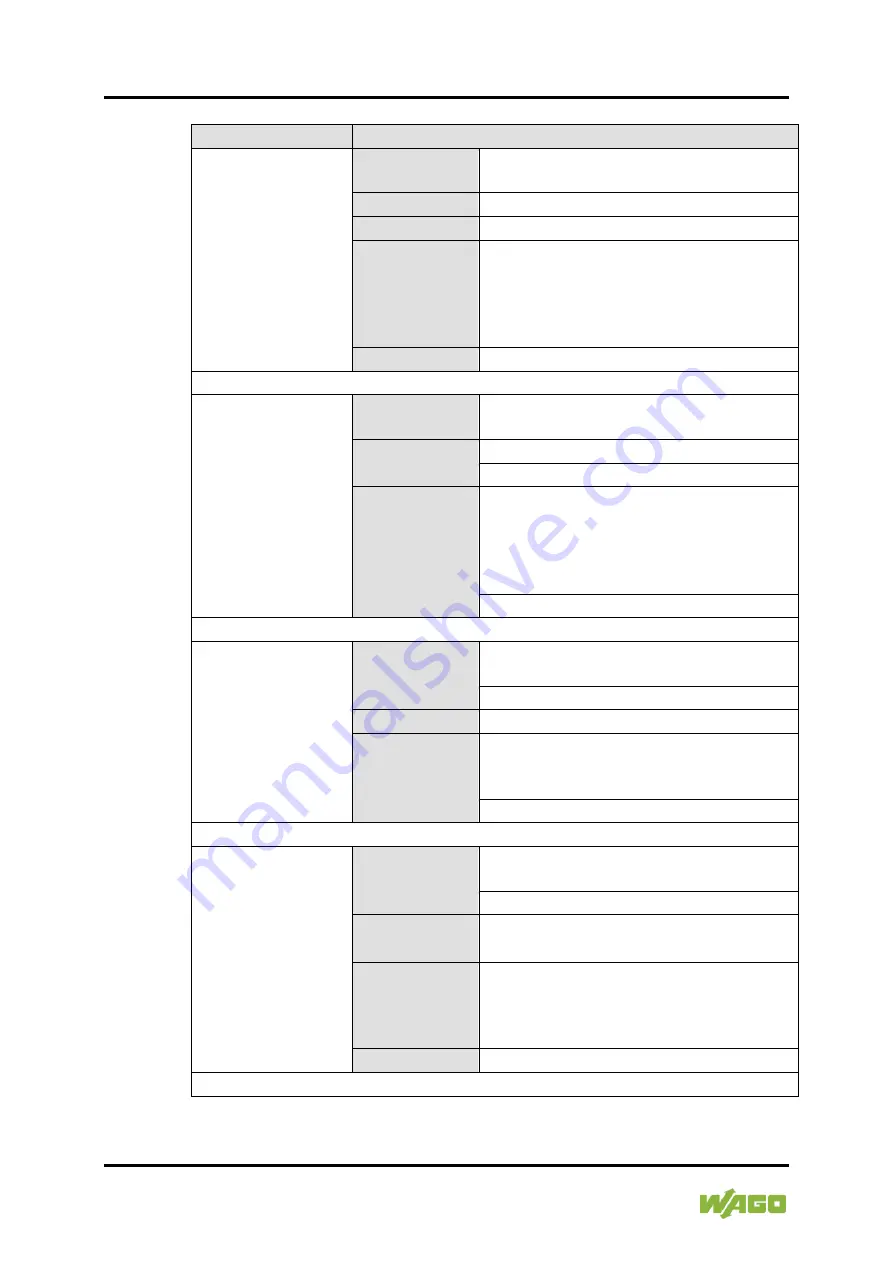
130 Diagnostics
WAGO-I/O-SYSTEM 750
753-668/000-004 4FAI 0/4-20 mA Diff PROFIsafe
Manual
Version 1.0.0, valid from HW/SW Version 01/01
Table 49: Diagnostic Messages
Alarm
Description
Underrange 1
Diagnostic
type
Channel diagnostics
Coding
0x0292
LED indicator
Description/
Remedy
The process value of the analog input is in
underrange 1 according to the set data
format.
Check the sensor wiring and the sensor
itself if necessary.
Classification
Warning
Underrange 2
Diagnostic
type
Channel diagnostics
Coding
0x0293
LED indicator
Description/
Remedy
The process value of the analog input is in
underrange 2 according to the set data
format.
Check the sensor wiring and the sensor
itself if necessary.
Classification
Warning
Undervoltage field
supply
Diagnostic
type
Module diagnostics
Coding
0x0202
LED indicator
Group error red
Description/
Remedy
The 24 V field supply of the F I/O module is
below the specified tolerance. Correct the
power supply responsible.
Classification
Error
Wire break
Diagnostic
type
Channel diagnostics
Coding
0x0290
LED indicator
Group error red
Channel status red
Description/
Remedy
The process value of the analog input is in
the wire break range according to the set
data format. Check the sensor wiring and
the sensor itself if necessary.
Classification
Error