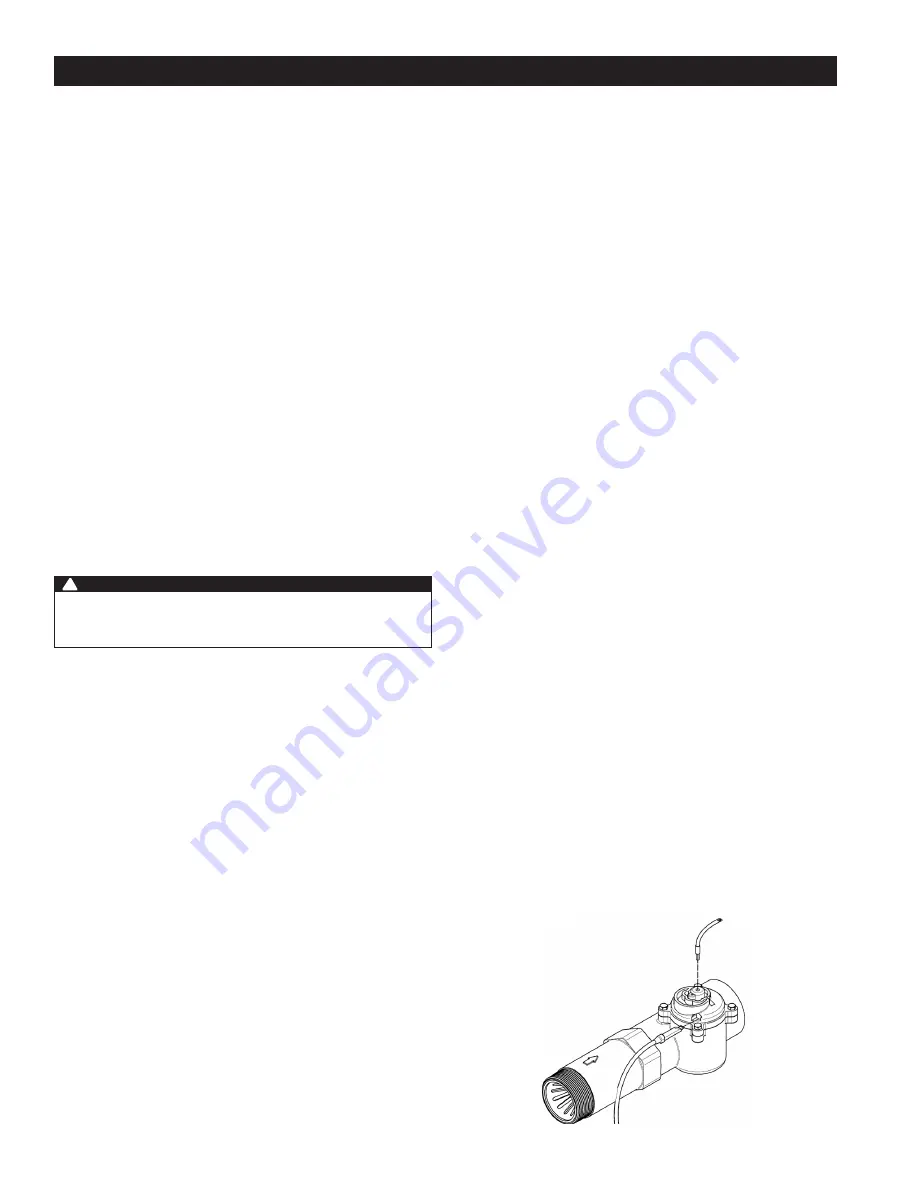
10
System Installation
7*. Connect the cold water supply to the inlet port of the water
softening system’s control valve(s). When constructing the
supply line, install an inlet water isolation valve and plumbing
union fitting (user supplied) in the supply line of each control
valve and close the isolation valve. The union fitting(s) should be
located between the isolation valve and the systems inlet port.
8*. Install an inlet water sample port in the supply line and close it.
9*. If risk of vacuum exists, install Watts # 0556031 vacuum
relief valve in the supply line to protect the system against
vacuum damage.
10*. Connect the outlet water connection of the water meter(s)
for HC-200 and HCP-200 systems, and the control valve
outlet water ports for HCTA-200 systems, to the water line
requiring softened water. When constructing this outlet water
line, install an outlet water isolation valve and plumbing union
fitting (user supplied) in the outlet line of each control valve
and close the isolation valve. The union fitting(s) should be
located between the outlet of the control valve(s) and the
outlet isolation valve(s).
