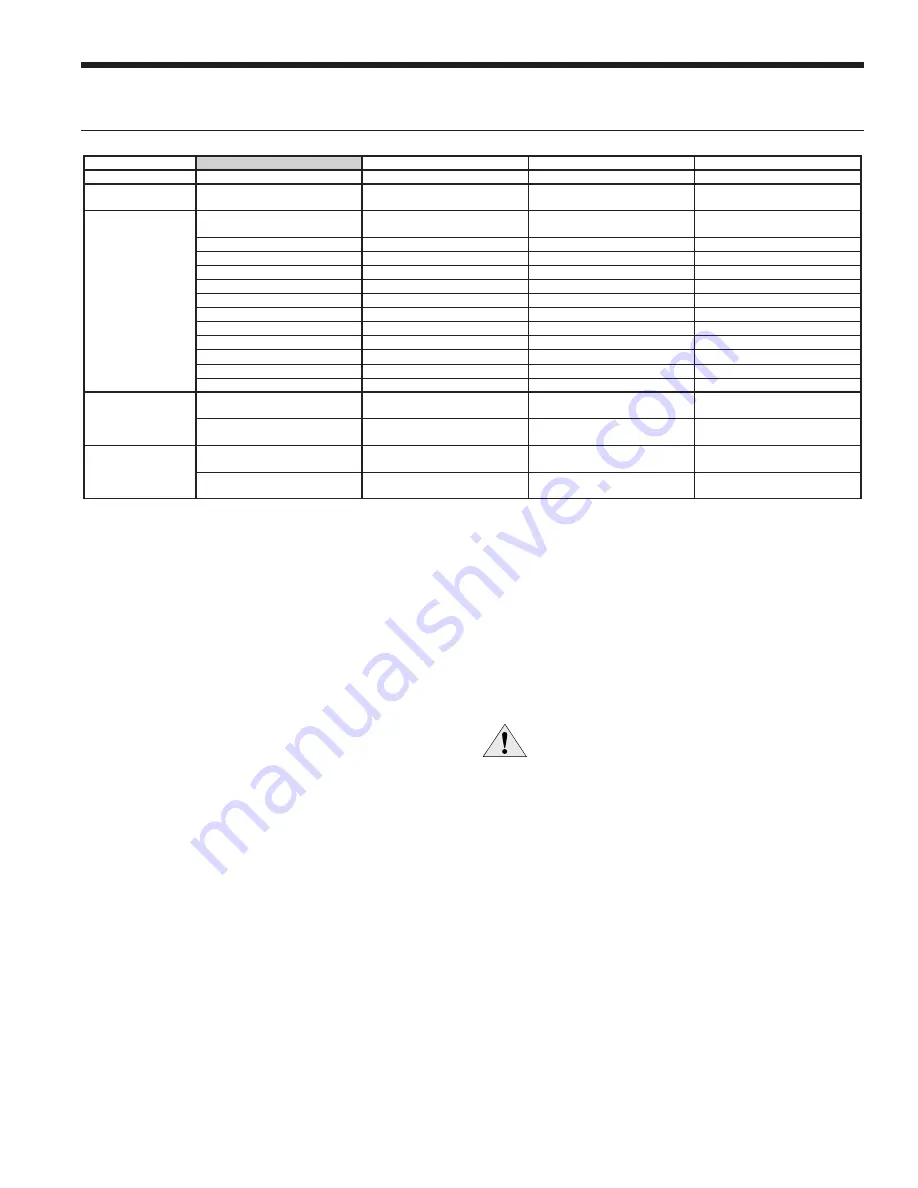
7
5 SERIES OPTIHEAT 504W11 INSTALLATION MANUAL
Field Connected Water Piping cont.
