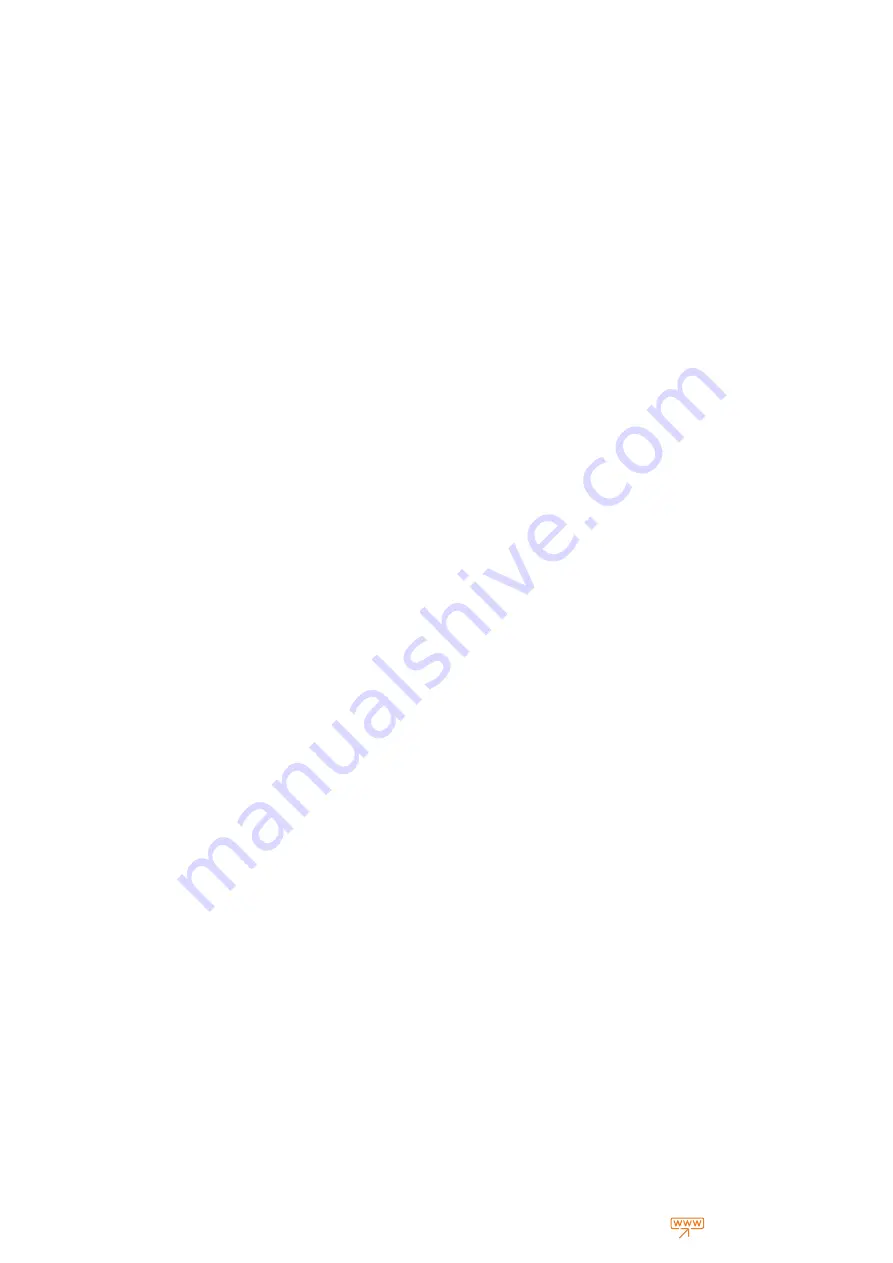
4
warmhaus.com.tr
INTRODUCTION
This Service Manual was prepared by Warmhaus Service Management to provide our dear authorized services convenience and
correct service.
Lifetime of these appliances is 10 years, which was determined by Ministry of Customs and Trade General Directorate of Consumer
Protection and Market Surveillance. Appliances started up by authorized services have two (2) years of warranty against
manufacturing and workmanship faults.
According to the relevant law, producing and vendor companies commit to keep spare parts and provide service for the appliance
in order to make appliances function during this period.
Maintenance activities are determined periodically according to use
frequency and appliance’s distinctive -superior features- and carried out as PAID by authorized services.
Periodic maintenances of the appliance considering the use frequency since the commissioning date provide fuel saving, extend
appliance’s service life, minimize the potential faults, and security and safety systems would be controlled. In cases which you doubt
that appliance isn’t working correct, maintenance should be done in one of the monthly, 3-month, 6-month or 1-year periods.
Don’t clean the outer coating of the appliance with aggressive and/or highly flammable cleaners (for example: gas oil, alcohol etc.)
Appliance’s operations such as control, repair, maintenance, part replacement etc. which is carried out by Authorized Service will
take place under the normal conditions of the appliance and in the place of appliance except force majeures. Before making any
operation on the appliance, disconnect the electricity and gas inlet definitely.
Prior to maintenance of the appliance, check the
functions whether they are working normally or not and -if any- fault condition. Heat values and working noise must be checked
by operating and stopping few times in the hot water and heating positions. Detections before and after maintenance must be
done precisely in the presence of customer.
After the operation, all components must original material to prevent any noise and leakage in the appliance. Auxiliary parts like bolt,
screw, gasket, oring must be installed carefully.