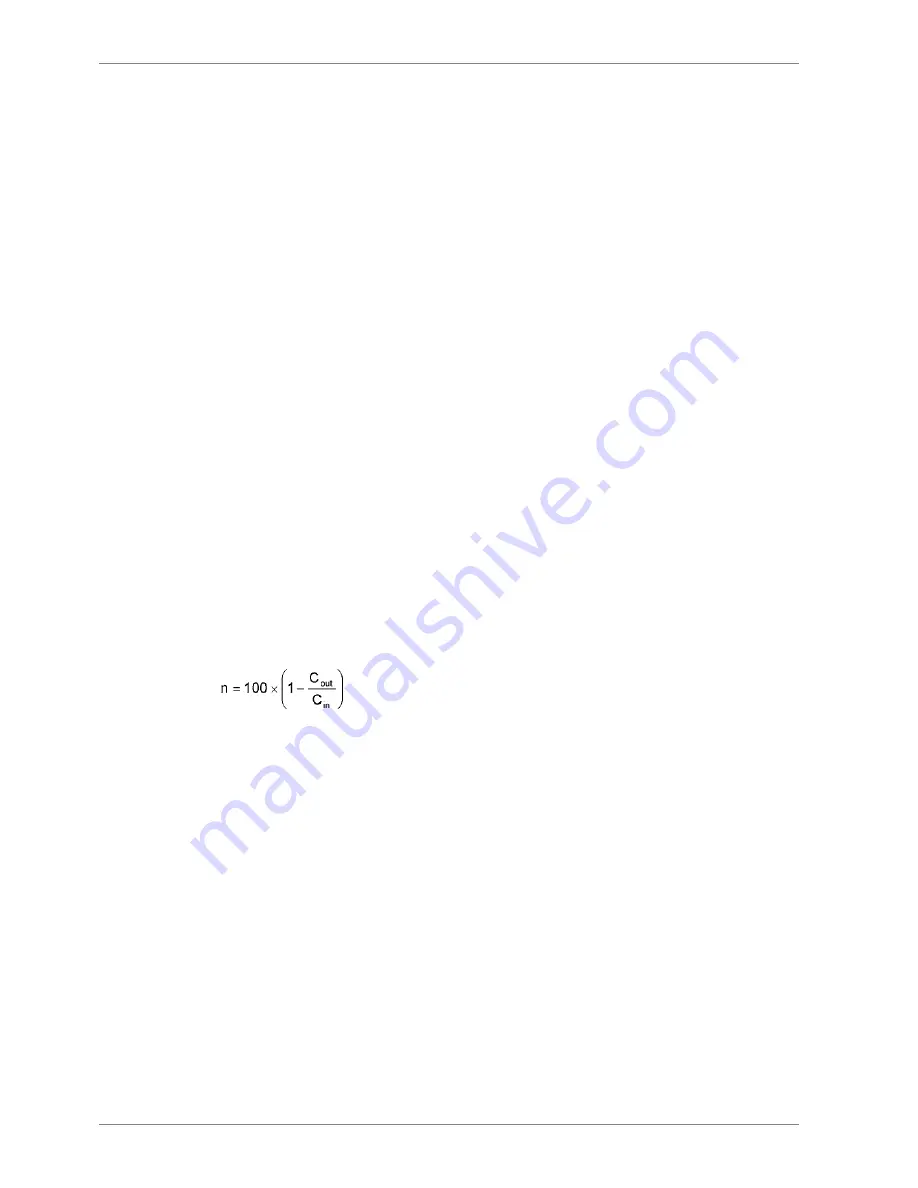
Classification rules require the separator arrangement to be redundant so that required capacity
is maintained with any one unit out of operation.
All recommendations from the separator manufacturer must be closely followed.
Centrifugal disc stack separators are recommended also for installations operating on MDF
only, to remove water and possible contaminants. The capacity of MDF separators should be
sufficient to ensure the fuel supply at maximum fuel consumption. Would a centrifugal separator
be considered too expensive for a MDF installation, then it can be accepted to use coalescing
type filters instead. A coalescing filter is usually installed on the suction side of the circulation
pump in the fuel feed system. The filter must have a low pressure drop to avoid pump cavitation.
Separator mode of operation
The best separation efficiency is achieved when also the stand-by separator is in operation
all the time, and the throughput is reduced according to actual consumption.
Separators with monitoring of cleaned fuel (without gravity disc) operating on a continuous
basis can handle fuels with densities exceeding 991 kg/m3 at 15°C. In this case the main and
stand-by separators should be run in parallel.
When separators with gravity disc are used, then each stand-by separator should be operated
in series with another separator, so that the first separator acts as a purifier and the second
as clarifier. This arrangement can be used for fuels with a density of max. 991 kg/m3 at 15°C.
The separators must be of the same size.
Separation efficiency
The term Certified Flow Rate (CFR) has been introduced to express the performance of
separators according to a common standard. CFR is defined as the flow rate in l/h, 30 minutes
after sludge discharge, at which the separation efficiency of the separator is 85%, when using
defined test oils and test particles. CFR is defined for equivalent fuel oil viscosities of 380 cSt
and 700 cSt at 50°C. More information can be found in the CEN (European Committee for
Standardisation) document CWA 15375:2005 (E).
The separation efficiency is measure of the separator's capability to remove specified test
particles. The separation efficiency is defined as follows:
where:
separation efficiency [%]
n =
number of test particles in cleaned test oil
C
out
=
number of test particles in test oil before separator
C
in
=
6.4.4.2
Separator unit (1N02/1N05)
Separators are usually supplied as pre-assembled units designed by the separator
manufacturer.
Typically separator modules are equipped with:
●
Suction strainer (1F02)
●
Feed pump (1P02)
●
Pre-heater (1E01)
●
Sludge tank (1T05)
●
Separator (1S01/1S02)
6-22
DBAE248994
Wärtsilä 31DF Product Guide
6. Fuel Oil System
Summary of Contents for ?31DF Series
Page 1: ...PRODUCT GUIDE W rtsil 31DF...
Page 4: ...This page intentionally left blank...
Page 8: ...This page intentionally left blank...
Page 14: ...This page intentionally left blank...
Page 74: ...This page intentionally left blank...
Page 84: ...This page intentionally left blank...
Page 134: ...This page intentionally left blank...
Page 150: ...This page intentionally left blank...
Page 154: ...This page intentionally left blank...
Page 164: ...This page intentionally left blank...
Page 182: ...This page intentionally left blank...
Page 188: ...This page intentionally left blank...
Page 196: ...This page intentionally left blank...
Page 204: ...This page intentionally left blank...
Page 210: ...This page intentionally left blank...
Page 212: ...This page intentionally left blank...
Page 215: ......