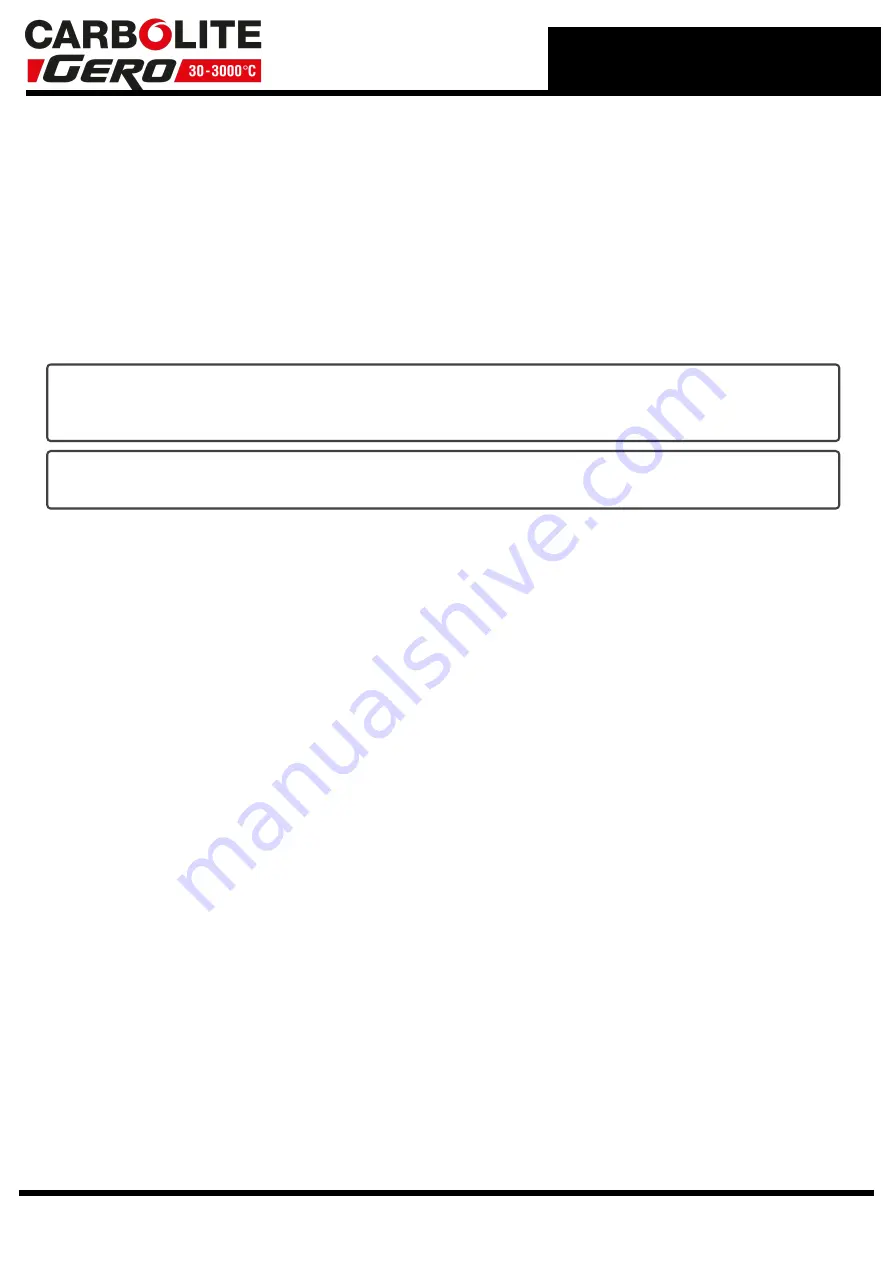
11.0
Using Autotune to Optimise Temperature Control
All Carbolite Gero products are preconfigured for optimum performance when used
within their normal expected operating temperature range.
Depending on the intended application, it may be necessary for the product to be used
outside of this normal range, in which case some tuning may be required in order to
optimise the PID controls within the temperature controller e.g. if a high temperature
product is to be used at a significantly lower temperature than it was originally designed
for, or if a particularly heavy sample/load is to be heated.
Note:
The following instructions are intended for use on single-zone products. Please
contact Carbolite Gero Service for assistance if it is necessary to auto-tune a product
with multiple heated zones or cascade control fitted.
Note:
The 3016 contains two sets of PID terms, therefore it may be necessary to
autotune at temperatures within both PID sets.
To use the Autotune function:
1. Ensure that the product is cold (at ambient temperature) before proceeding.
2. On the home display, set the setpoint temperature to 0°C .
3. Log in as Operator Level
3
(see section 4.0).
4. Navigate to the
AtuN
sublist in for the main controller (see section 9.0).
5. Use the up and down buttons to switch the
TUNE
parameter from
Off
to
On
. The
auto-tune function will now go into stand-by mode for 30 seconds
6. Before the stand-by mode period lapses, navigate to the home display and set the
product setpoint to the temperature you wish to optimise the product for e.g.
400°C
7. The controller will remain in stand-by mode for a few minutes. <
AUTOTUNE
ACTIVE
> will scroll along the bottom of the home display when the product begins
the autotuning cycle:
l
The controller heats until it is within a few degrees (°C / °F / K) of the pro-
grammed setpoint
l
The controller then cuts off power to the heating elements
l
The controller allows the temperature to overshoot the target setpoint
l
When the temperature drops below the point at which the controller stopped
heating, it turns the power to the heating elements back on
l
The controller will then allow the temperature to undershoot (not reach the
target setpoint)
l
The controller analyses the information it received from the overshoot and
undershoot scenarios, and calculates new PID terms that will optimise tem-
perature control for the new temperature range
l
The new PID terms are applied, and the controller then heats as normal until
it reaches the target setpoint, then maintains that setpoint
43