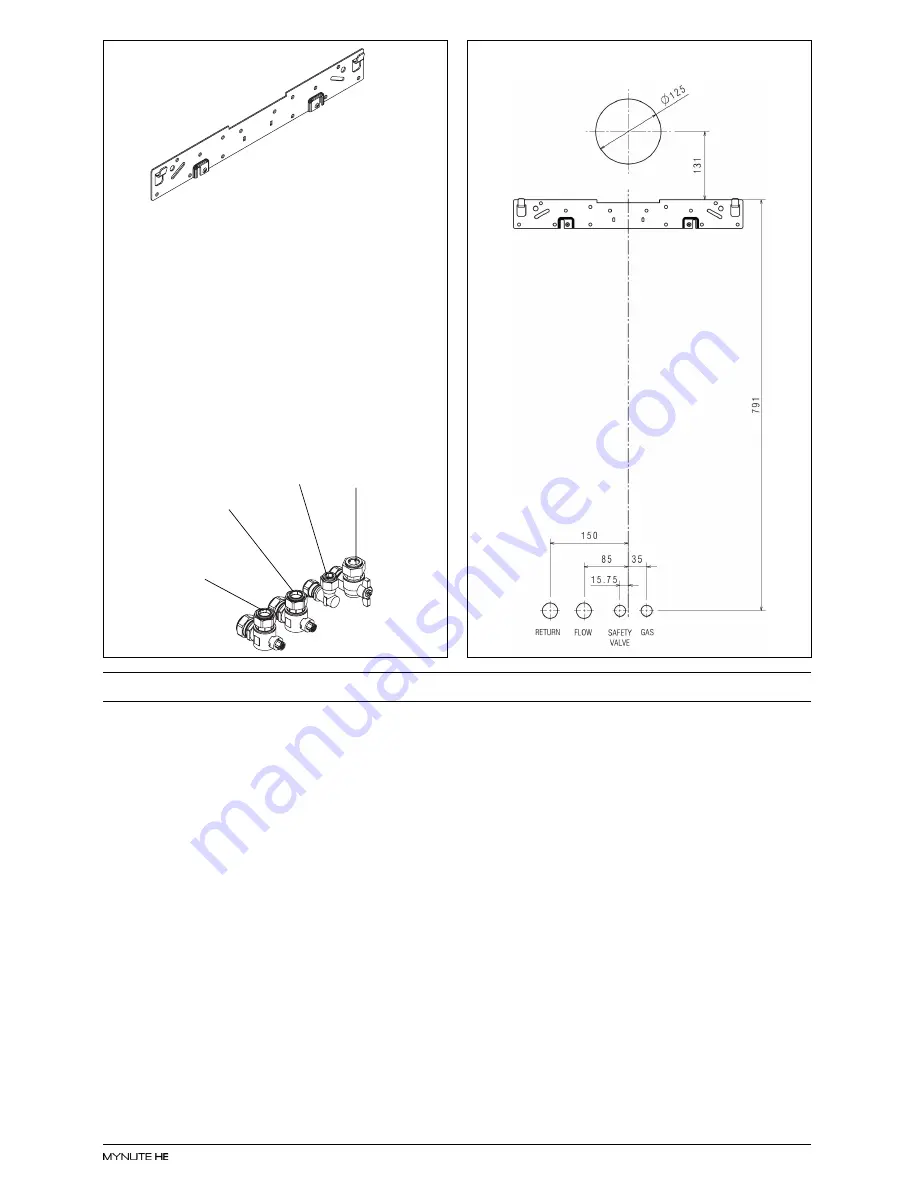
7
Fig. 6A
Gas
cock
C/H flow
valve
C/H return
valve
Safety
valve outlet
Fig. 6B
SECTION 3A
GENERAL REQUIREMENTS (EIRE)
This appliance must be installed by a competent
person in accordance with and defined by, the
Standard Specification (Domestic Gas Installa-
tions) Declaration (I.S. 813).
3A.1
RELATED DOCUMENTS
The installation of this boiler must be in accord-
ance with the relevant requirements of the local
building regulations, the current ETCI National
Rules for Electrical Installations, and the bylaws
of the local water undertaking.
It should be in accordance also with any relevant
requirements of the local and/or district authority.
3A.2
LOCATION OF APPLIANCE
The appliance may be installed in any room or
internal space, although particular attention is
drawn to the requirements of the current ETCI Na-
tional Rules for Electrical Installations, and I.S.
813, Annex K.
When an appliance is installed in a room or internal
space containing a bath or shower, the appliance
or any control pertaining to it must not be within
reach of a person using the bath or shower.
The location chosen for the appliance must permit
the provision of a safe and satisfactory flue and
termination. The location must also permit an
adequate air supply for combustion purposes and
an adequate space for servicing and air circulation
around the appliance. Where the installation of the
appliance will be in an unusual location special
procedures may be necessary, refer to I.S. 813 for
detailed guidance on this aspect. A compartment
used to enclose the appliance must be designed
and constructed specifically for this purpose. An
existing compartment/cupboard may be utilised
provided that it is modified to suit. This appliance
is not suitable for external installation.
3A.3
GAS SUPPLY
The gas meter - as supplied by the gas supplier -
must be checked to ensure that it is of adequate
size to deal with the maximum rated input of all the
appliances that it serves. Installation pipes must
be fitted in accordance with I.S. 813.
Pipe work from the meter to the appliance must
be of adequate size. Pipes of a smaller size than
the appliance gas inlet connection must not be
used. The installation must be tested for sound-
ness in accordance with I.S. 813.
If the gas supply serves more than one appliance,
it must be ensured that an adequate supply is
maintained to each appliance when they are in
use at the same time.