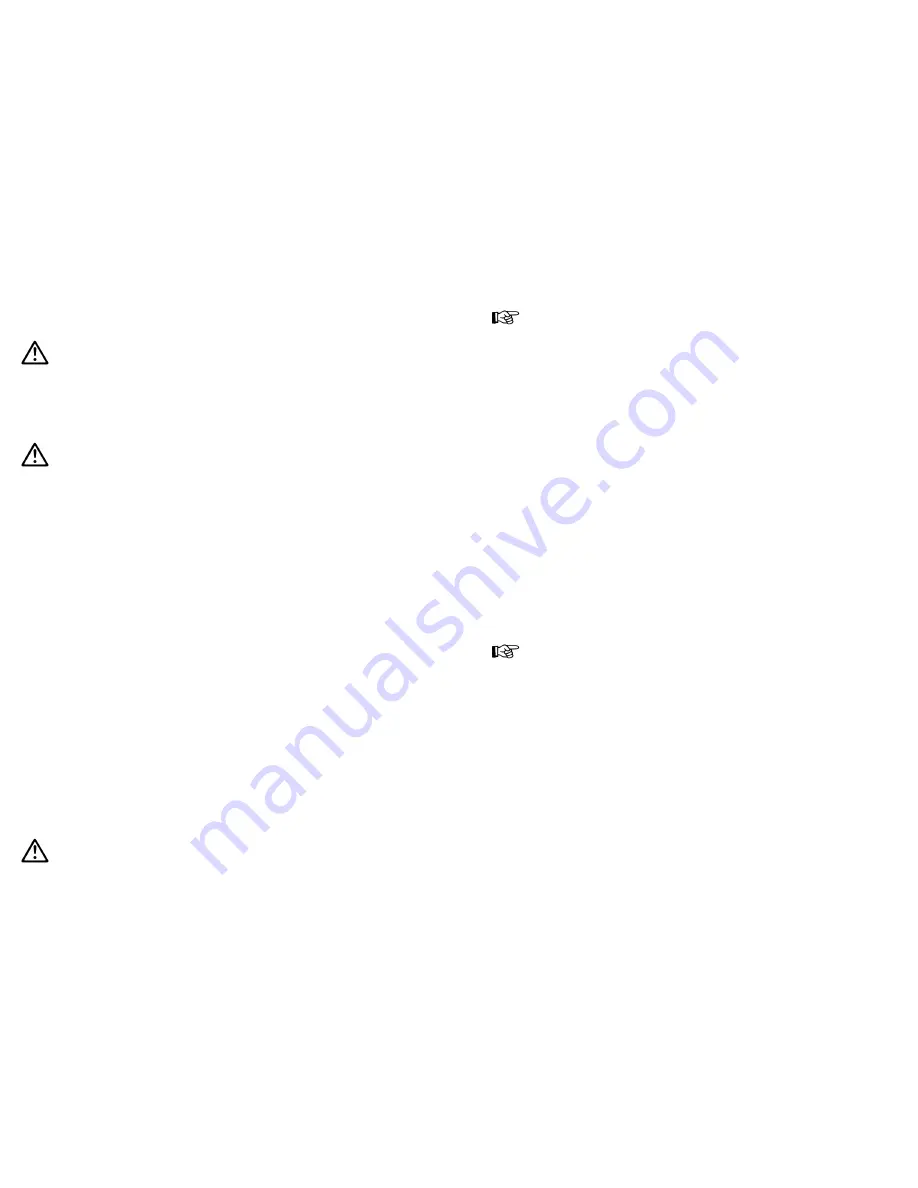
21
20
•
The atomizing air pressure (round jet / flat jet) must be available at the gun
•
The material pressure must be available at the gun.
Caution
The material pressure should not exceed
• 8 bar, since otherwise the operational reliability of the spray gun will be impaired.
The control air pressure should be set at
• minimum of 4,5 bar,
in order to operate the gun.
The operation of the spray gun can be started/stopped by way of the 3/2-way control
valve (see the operating instructions of the plant systems manufacturer).
Warning
It is important to remember to relieve the spray gun of all pressures when work is
terminated. Lines left under pressure may burst and the released material may
injure any persons in the vicinity.
Spray Pattern Test
Spray pattern tests should be performed whenever:
•
the spray gun is taken into operation for the first time;
•
the spraying medium is changed;
•
the spray gun was taken apart for maintenance or repair works.
The spray pattern is best tested using a workpiece sample, a sheet of metal,
cardboard or paper.
Spray Pattern Adjustment
Material flow rate
In order to establish the material flow rate choose a suitable nozzle size. Further-
more it is dependent on the upcoming material pressure.
Regulate the material pressure
Adjust the material pressure at the pump or the material pressure tank - make sure
to follow relevant instructions and safety warnings of the manufacturer!
Regulate the atomizing air pressure
The atomizing air pressure is continuously variable adjusted at the arranged air
pressure-reducer in the plant system. Please comply with the operating instructions
and safety warnings issued by the manufacturer.
Regulate the control air pressure
The control air pressure is to be adjusted at the air pressure reducing valve of the
compressor system. Please comply with the operating instructions and safety
warnings issued by the manufacturer.
6
Retooling and Repairs
Warning
Control and atomizing air as well as material inputs must be shut off prior to retooling
- risk of injury.
Note
Please refer to the exploded view at the beginning of these operating instructions to
perform the steps detailed below.
Changing of the air cap
1. Unscrew the air cap nut (item 3) and remove the air cap (item1) from the gun
body (item 5).
Changing the material nozzle
1. Remove the air cap (item 1).
2. Remove the material nozzle (item 2) from the gun body using the size 7 wrench.
Changing the material needle
1. Unscrew the three countersunk screws (item 15) from the front gun section
(item 5).
2. Disassemble the piston housing (item 14).
3. Disassemble the piston spring (item 12).
4. Pull out the piston (item 8) together with the material needle (item 7).
5. Unscrew the needle chuck (item 10) and separate the piston from the material
needle (item 7).
Install the new material needle* in reverse order.
Changing the Springs and Seals
If the following parts have to replace, dismantle the spray gun in accordance with the
work steps write above:
•
Piston Spring
•
O-ring of the piston*
Note
Parts marked * have to be lubricated with a non-acidic, non-resinogenic grease prior
to installation.
7
Cleaning and Maintenance
•
Make sure that the spray gun is in unpressurised condition, i.e. all air and
material inputs must be shut off - if not, imminent Risk of Injury.
•
Open fires, naked lights and smoking is prohibited in the working area. There is
an increasing risk of fire and explosion, when spraying readily flammable media
(such as cleaning solutions).
•
Observe all processing specifactions and safety warnings issued by the
manufacturer of cleaning media. Especially aggressive and corrosive media
represents risks and hazard to personal health.
Clean the spray gun
•
prior to each change of the spraying medium
•
at least once a week
•
as often as may be required by the spraying medium handled and the resulted
degree of fouling.