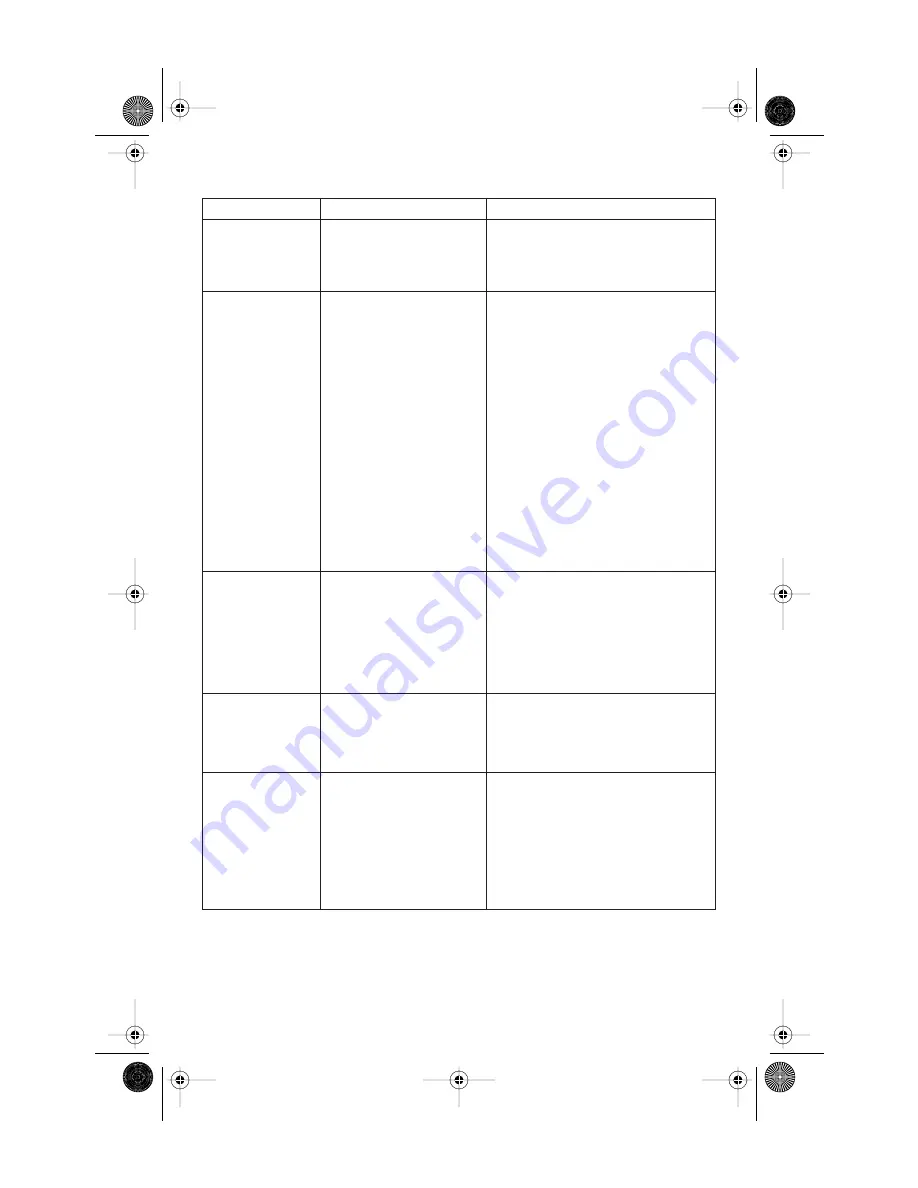
28
VE46 Pipe Roll Grooving Tool
TOOLS INSTALLED ON A POWER DRIVE
Problem
Possible Cause
Solution
Pipe will not stay in the
grooving rolls.
Incorrect pipe positioning of
long pipe length.
Refer to the "Long Pipe Lengths" section on
page 15.
Roll set and pipe are not
rotating
clockwise
.
Flip the switch on the power drive to the
opposite rotation position.
Pipe stops rotating
during grooving.
Rust or dirt buildup is present
on the roll set.
Remove rust or dirt accumulation from the
roll set with a stiff wire brush.
Rust or dirt is excessively heavy
inside the pipe end.
Remove heavy rust and dirt from inside the
pipe end.
Worn roll set.
Inspect the roll set for worn knurls. Replace
the roll set if excessive wear is present.
Power drive has stalled due to
over-advancing the grooving
roll.
Make sure the pipe is supported. Release
the pipe by turning the feed nut
counterclockwise
, which will retract the roll
arm and grooving roll to the fully open
position. Refer to the "Grooving Operation
For Power Drive Setup" section on page 22
to start the grooving process again.
The circuit breaker has tripped
or a fuse has blown out on the
electrical circuit that supplies
the power drive.
Reset the breaker, or replace the fuse.
While grooving, loud
squeaks echo through
the pipe.
Incorrect pipe support
positioning on long pipe. Pipe is
“over-tracking.”
Re-position the pipe/ support. Refer to the
"Long Pipe Lengths" section on page 15.
Pipe is not cut square.
Cut the pipe end squarely.
Pipe is rubbing excessively on
the two pipe-end stops.
Remove the pipe from the tool, and apply a
light coating of grease to the two pipe-end
stops, as needed.
During grooving, loud
thumps or bangs
occur approximately
once every revolution
of the pipe.
Pipe has a pronounced weld
seam.
Grind the raised welds flush with the interior
and exterior pipe surfaces 2 inches (50 mm)
back from the pipe end.
Pipe flare is
excessive.
Pipe support is not adjusted
properly for a long length of
pipe.
Refer to the "Long Pipe Lengths" section on
page 15.
Tool is tilted backward while
grooving a long length of pipe.
Refer to the "Long Pipe Lengths" section on
page 15.
Incorrect pipe support
positioning of a long length of
pipe. Pipe is “over-tracking.”
Re-position the pipe support. Refer to the
"Long Pipe Lengths" section on page 15.
TM-VE46 1924 Rev_B.fm Page 28 Wednesday, January 19, 2005 8:59 AM