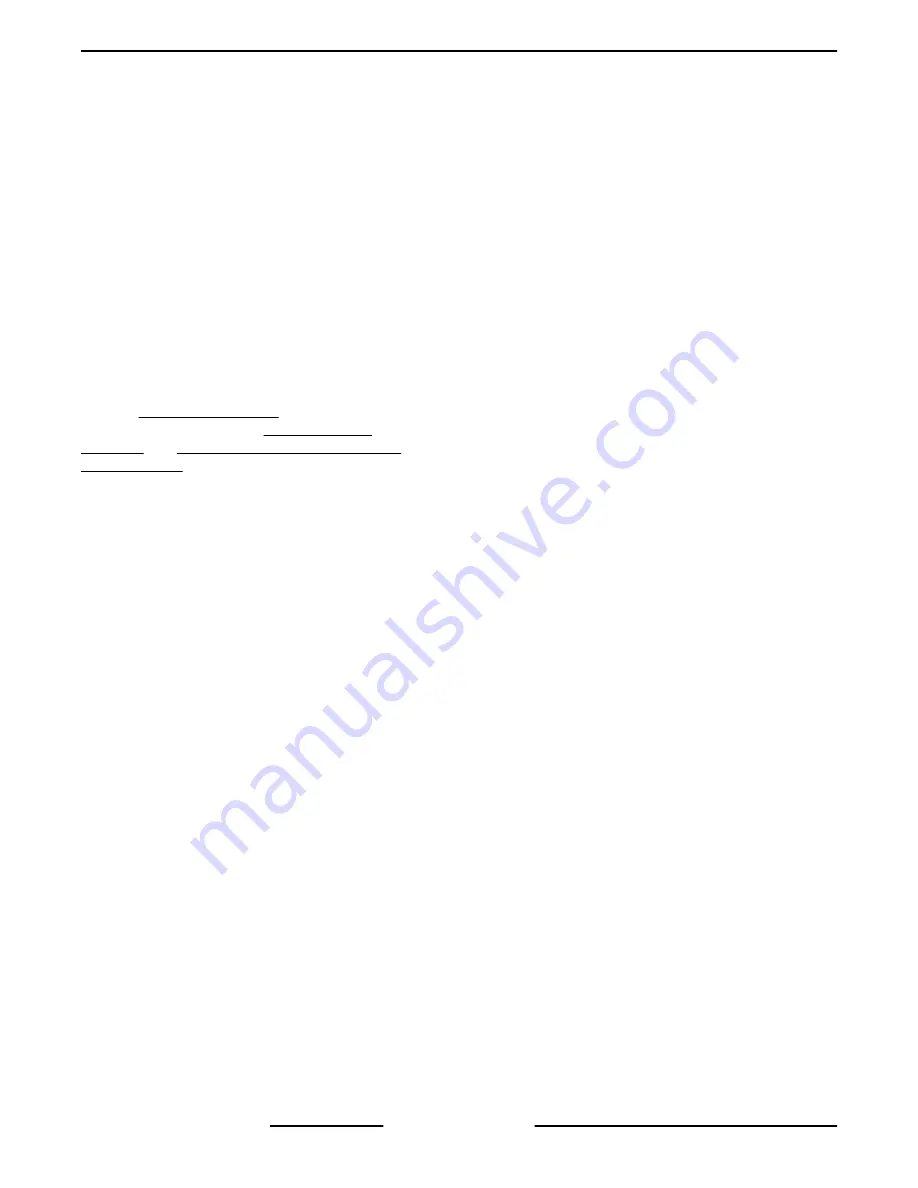
12. If shortening is allowed to cool over a long period
of time, burner will operate on low heat to
maintain shortening temperature near operating
temperature.
NOTE:
When the fryer shortening is cooling, the
controller observes how fast or slow the temperature
drops. If the temperature drops slowly the controller
will operate the burner with the blower motor in low
speed allowing the burner to operate at a lower BTU
output to save our customers money by using less
gas. The fryer will still reach set temperature, just at a
slower pace. If the temperature drops rapidly, the
controller will operate the burner blower motor in low
speed until the flame is rectified, then it will change to
the high speed for the rest of the call for heat
Drawer Filter System
Refer to SCHEMATIC AI3496 for Drawer Filter
System operation. Refer to VK OPERATOR
MANUAL and DRAWER FILTRATION SYSTEM
SUPPLEMENT for specific instructions on filtering.
NOTE:
The discard valve handle is connected to a
mechanical valve and magnetic reed switch assembly
to route the flow of shortening in the filtering system
and supply power to the pump motor.
1.
Conditions.
A.
Fryer connected to correct supply voltage
and is properly grounded .
B.
Power switch to fryer section to filter turned
on.
C.
The cooking control should be setup
properly and ready to use.
D.
Cooking control temperature setting
between 300°F (minimum) and 350°F
(maximum).
NOTE:
Shortening should not be filtered outside of
this temperature range. At lower temperatures the
shortening is thicker which may increase filtering time
and place a greater load on the pump. At higher
shortening temperatures, oil seal life is decreased.
E.
Filter drawer assembly installed properly.
F.
Drain valve handle (white) retracted.
1)
Drain valve interlock switch N.O.
contacts open. Mechanical drain valve
closed.
2.
Allow shortening to cycle between 300°F and
350°F for approximately 10 minutes.
NOTE:
If using solid shortening, once it has melted,
stir the shortening to eliminate any sold shortening in
cold zone of the fry tank.
3.
Open drain valve to fryer section in need of
filtering and drain shortening into filter tank.
A.
Display indicates draining.
B.
Drain valve interlock switch contacts open
and position of drain valve is indicated to
cooking control.
NOTE:
If using solid shortening, allow hot shortening
to stand in filter tank for approximately 6 minutes prior
to filtering.
4.
Press filter key on the control panel and hold for
3 seconds. The filter output signal (24VAC) at pin
E1-9 is turned on and the interface board K3 relay
coil is energized at pins 11 & 4.
A.
K3 N.O. contacts close and 24VAC is output
from the interface board at pin 12.
B.
R1 pump motor relay coil (24VAC) is
energized and both sets of N.O. contacts
close.
NOTE:
Jumper wire number 24 connects one set of
R1 N.O. contacts to R2 COM.
1)
Fill solenoid valve is energized
(120VAC) thru R2 fill relay N.C.
contacts and valve opens.
2)
Pump motor is energized (120VAC)
and pump circulates shortening
through filtering system.
5.
When filtering is completed, close the drain valve
and allow the fry tank to refill.
A.
Display indicates fill tank.
B.
Drain valve interlock contacts close and the
position of the drain valve is indicated to the
cooking control.
6.
When all filtered shortening is returned to the fry
tank, press filter key on the control panel.
A.
Power is removed from fill solenoid valve
and pump motor.
B.
Display indicates tank full hit temp. If
shortening is at proper level in fry tank,
press and hold temp key until shortening
temperature is displayed. Filtering cycle is
complete and fryer resumes normal
operation.
NOTE:
If using solid shortening, when all filtered
shortening is returned to fry tank and pump motor is
off, open filter drawer approximately one inch. Allow
remaining shortening in line to drain into filter tank to
prevent possible clogging after shortening cools and
solidifies. Close filter drawer when complete.
VK and TR GAS FRYERS W/Wo KleenScreen PLUS - ELECTRICAL OPERATION
F45474 (0413)
Page 44 of 55