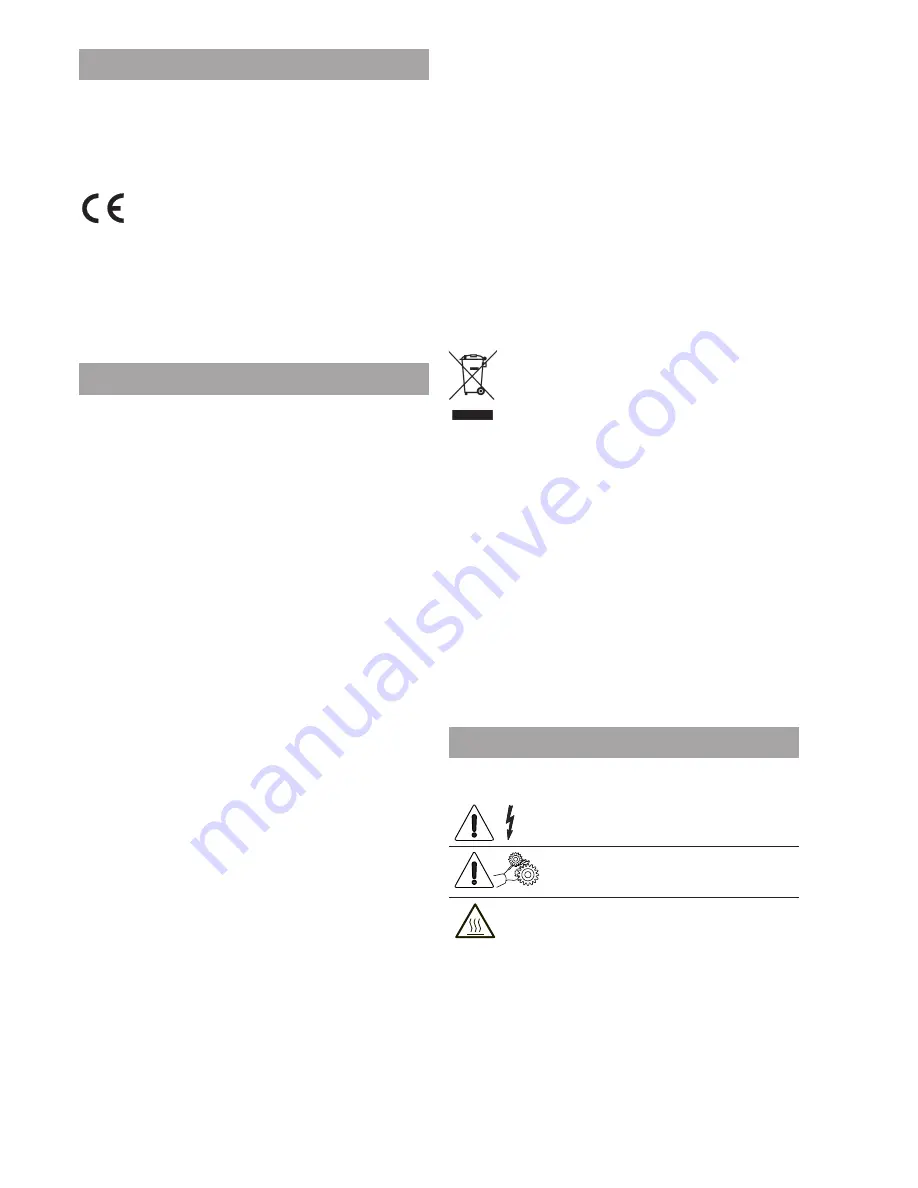
Declaration of conformity
The declaration of conformity with the European Direc-
tives and Standards provided for by the laws in force
is supplied by the first page of this manual, which is an
integral part of the machine.
It is declared that the machine described by
the identification plate is in compliance with the
provisions of the European Directives, its sub
-
sequent amendments and integrations as well as with
the harmonised standards or technical specifications
(designations) applied in compliance with the safety
rules of good practice enforced in the EU and listed on
the same page.
Warnings
for
installation
The installation and any subsequent maintenance
operation shall be carried out by the personnel
skilled and trained on the utilisation of the machine
according to the rules in force.
The machine is sold without any payment system. As
a consequence, only the installer will be liable for any
damage that may be caused to the machine or to things
and persons by an incorrect installation of the payment
system.
The intactness of the machine and its compliance
with the standards of relevant installations must be
checked by skilled personnel at least once a year.
Package materials must be disposed of in observance of
the environment.
Important!
The machine is equipped with an automatic wash-
ing system for the mixers with the relative water
circuit and the brewing unit.
If the machine is not used for some time (weekends,
etc.) even for pauses longer than two days, it is recom
-
mended to enable the automatic washing functions (e.g.
before starting to use the VM).
for
use
The machine can be used by children and by people
having reduced physical, sensorial or mental skills under
the supervision of people responsible for their safety or
specifically trained on the use of the machine. Children
shall be prevented from playing with the machine by the
people in charge of their supervision.
for
the
environment
Some tricks will help you to protect the environment:
- use biodegradable products to clean the machine;
- properly dispose of all the packages of the products
used to fill and clean the machine;
- power off the machine during inactivity for energy sav
-
ing.
for
dismantling
and
disposal
When dismantling the machine, it is recommen
-
ded to destroy the machine rating plate.
The symbol shows that the machine can not be
disposed of as common waste, but it must be
disposed of as it is established by the 2002/96/
CE (Waste Electrical and Electronics Equipments -
WEEE) European Directive and by the national laws
arising out of it in order to prevent any negative conse
-
quence for environment and human health.
The differentiated collection of the machine at the end of
its life is organised and managed by the manufacturer.
For the correct disposal of the machine contact the sales
point where you have purchased the machine or our
after-sales service.
The unlawful disposal of the machine implies the appli-
cation of the administrative sanctions provided for by the
rules in force.
Attention!
If the machine is equipped with a cooling system, the
cooling unit contains HFC-R134a fluoridised greenhouse
effect gas ruled by the Kyoto protocol, the total heating
potential of which is equal to 1300.
Symbology
The following symbols may be present inside the machines,
according to models:
Attention: dangerous voltage
Power off before removing the cover
Attention
Danger of crushing your hands
Attention
Hot surface
Summary of Contents for KARISMA
Page 2: ......
Page 5: ......
Page 6: ......
Page 60: ...by N W GLOBAL VENDING S p A 54 02 2014 4535 00 This page is intentionally left blank...
Page 72: ......