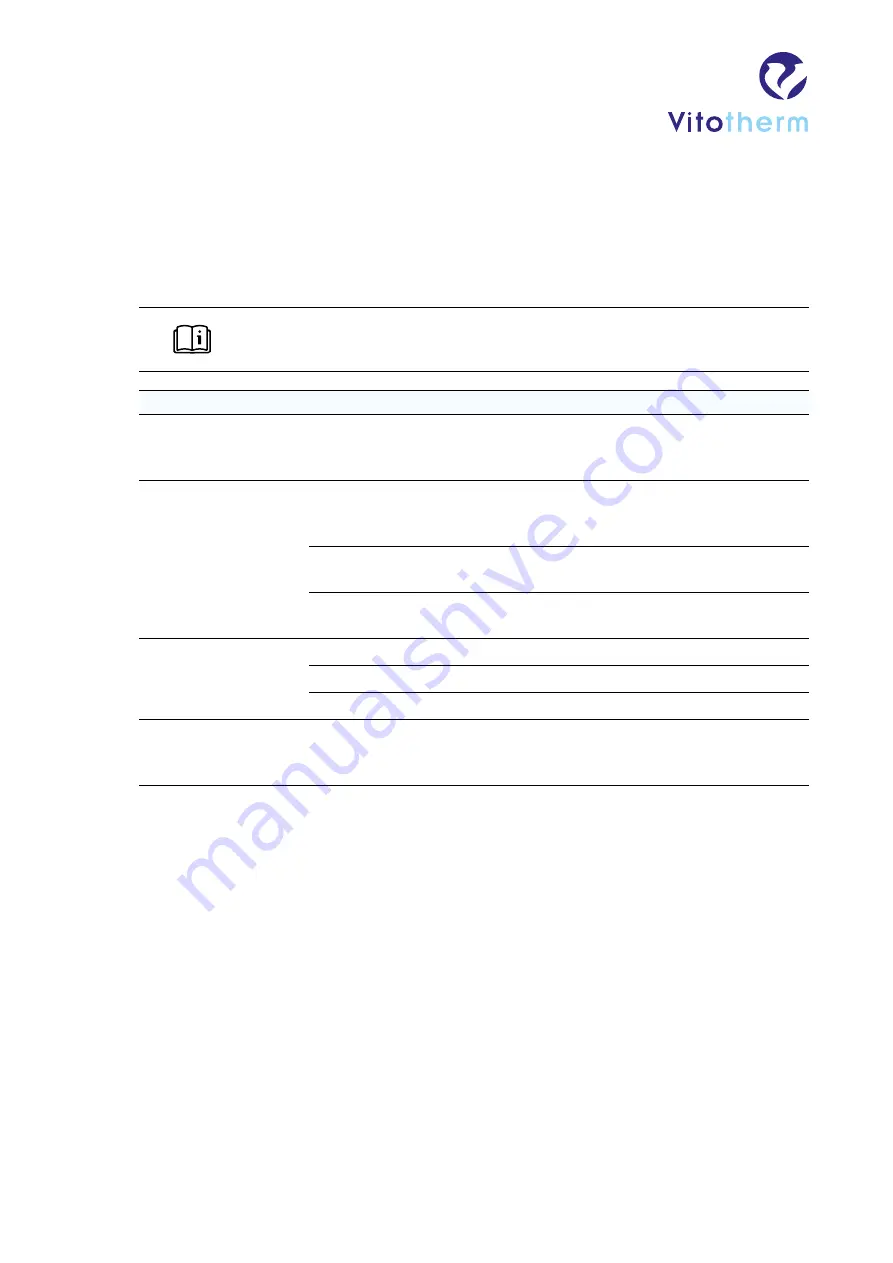
27
CO2 set
| Instruction
manual
rev-03_May 2022
7
.
Troubleshooting
System failures are displayed on the interface of the control panel or frequency drive. The table below can be used to identify
and solve the failure.
For more detailed information about these system failures, please refer to the OEM manual of the
Lamtec operating system.
Description
Cause(s)
Solution(s)
Failure indication LED:
Max. thermostat
Flue gas after CO
2
temperature
is too high.
1
)
Perform a system reset (see §
6.3
.
).
2
)
Check the modulating temperature control. Adjust if
necessary.
Failure indication LED:
Valve failure (ES6)
Valve servomotor has stopped
working: jammed valve shaft
1
)
Dismount, clean and remount the 2-way valve
servomotor.
2
)
Replace the servomotor if necessary.
Valve servomotor has stopped
working: jammed ball joint
1
)
Close the valve by hand.
2
)
Perform a system reset (see §
Limit switch of the 2-way valve
servomotor is set incorrectly.
Adjust the settings of the limit switch. Refer to the OEM
manual for instructions.
The fan motor overrides the
maximum current.
Fan or air inlet is obstructed.
Check the fan and air inlet and remove any obstructions.
The motor runs on 2 phases.
Check the electrical wiring and fuses.
The motor is defective.
Repair or replace the motor.
Minimum CO
2
pressure failure
(LD3)
Insufficient air is being
transported through the
dosing unit.
Check the fan housing outlet for obstructions.
Check if the sleeve connections are airtight.