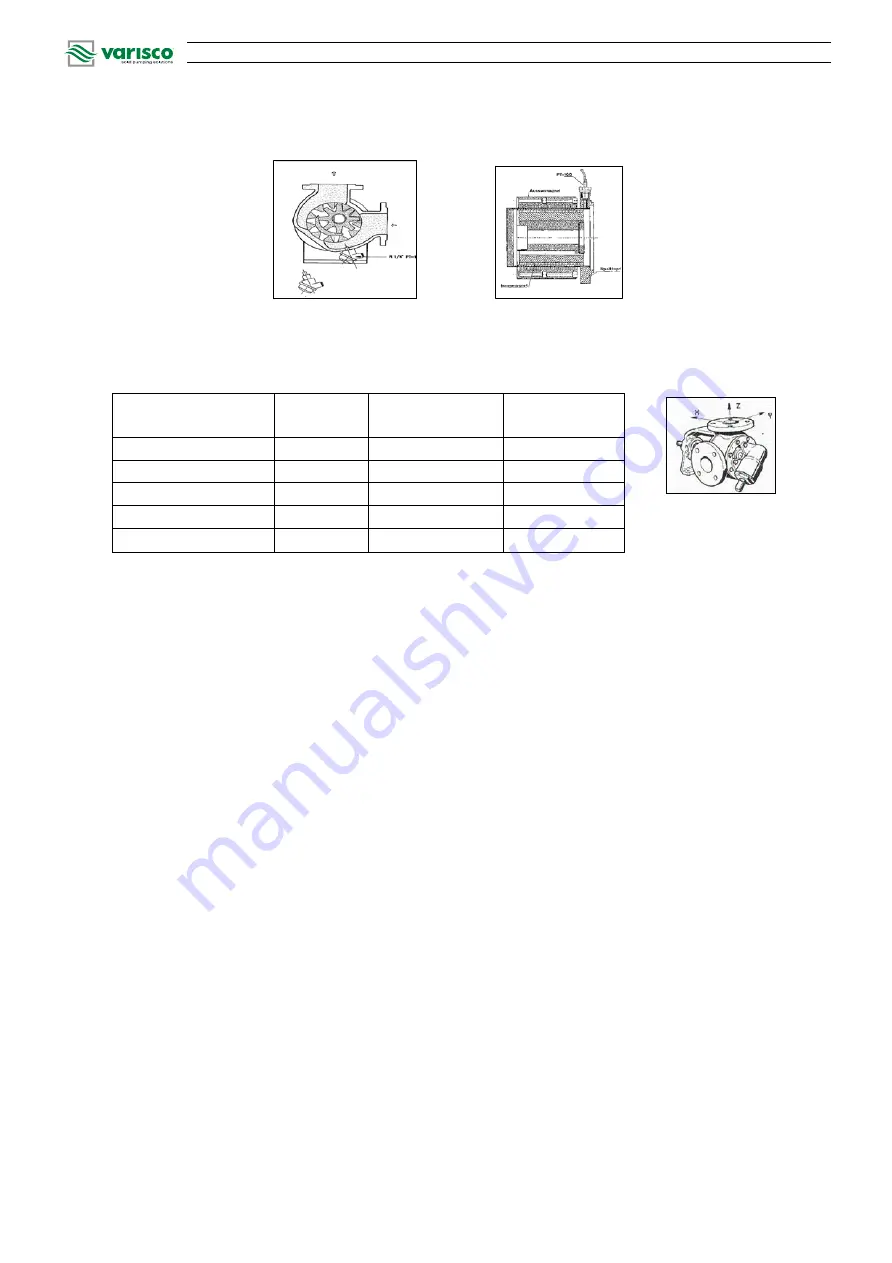
OPERATING MANUAL -
SAXMAG V
Page 18
Temperature monitoring
4.3.5 Permissible forces, torques and moments on the pump branches
Pump Type
Flange
(DN)
F
x
, F
y
, F
z
N
M
x
, M
y
, M
z
Nm
V6, V12
15
196
99
V20, V25-2, V30-2
40
520
260
V60-2
50
650
330
V80-2
80
1,040
520
V100-2
100
1,300
660
4.3.6 Expected noise
The sound pressure level of V-Series Varisco pumps with drive, as measured at the pump height at 1 m
distance from the pump, is less than 75 dB for all models.
4.4
Accessories
Shaft coupling: flexible coupling with / without adapter sleeve
Touch guard:
coupling guard
Baseplate:
welded fabrication, for complete (to ISO 3661) unit (pump and motor) of torsionally
rigid design.
Where complete units are delivered the coupling and the coupling guard will be
furnished by the supplier.
4.5
Dimensions and weights
Dimensions and weights can be seen from the pump's installation drawing.
5
Mounting/Installation
5.1
Safety regulations
Equipment operated in potentially explosive atmospheres must comply with relevant explosion
protection regulations. This requirement is clear from the rating plates of the pump and the motor.
Persons who have a pacemaker should not be allowed in the vicinity of the strong magnetic field
generated by the magnetic coupling. Persons within 2 m of the pump would be risking their lives!
Summary of Contents for SaxMag V Series
Page 34: ...Page 34...
Page 35: ...Page 35...