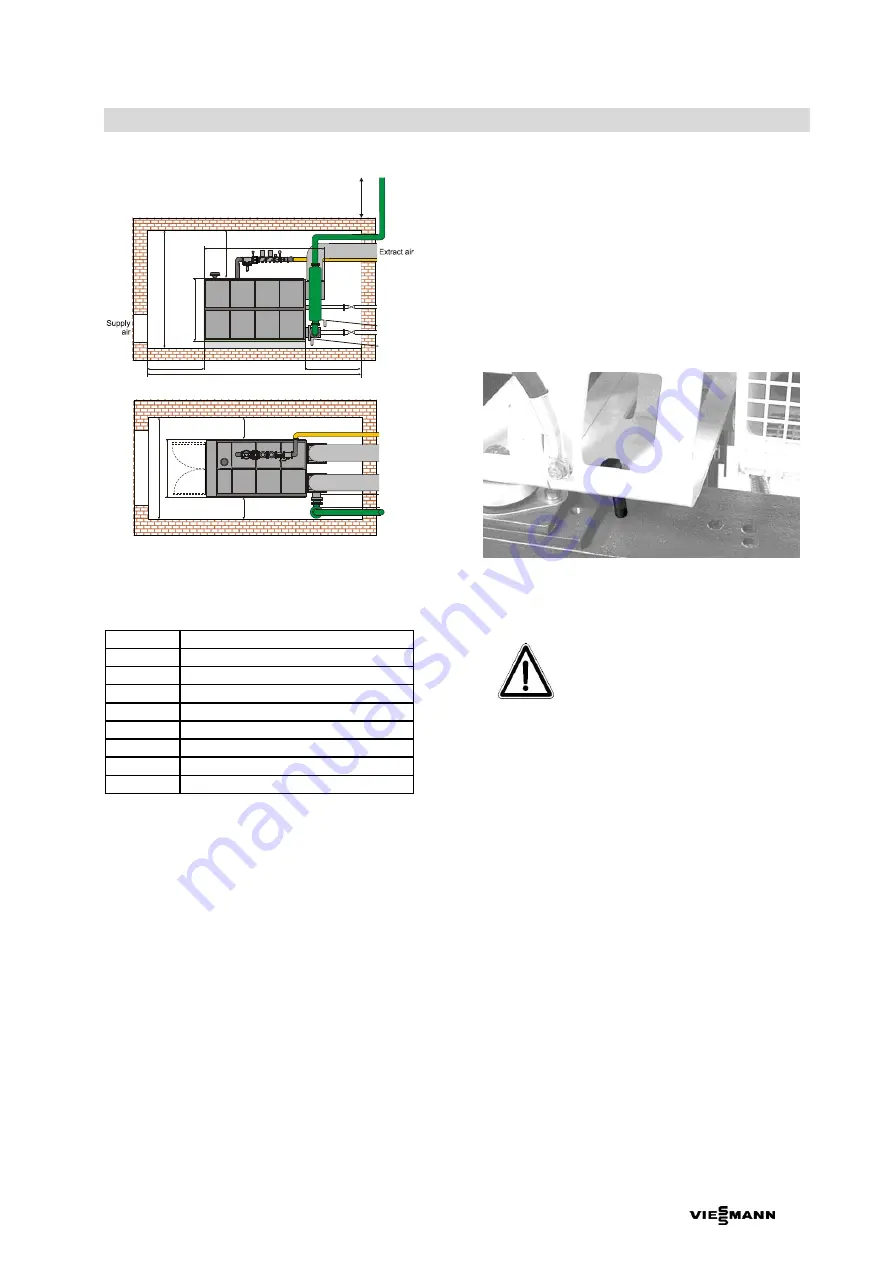
Transportation
VITOBLOC 200 BM-190/238
Assembly instructions
17
5780045
GB
G
G
H
I
Supply
air
Gas
Extract air
Condensate
Exhaust gas
Horizontal projection
Extract air
Condensate
D
C
A
B
E
F
1
m
Exhaust gas
Gas
Heating water
Condensate
Heating water
Condensate
Cut
K
Fig. 6
Minimum distances in the technical room
(dimensions in mm)
A
1,000 mm
B
2,000 mm
C
6,600 mm
D
4,333 mm
E
2,070 mm
F
3,500 mm
G
1,100 mm
H
1,650 mm
I
3,850 mm
Tab. 7
Minimum distances in the technical room
3.5
Removing the transport securing
devices
●
Remove the packaging and send it for recycling.
●
Remove four transport securing devices at the
elastic supports of the engine and alternator
(Fig. 7)
Fig. 7
Remove four transport securing devices at the
elastic supports of the engine and alternator
CAUTION
Always remount the transport locking
device when the block-type thermal
power station is removed after final
shut-down. Otherwise, there is a risk
that the motor-generator unit will tear off
from the basic frame if not transported
vertically, which can endanger the
transport personnel.