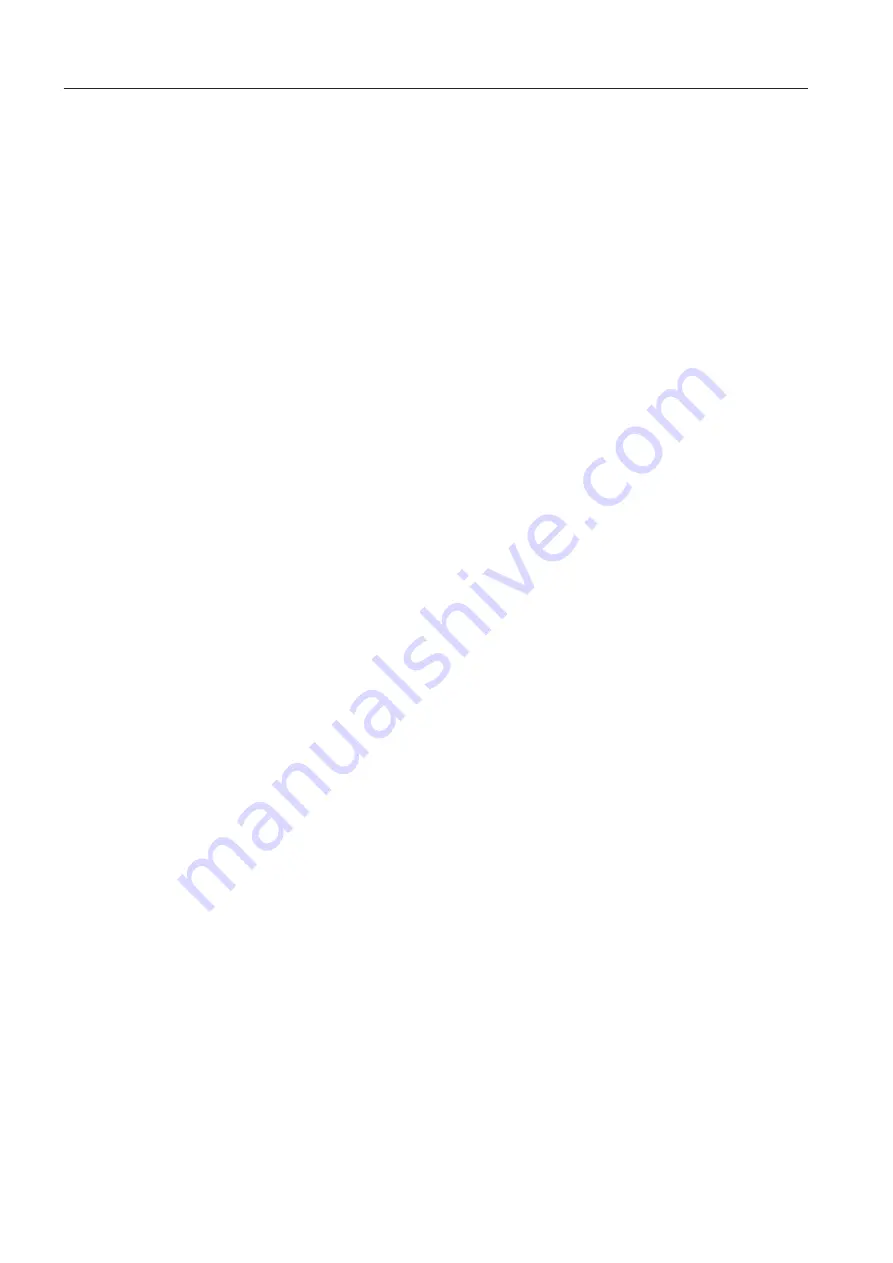
D
D
isengaging the boom suspension system
To disengage the boom suspension system press the lower end
of the BSS switch down. The BSS symbol is not shown in the
display if the system is switched off.
19
9
8
8
Op
p
e
e
r
r
a
a
t
t
i
i
n
n
g
g
te
e
c
c
hn
n
i
i
q
q
u
u
e
e
s
s
Boo
o
m
m
Su
u
s
s
pe
e
n
n
s
s
io
o
n
n
Sy
y
ste
e
m
m
(B
B
S
S
S
S
)
)
Summary of Contents for 322001
Page 7: ...5 5 ...
Page 146: ...Right mirrors 1 14 44 4 Op pe er ra at ti in ng g in ns str ru uc cti io on ns s ...
Page 172: ...1 170 Operating instructions Exhaust aftertreatment system ...
Page 357: ...S Specifications Dimensions 355 ...
Page 410: ......
Page 413: ......
Page 414: ...4 412 Alphabetical index Ref No 20052711 C Volvo Eskilstuna English ...