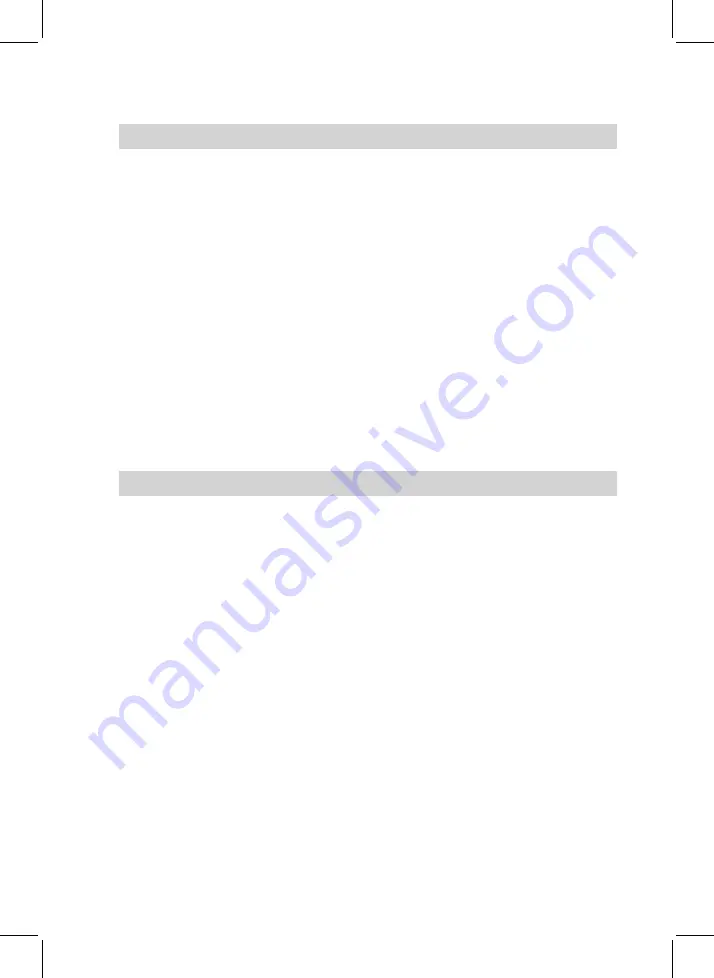
Duct mounted devices, type D304H, D305H and D307H
When ordering spare parts:
Quote the part and serial no. (see
type plate) and the item no. of the
required part (as per this parts list).
Obtain standard parts from your local
supplier.
Parts
001 Air filter
006 Impeller
007 Fan motor
009 Receiver
013 Fan motor capacitor
018 Control PCB
020 Room temperature sensor (only
type D304H)
021 Temperature sensor (only type
D304H)
022 Temperature sensor (only type
D305H and D307H)
023 Room temperature sensor (only
type D305H and D307H)
044 Remote control
040 Operating instructions
041 Installation instructions
042 Service instructions
Parts list, external units
Type OS303H to OS307H
When ordering spare parts:
Quote the part and serial no. (see
type plate) and the item no. of the
required part (as per this parts list).
Obtain standard parts from your local
supplier.
Parts
001 Compressor
002 Fan motor
003 Fan impeller
004 Four-way reversing valve
006 Compressor temperature sensor
007 Temperature sensor
010 Electronic expansion valve
013 Outside temperature sensor
014 Controller
015 Coil for electronic expansion
valve, white, 530 mm (only type
OS303H and OS304H)
Coil for electronic expansion
valve (only type OS305H and
OS307H)
040 Operating instructions
041 Installation instructions
042 Service instructions
Parts lists, internal devices
(cont.)
43
Parts lists
5692
687
GB
Summary of Contents for Vitoclima 300-S
Page 54: ...54 5692 687 GB ...
Page 55: ...55 5692 687 GB ...