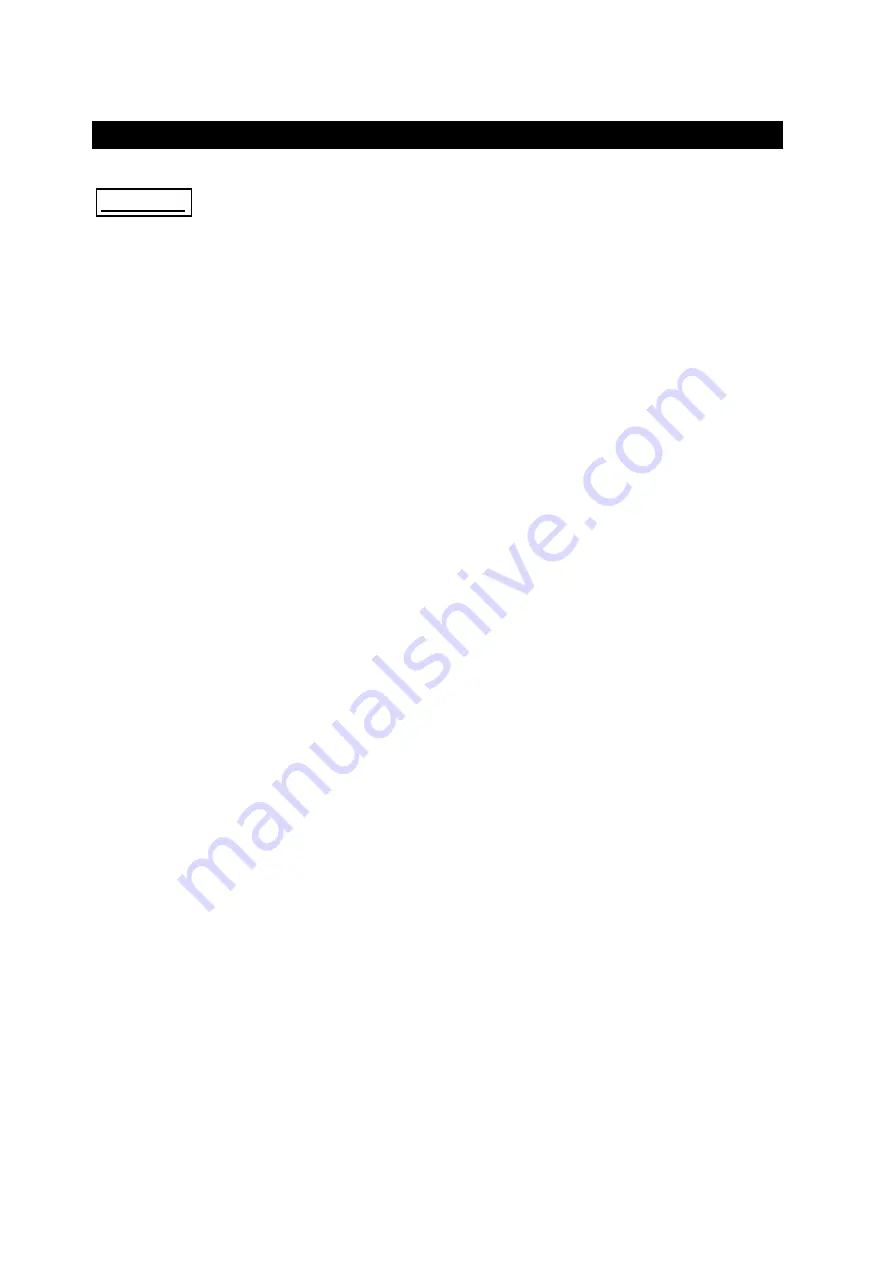
22
MAINTENANCE
WARNING!
MAKE CERTAIN THAT THE MACHINE IS DISCONNECTED FROM THE
POWER SOURCE BEFORE PERFORMING ANY MAINTENANCE PROCEDURES
DAILY AFTER USE
Clean shavings away from the lathe bed and tool rest, etc.
MONTHLY
Check the belt tension and adjust if necessary. See pages 17 and 18 for instructions.
Check for any build-up of wood shavings on the motor and pulleys and clean if necessary
Using compressed air, lightly blow out the motor vents.
If the lathe will not be used for an extended period of time, place a light coat of wax over the bed
and place a dust cloth over the lathe.
Summary of Contents for 60170ML-WHD
Page 5: ...5 FEATURE IDENTIFICATION cont WIRED REMOTE CONTROL WITH MAGNETIC BACK...
Page 24: ...24 PARTS...
Page 25: ...25 PARTS cont...
Page 31: ...31 WIRING DIAGRAM...
Page 32: ...32...