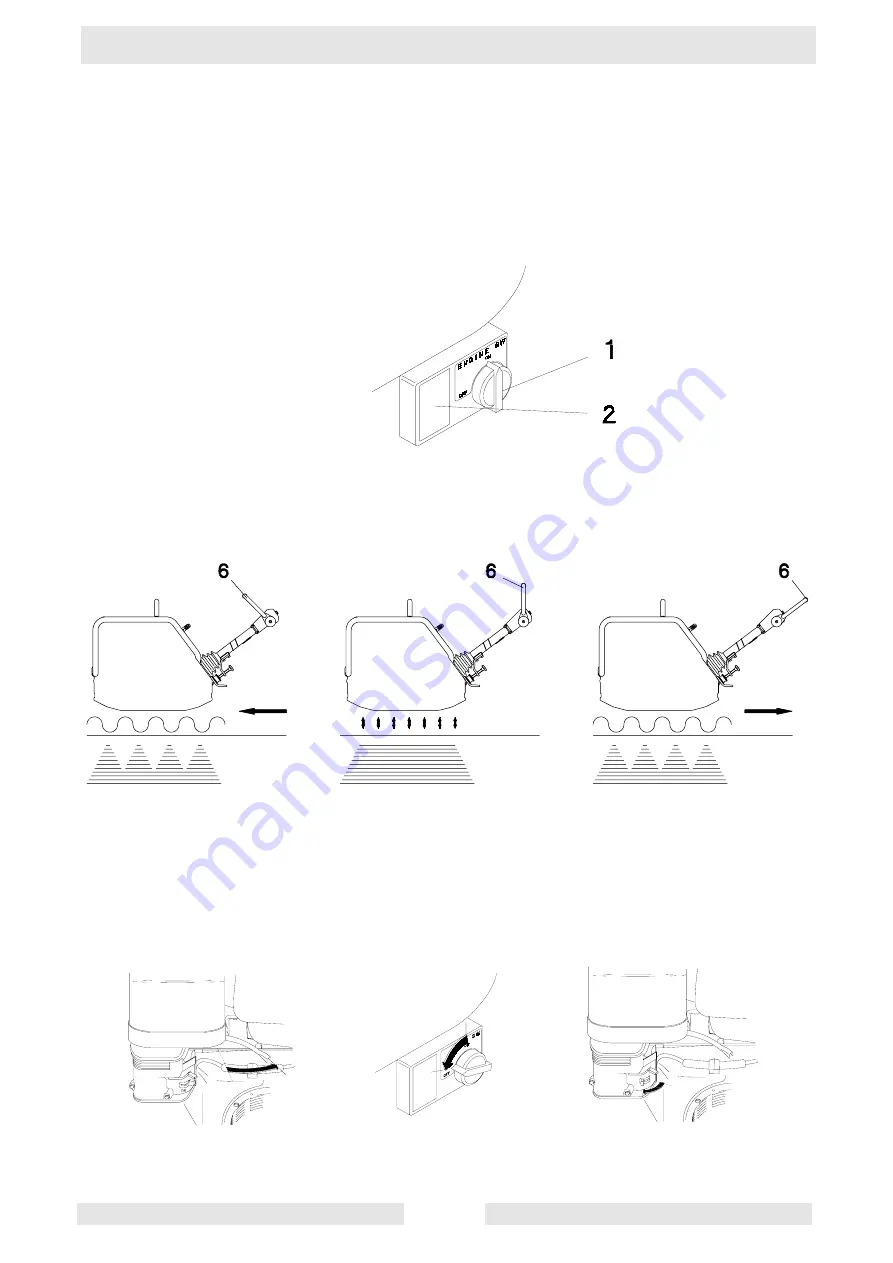
T00805GB
14
OPERATION
Handling
As the engine warms up, gradually move the choke lever to the OPEN position.
Position the throttle lever for the desired engine speed.
Oil alert system
The oil alert system is designed to prevent engine damage caused by an insufficient amount of oil in the crank-
case. Before the oil level in the crankcase drops below a safe limit, the oil alert system will automatically shut
down the engine (the engine switch will remain in the ON position).
1
Engine switch
2
Note: If engine does not start
check oil level
Forward and reverse motion
The engine speed can be infinitely varied with the throttle control lever (5).
The direction of travel is determined with the operating control handle (6).
Depending on the position of the control handle (6), the vibration plate compacts in forward direction, on the
spot or in reverse direction.
Forwards
On the spot
Reverse
Stopping the engine
To stop the engine in an emergency, turn the engine switch to the OFF position. Under normal conditions, use
the following procedure:
a) Move the throttle lever fully to the right.
b) Turn the engine switch to the OFF position.
c) Turn the fuel valve to the OFF position.
a)
b)
c)
Summary of Contents for BPU 3545A
Page 1: ...www wackergroup com Operator s Manual VIBRATORY PLATE BPU 3545A 0200301en 12 2001 0008783 100...
Page 4: ...2...
Page 15: ...T00805GB 13...
Page 26: ...24...
Page 27: ...File certificate carefully DIN EN ISO 9001 Certificate...
Page 28: ......