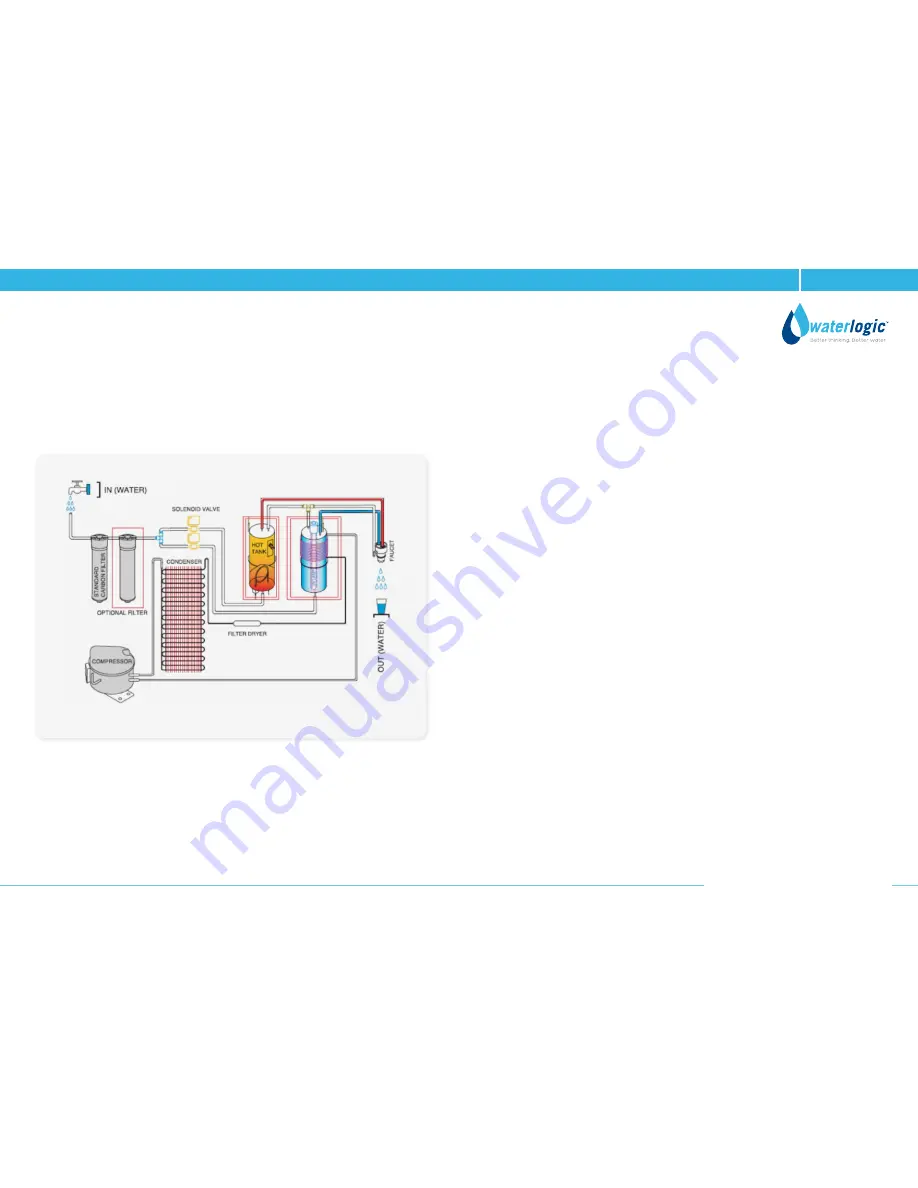
8
9
Waterlogic 2000IT Technical Manual - Issue B, December 2013
Pre Delivery
Inspection Procedures (PDI)
CAUTIONS:
• Only competent trained technicians should work on Waterlogic products.
• Waterlogic units may weigh over 25KG. We recommend caution when lifting.
• Packing materials could present a trip hazard. Keep them off the floor.
• Take care not to allow the power lead to get wet. If the lead gets wet it must
not be used.
1.
Unpack and carry out a visual inspection of the unit for any transit damage.
2.
Remove the top cover and the lower front panel and visually inspect the
internal parts of the machine for any wires or pipes that may have come loose
in transit including the Quartz Sleeve.
3.
Connect the water supply.
4. Ensure the switch on the rear of the machine is in the off position and
connect the unit to a power supply.
5
. The unit is now live and suitable safety precautions should be taken.
6.
Flush water (approximately 10 litres) through the hot tank first until the water
runs clear of any carbon fines.
7.
Now flush water through the Cold Tank with approximately 10 litres (20 litres
if cold only).
8.
Once you are sure that water is running through both the cooling and
heating circuit then turn on the heater and compressor switch at the rear of the
machine.
9
. Carry out a visual inspection for any water leaks.
10.
The hot water will heat to approximately 85°C.
11.
To test the cold water wait until the compressor has shut off. Test the 2nd
cup of water taken. It should be between 5 and 8°C.
12
. Inspect the cold water produced for clarity and taste. If required flush more
water to remove any adverse taste or carbon fines.
13
. Return the switch to the off position and isolate the power and water to the
machine.
14.
Drain the hot tank and cold tank.
15.
Replace all panels, clean the machine and repack the machine.
16.
Waterlogic recommend that all units are fully electrically (PAT) tested on
site by the commissioning engineer as damage may have occurred during
transit to the unit’s final destination.
Wetted Parts Layout
Hot and Cold