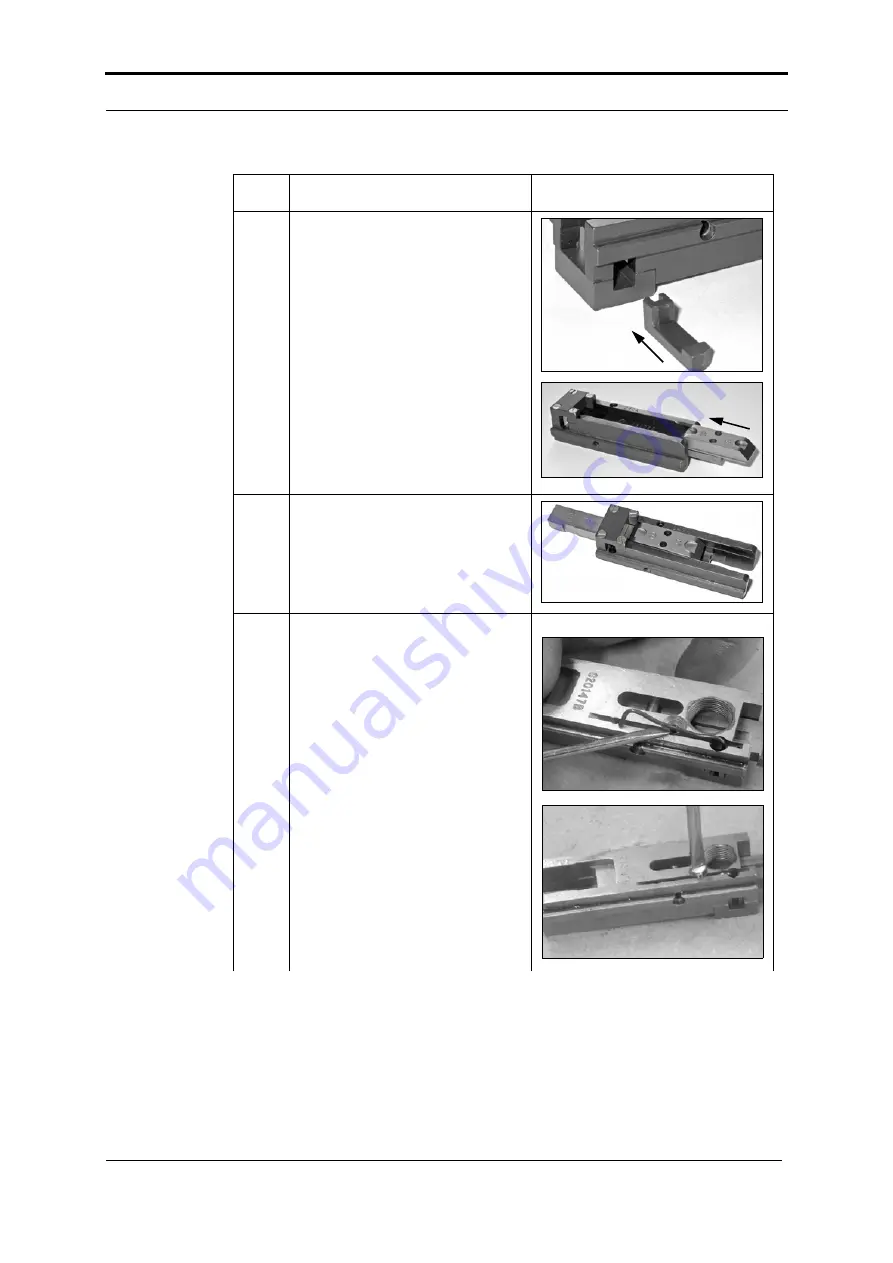
3 - Fit the New Parts - Replace the Bender Bar Components
G8 Stitch Head Maintenance Kit Instructions
47
5
Apply grease to all faces of the
bender bar latch.
Apply grease to the inside faces of
the bender bar where the driver
bar runs.
Fit the bender bar latch and the
new driver bar assembly to the
bender bar.
6
Push the driver bar assembly to
the end of the bender bar.
7
Fit the bender bar latch spring and
the bender bar latch spring screw.
Step
Action
Information