Material
Copper
90/10 Cupronickel
316 Stainless Steel
pH
Acidity/Alkalinity
7 - 9
7 - 9
7 - 9
Scaling
Calcium and
Magnesium Carbonate
(Total Hardness)
less than 350 ppm
(Total Hardness)
less than 350 ppm
(Total Hardness)
less than 350 ppm
Corrosion
Hydrogen Sulfide
Less than 0.5 ppm (rotten egg
smell appears at 0.5 ppm)
10 - 50 ppm
Less than 1 ppm
Sulfates
Less than 125 ppm
Less than 125 ppm
Less than 200 ppm
Chlorine
Less than 0.5 ppm
Less than 0.5 ppm
Less than 0.5 ppm
Chlorides
Less than 20 ppm
Less than 125 ppm
Less than 300 ppm
Carbon Dioxide
Less than 50 ppm
10 - 50 ppm
10 - 50 ppm
Ammonia
Less than 2 ppm
Less than 2 ppm
Less than 20 ppm
Ammonia Chloride
Less than 0.5 ppm
Less than 0.5 ppm
Less than 0.5 ppm
Ammonia Nitrate
Less than 0.5 ppm
Less than 0.5 ppm
Less than 0.5 ppm
Ammonia Hydroxide
Less than 0.5 ppm
Less than 0.5 ppm
Less than 0.5 ppm
Ammonia Sulfate
Less than 0.5 ppm
Less than 0.5 ppm
Less than 0.5 ppm
Total Dissolved Solids (TDS)
Less than 1000 ppm
1000 - 1500 ppm
1000 - 1500 ppm
LSI Index
+0.5 to -0.5
+0.5 to -0.5
+0.5 to -0.5
Iron Fouling
(Biological Growth)
Iron, FE
2
+ (Ferrous)
Bacterial Iron Potential
< 0.2 ppm
< 0.2 ppm
< 0.2 ppm
Iron Oxide
Less than 1 ppm, above this
level deposition will occur
Less than 1 ppm, above this
level deposition will occur
Less than 1 ppm, above this
level deposition will occur
Erosion
Suspended Solids
Less than 10 ppm and filtered
for max. of 600 micron size
Less than 10 ppm and filtered
for max. of 600 micron size
Less than 10 ppm and filtered
for max. of 600 micron size
Threshold Velocity
(Fresh Water)
< 6 ft/sec
< 6 ft/sec
< 6 ft/sec
NOTES:
Grains = ppm divided by 17
mg/L is equivalent to ppm
2/22/12
Water Treatment
Do not use untreated or improperly treated water.
Equipment damage may occur. The use of improperly
treated or untreated water in this equipment may result in
scaling, erosion, corrosion, algae or slime. Purchase of a pre-
mix antifreeze could significantly improve system reliability
if the water quality is controlled and there are additives in
the mixture to inhibit corrosion. There are many examples
of such fluids on the market today such as Environol™ 1000
(pre-mix ethanol), and others. The services of a qualified
water treatment specialist should be engaged to determine
what treatment, if any, is required. The product warranty
specifically excludes liability for corrosion, erosion or
deterioration of equipment.
The heat exchangers and water lines in the units are copper
or cupronickel tube. There may be other materials in the
buildings piping system that the designer may need to take
into consideration when deciding the parameters of the
water quality. If antifreeze or water treatment solution is
to be used, the designer should confirm it does not have a
detrimental effect on the materials in the system
.
Contaminated Water
In applications where the water quality cannot be held to
prescribed limits, the use of a secondary or intermediate
heat exchanger is recommended to separate the unit fro
the contaminated water. The table above outlines the
water quality guidelines for unit heat exchangers. If these
conditions are exceeded, a secondary heat exchanger is
required. Failure to supply a secondary heat exchanger
where needed will result in a warranty exclusion for primary
heat exchanger corrosion or failure.
WARNING: Must have intermediate heat exchanger
when used in pool and spa applications.
Summary of Contents for 5 Series 504W11 OptiHeat
Page 2: ......
Page 46: ...46 5 SERIES OPTIHEAT 504W11 INSTALLATION MANUAL Notes...