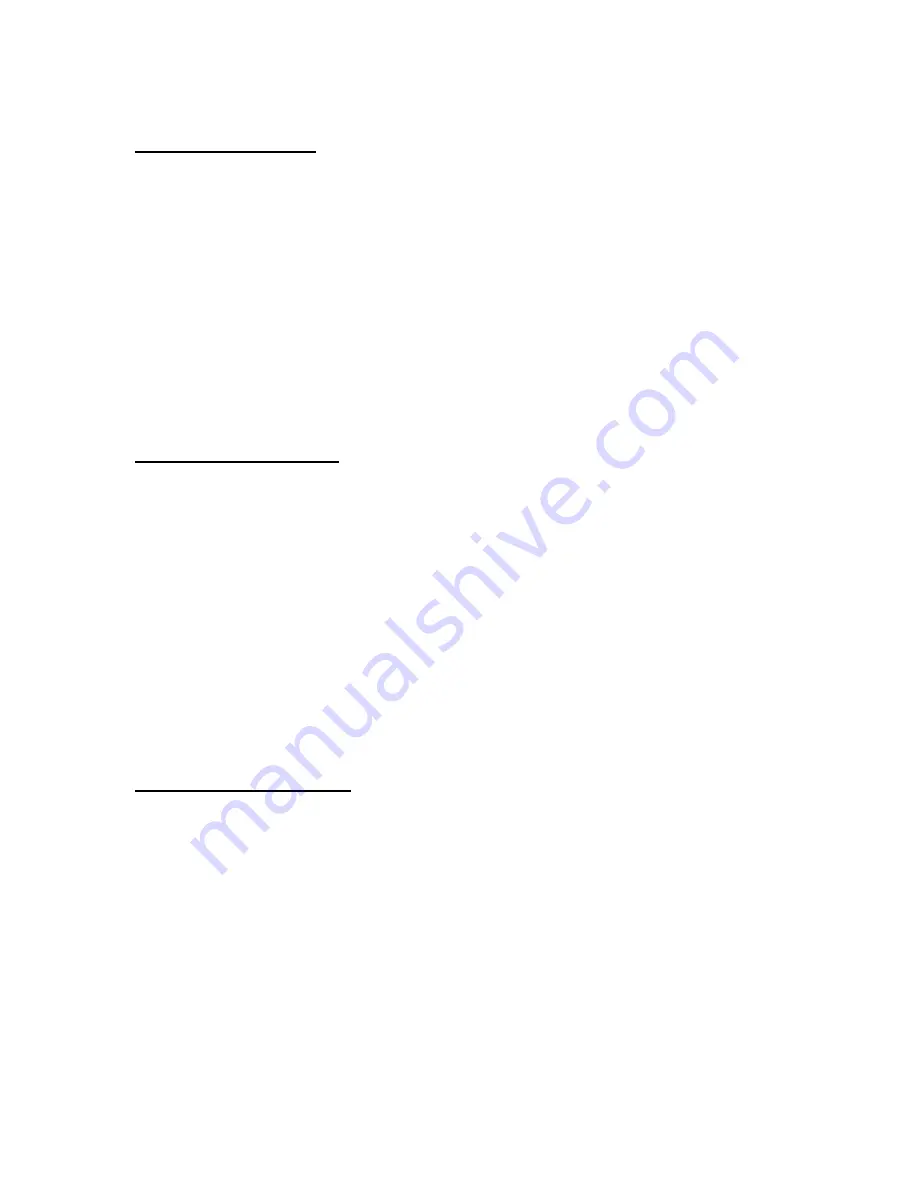
INSPECTION SCHEDULE
DAILY INSPECTIONS
•
Remove any film build up in chain grippers, around sprockets and in the chain guides.
•
Remove debris in the form and seal die bottoms.
•
Wear protective gloves to clean and inspect the cutting blades.
o
Clean with anti-corrosive agents and lubricate with non-acid oils.
•
Clean spindle threads with a wire brush.
o
Threads will have build-up of cardboard shavings from film core.
•
Replace any damaged grippers in film transport chain.
•
Examine all safety guards and emergency stops for damage.
o
Repair or replace as needed
•
Examine radius plates for debris or damage.
o
Make sure all vent holes are clear.
•
Clean the machine per your company standards.
o
Do not use corrosive or acidic agents.
•
Dry the machine by hand or with compressed air to remove standing water.
•
Lubricate all metal surfaces with a light coating of mineral oil or equivalent.
WEEKLY INSPECTIONS
•
Examine seal gasket(s) and all o-ring seals in the form and seal tooling.
•
Inspect for damage or contamination on the form heat plate, seal plate(s) and the seal die top
cavity.
o
Clean as needed making sure all vent holes are clear on the form heat plate and there is
no contamination inside the seal die top cavity.
•
Inspect and clean the seal die bottom for pin gas applications.
•
Replace cutting blades as needed using protective gloves.
•
Test the safety fault indicators on the machine when each guard is removed.
•
Make sure the machine cycle is stopped when each guard is removed.
•
Test emergency stop switches.
o
The machine cycle will stop immediately when pressed.
•
Clean and lubricate the gripper chain.
•
Check oil level in the vacuum pump.
•
Perform a vacuum test on the seal die chamber.
•
Make sure the film tension systems and the film tracking adjustments are functioning
properly.
MONTHLY INSPECTIONS
•
Tension chain by using chain tensioners (see exploded view).
o
Remove a link if necessary.
•
Check lubricator in the pneumatic cabinet for the low pressure manifold.
o
Examine oil level and oiling rate.
o
Oilier should give one drop in 3 minutes (open approximately ¾ turn).
•
Check PLC battery
o
The PLC battery indicator light is located on the front of the PLC. If the red light is on, the
battery is low and needs to be replaced
o
The battery is located on top of the PLC under a small cover approx. 40mm long 15mm
wide
o
When the battery is unplugged you have 20 seconds to reconnect the new battery before
you lose stored parameters.
•
Grease both chain drive shaft bearing zerts as well as single zert on non-form film unwind.
Summary of Contents for RS420
Page 6: ...SECTION 1 SAFETY...
Page 11: ...SECTION 2 TRANSPORTATION...
Page 13: ...SECTION 3 INSTALLATION...
Page 19: ...SECTION 4 INTERFACE TOUCH SCREEN...
Page 26: ...SECTION 5 MAINTENANCE INSPECTION SCHEDULE...
Page 39: ...SECTION 6 TROUBLESHOOTING GUIDE...
Page 55: ...SECTION 7 PNEUMATIC DIAGRAMS...
Page 73: ...SECTION 8 ELECTRICAL DIAGRAMS...
Page 91: ...SECTION 9 PARTS LIST ASSEMBLY DRAWINGS...
Page 148: ...Parts 8 12 Vacuum Valve O Ring Replacement Kit...
Page 149: ...SECTION 10 DIE ASSEMBLY DRAWINGS...
Page 156: ...NOTES...
Page 157: ...NOTES...