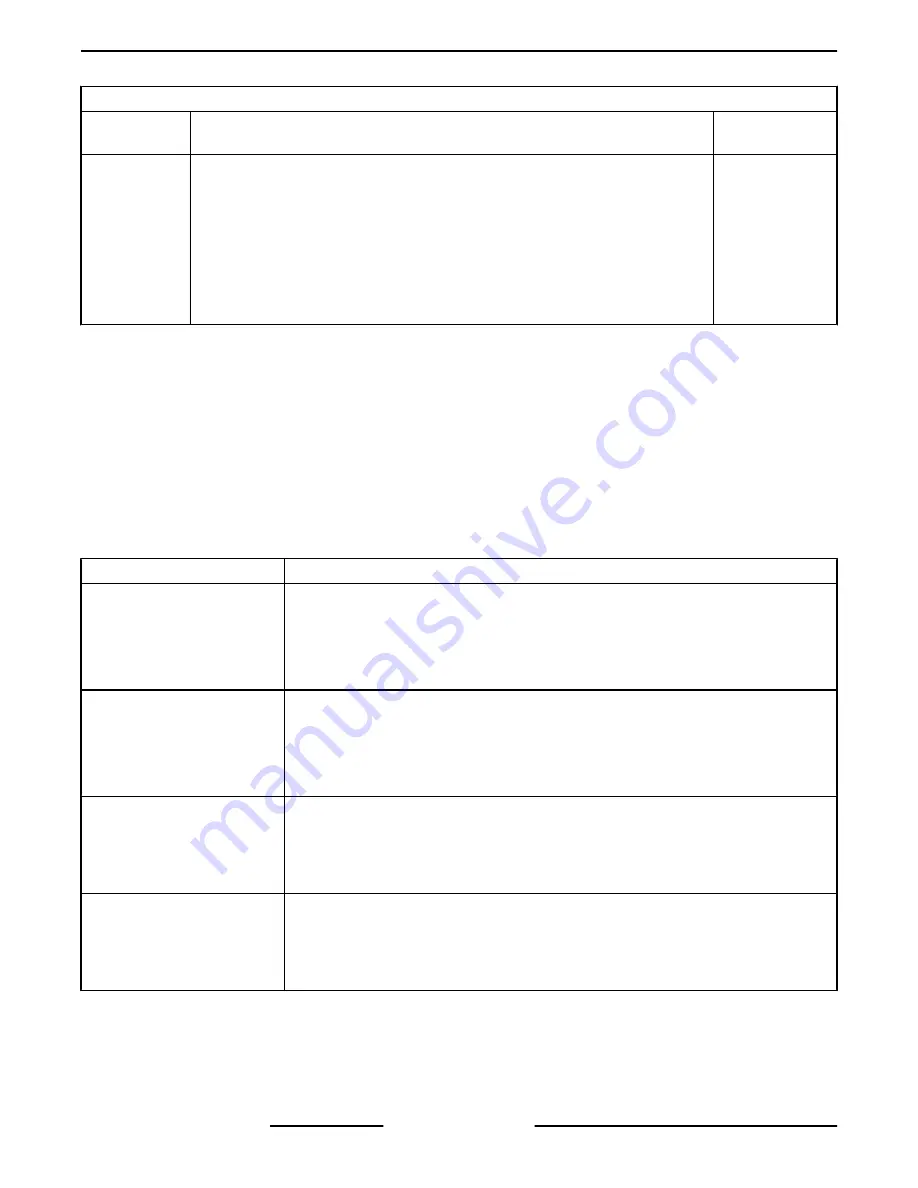
Control Programming
PROGRAM
ITEM
KEY SEQUENCE
DISPLAY
NOTES
1
Default value shown in bold type.
2
Temperature will change in one degree increments, accelerating if the
button is held.
3
Time will change in one second increments, accelerating if the button
is held.
4
Gas* and Gas Star are the same value. The Solid State Display cannot
show an asterick(*).
Display Test
1.
Cycle power switch. When FRYERS is
displayed, press PROGRAM key.
A.
Display shows DSP TEST.
B.
Press PROGRAM key again to light all the
display segments in the first character.
C.
Continue pressing PROGRAM key until the
display segments for all eight characters are
tested.
2.
To exit test, press and hold the PROGRAM key
for one second.
Alarm Messages
Alarms take precedence over any other controller
mode or function (except drain valve function).
ALARMS
DESCRIPTION
OPEN PROBE
If an open probe is detected, the heat demand (heat on) and basket lift outputs are
disabled. Any cooking in progress is cancelled and all operator buttons are disabled.
the display alternates OPEN PROBE and the electronic alarm will sound
continuously.
NOTE:
A temperature of 460°F is an open probe equivalent.
SHORTED PROBE
If a shorted probe is detected, the heat demand (heat on) and basket lift outputs are
disabled. Any cooking in progress is cancelled and all operator buttons are disabled.
The display alternates SHORTED PROBE and the electronic alarm will sound
continuously.
NOTE:
A temperature of 460°F or greater is a shorted probe equivalent.
HI TEMP
If the temperature is greater than or equal to 415°F, the heat demand (heat on) and
basket lift outputs are disabled. Any cooking in progress is cancelled and all operator
buttons are disabled. The display alternates HIGH TEMP and the electronic alarm
will sound continuously. Normal fryer operation resumes when the temperature
drops below the high temperature alarm level.
IGNITION STATUS (gas
models only)
If the ignition status input to the control is not active (24VAC = active), the display
shows NO PILOT. If the input remains inactive for greater than 90 seconds, the
display will alternate IGNITION LOCKOUT, the electronic alarm will sound
continuously, and the controller will be disabled (all outputs including heat demand
off) until power is cycled.
VK and TR GAS FRYERS W/Wo KleenScreen PLUS - SERVICE PROCEDURES AND ADJUSTMENTS
F45474 (0413)
Page 30 of 55