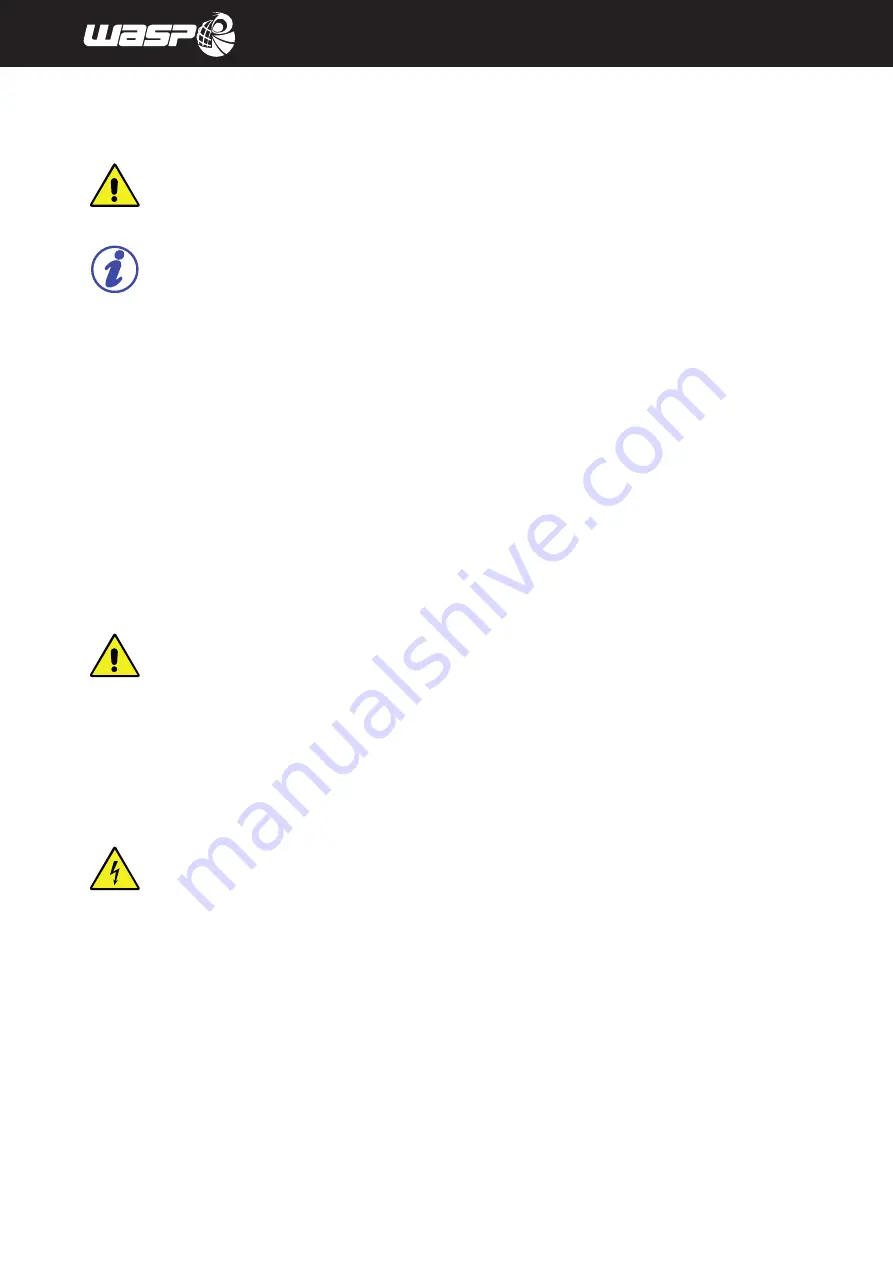
INTRODUCTION
© WASP S.r.l.
1
9
1
1.5. General safety warnings
CAUTION:
All intervention performed on the printer require particular caution on the part of the operator.
NOTE:
Any intervention on the printer must be carried out in strict compliance with the operational skills
(see paragraph 1.7.1 “Identification of Operational Staff”). WASP S.r.l. declines any responsibility in
case of non-compliance with these skills.
The purpose of this chapter is to indicate:
•
which are the specific measures to avoid incurring any kind of accidents
•
what may be defined as residual risks
•
which are the minimum essential safety provisions to be maintained
•
what characteristics must have the operators assigned to the operations on the machine
•
which must be the characteristics of the maintenance operators.
WASP is not responsible for unspecified operations, as they are considered strictly pertinent to technical
assistance personnel or for operations performed differently from what we described in the documentation
presented.
Possible operations on the printer can include:
• Mechanical
• Electrical
MECHANICAL NATURE INTERVENTIONS
Any intervention of a mechanical nature must be carried out in strict compliance with the directives required by
current safety regulations. It is absolutely forbidden to perform any type of mechanical maintenance intervention
on the printer during the operating cycle or in any case with parts of the printer moving.
Every mechanical operation must be carried out with the printer stopped and only and exclusively by the mechanical
maintenance technician, qualified to operate in conditions of safety (see paragraph 1.7.1 “Identification of the
operating personnel”).
Maintenance work must only be performed with the machine disconnected from the power source and taking all
the safety measures required by current laws and regulations.
ELECTRICAL NATURE INTERVENTIONS
Every electrical adjustment operation must be carried out taking all the safety measures required by current
regulations.
1.5.1. Personal protective equipment
It is mandatory to use specific personal protection devices (PPE) to the current operations made available by
the company (in relation to the risk attached to the performance of certain processes), even when not directly
concerning the use of the machine.
Summary of Contents for 4070 ZX
Page 1: ...MANUAL OF USE AND MAINTANANCE ORIGINAL INSTRUCTIONS WASP4070ZX...
Page 4: ......
Page 14: ...INTRODUCTION WASP S r l 1 14 1...
Page 30: ...INTRODUCTION WASP S r l 4 30 Description of the printer 4...
Page 60: ...INTRODUCTION WASP S r l 60 Ordinary and extraordinary maintanance...
Page 67: ...INTRODUCTION WASP S r l 67 Use of the printer Fig 8 6 Free Zeta System...
Page 82: ...WASP S R L Via Castelletto 104 48024 Massa Lombarda RA Italia www 3dwasp com info 3dwasp com...