11*. Install an outlet water sample port on the outlet water line of
the system and close it.
12*. Install a bypass valve between the inlet and outlet plumbing
water lines and close it.
13*. If not already factory installed on the control valve, attach the
drain line flow controller directly to the control valve’s drain
port. See page 11 for connection detail. The flow arrow on
the drain line flow controller must point towards the drain
receptacle. Only plumbing tape is allowed on the drain line
flow controller fitting threads.
14*. Construct the drain line routing it to an appropriate drain recep-
tacle abiding buy all local building and plumbing codes. DO
NOT construct drain line to elevations that exceed 4 feet above
the drain port of the control valve, or reduce the drain line diam-
eter to smaller than that of the drain line flow controller. Install a
plumbing union fitting in the drain line close to the drain line flow
controller. The drain line must be anchored to the floor.
15*. Connect the brine tank to the water softener’s control valve
brine port using the factory supplied fittings and tubing. See
page 11 for connection detail. The brine tank should set on
a common elevation as the mineral tank and within distance
so that it can be reached by the length of factory supplied
brine tubing. Add enough water (6") to the brine tank so that
water covers the top of the air check. DO NOT add salt to
the brine tank at this time.
16. Connect meter cable(s) into meter dome(s) according to Figure
1. NXT2 & SXT controller meter cable(s) must use side port on
meter dome(s). Connect the other end of the meter cable(s)
to the control valve’s P5 port located on the control valve’s
controller of the control valve the meter is plumbed into. For
HCTA-200 series systems, connect the meter cable to a single
control valve controller. See pages 14 & 15 for P5 location.
17. Connect the 24V transformer power supply wire(s) to the
P14 port(s) of the control valve controller(s). See pages
14 & 15 for P14 location.
18. If applicable, install a metal bonding strap across metal inlet
and outlet plumbing lines to maintain electrical continuity.
The system is now ready for Start Up.
* See Installation Diagrams pages 11–13 of this manual for
additional information.
WARNING
!
Operating a system without a drain line flow controller will
cause all media to flow out of the system through the
drain line.
Start Up Instructions
1. Ensure all inlet and outlet isolation valves and the bypass
valves are in the closed position and the treated water faucet
hot and cold side are in the open position.
2. Open the main water supply valve to the building.
3. Check for leaks and repair as needed.
4. Plug the power cord of the control valve into an electrical
outlet to energize system.
5. Locate “Manually Initiating a Regeneration” on page 18 of
this manual and follow the steps to place the system into the
backwash position. Once the system cycles into the back-
wash position, unplug the control valve from the power outlet
to keep the system in the backwash position.
6. Open the inlet isolation valve slightly until water can be heard
flowing through the isolation valve and allow the mineral tank
to fill with water. Air will come out of the drain line until the
mineral tank is full of water. Once water flow at the drain line
is observed, fully open the inlet valve and allow water flow
to drain for 10 minutes to flush the resin bed of any color. If
water at the drain shows any discoloration, continue to flush
the resin bed until water at the drain is clear.
7. After resin bed flushing is complete, plug the system back in
to the power outlet so that it will return to the service position.
Repeat steps 4, 5, 6 and 7 on the other tank(s) if this is a Series
HCTA-200 Duplex Alternating or HCP-200 Progressive system.
8. For HCP-200 or HCTA-200 series systems, connect the
factory supplied inner-connecting communication cable(s)
between the P1 and P3 ports of the control valve’s controllers
shown on pages 14 & 15.
9. Program the system according to the System Type (see page 20)
following the Control Valve Programming section beginning
on page 21.
10. Put the appropriate amount of water in the brine tank(s). This
is accomplished by manually cycling the control valve(s) to
cycle step 4 “Brine Tank Refill” and allowing a complete brine
tank refill cycle to conclude. This step must be done for each
brine tank in the system only after the proper brine tank refill
time has been programmed into each controller.
11. Put the appropriate amount of salt in each brine tank. Do Not
fill the salt level past the brine well lid.
12. Fully open the outlet isolation valve(s).
13. Ensure the bypass valve is in the closed position.
14. Check for leaks and repair as needed.
15. Allow water to flow from the hot and cold side treated faucet
until all air has been purged from the plumbing system. Then
close both the hot and cold side treated water faucet.
16. Turn on water heaters.
Start up is now complete and the system is ready for operation.
Figure 1
Mechanical Meter Cable Inserts Into
Top Center Port of Meter Dome
Electronic Meter Cable for NXT2 & SXT
Controllers Inserts Into Side Port of Meter Dome