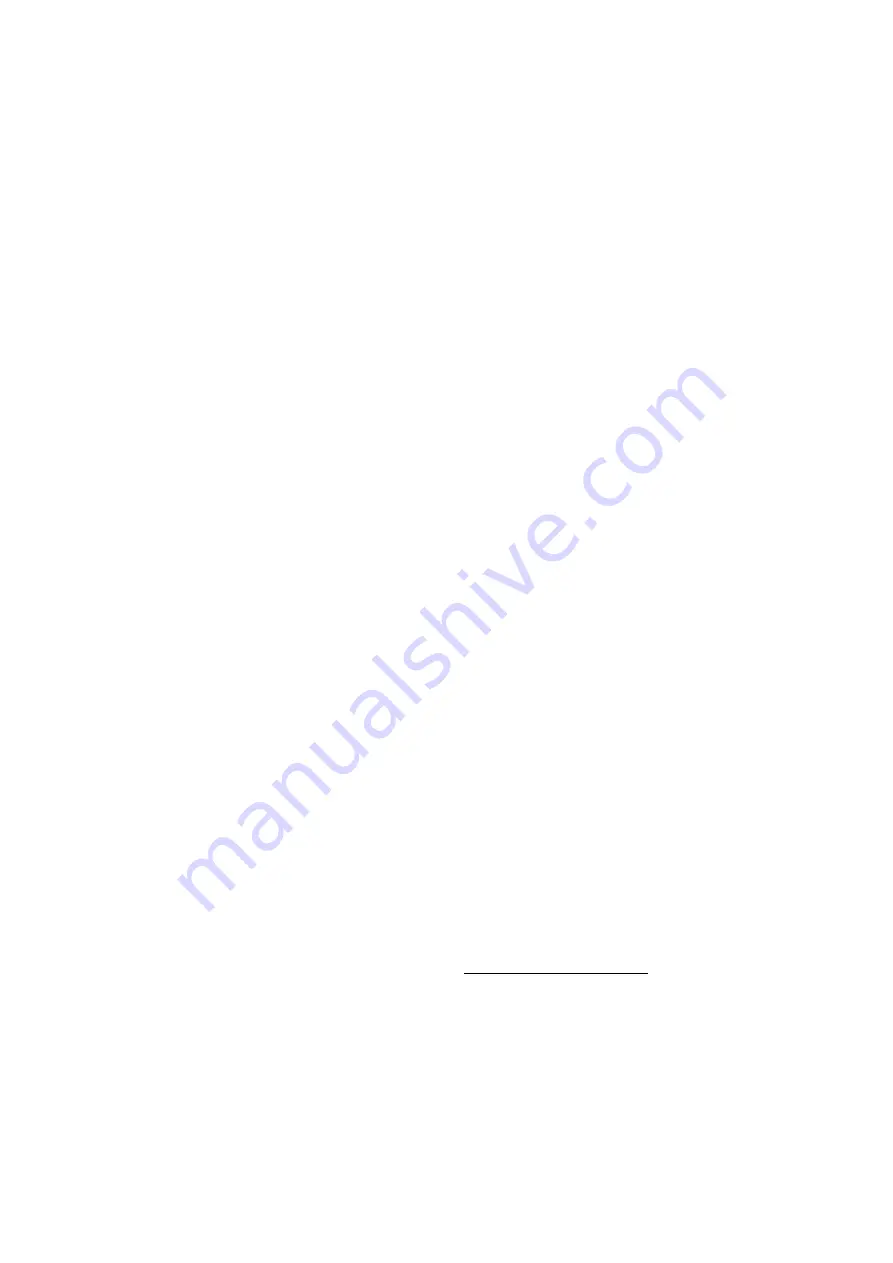
G4 Multi Channel Force Instrument
5-3
Calibrating using datasheet
When calibrating with data given in the transducer data sheet the ‘Table calibration’
method should be used. Note that there are two different ways that the transducer
characteristics may be described in a data sheet. Choose the appropriate method
below.
There are parameters for each input that are used with the current configuration for the
Function Block being calibrated. Function Blocks can be 1 channel (Input A), 2 channel
(Input A - B) or 4 channel (Input A - D) type. Note that only input channel A parameters
are shown in the text below.
The transducer characteristics is given as two (or more) load / transducer output value
pairs:
X:A Value Cal. P1:
Enter first calibration point load value, expressed in the measurement unit, (usually zero)
in this parameter.
X:A Transd. Signal P1:
Enter first calibration point transducer output value, in mV/V, in this parameter.
X:A Value Cal. P2:
Enter last calibration point load value, expressed in the measurement unit, (usually
nominal load) in this parameter.
X:A Transd. Signal P2:
Enter last calibration point transducer output value, in mV/V, in this parameter.
The change of transducer output in mV/V is given for a load change, usually
corresponding to the transducer nominal load:
X:A Value Cal. P1:
Enter zero in this parameter.
X:A Transd. Signal P1:
Enter zero in this parameter.
X:A Value Cal. P2:
Enter the given load value, expressed in the measurement unit, in this parameter. This
value is usually nominal load.
X:A Transd. Signal P2:
Enter the datasheet mV/V value, corresponding to the given load change, in this
parameter. This value is often called Rated Output. See the example of ‘Data and
Calibration Sheet’ shown under section General in this chapter.
After entering the four parameters above the gradient of the force input is defined. Next
step is to zero the input:
X:A Set Zero
Set zero is useful only when the installation is finished. By the digit keys this value can
be set to zero, for an unloaded input, or to the force of the known load for a loaded
input. Note that unloaded means when the display should show zero.
X:A Zero Offset
This parameter is used for entry of the recorded zero offset value from a previous
calibration. If a zeroing has been performed with parameter ‘Set zero’ above, the value
of parameter ‘Zero offset’ need not be changed.
Repeat the calibration for all inputs used in the Function Block.
Summary of Contents for G4-DT
Page 2: ......
Page 18: ...Technical Manual 1 14 ...
Page 36: ...Technical Manual 2 18 ...
Page 45: ...G4 Multi Channel Force Instrument 4 5 ...
Page 76: ...Technical Manual 4 36 ...
Page 82: ...Technical Manual 5 6 ...
Page 92: ...Technical Manual 6 10 ...
Page 138: ...Technical Manual 7 46 ...
Page 158: ...Technical Manual 8 20 ...
Page 164: ...Technical Manual 9 6 ...
Page 170: ......
Page 171: ...G4 Multi Channel Force Instrument Appendix 1 ...
Page 172: ...Technical Manual ...
Page 173: ......