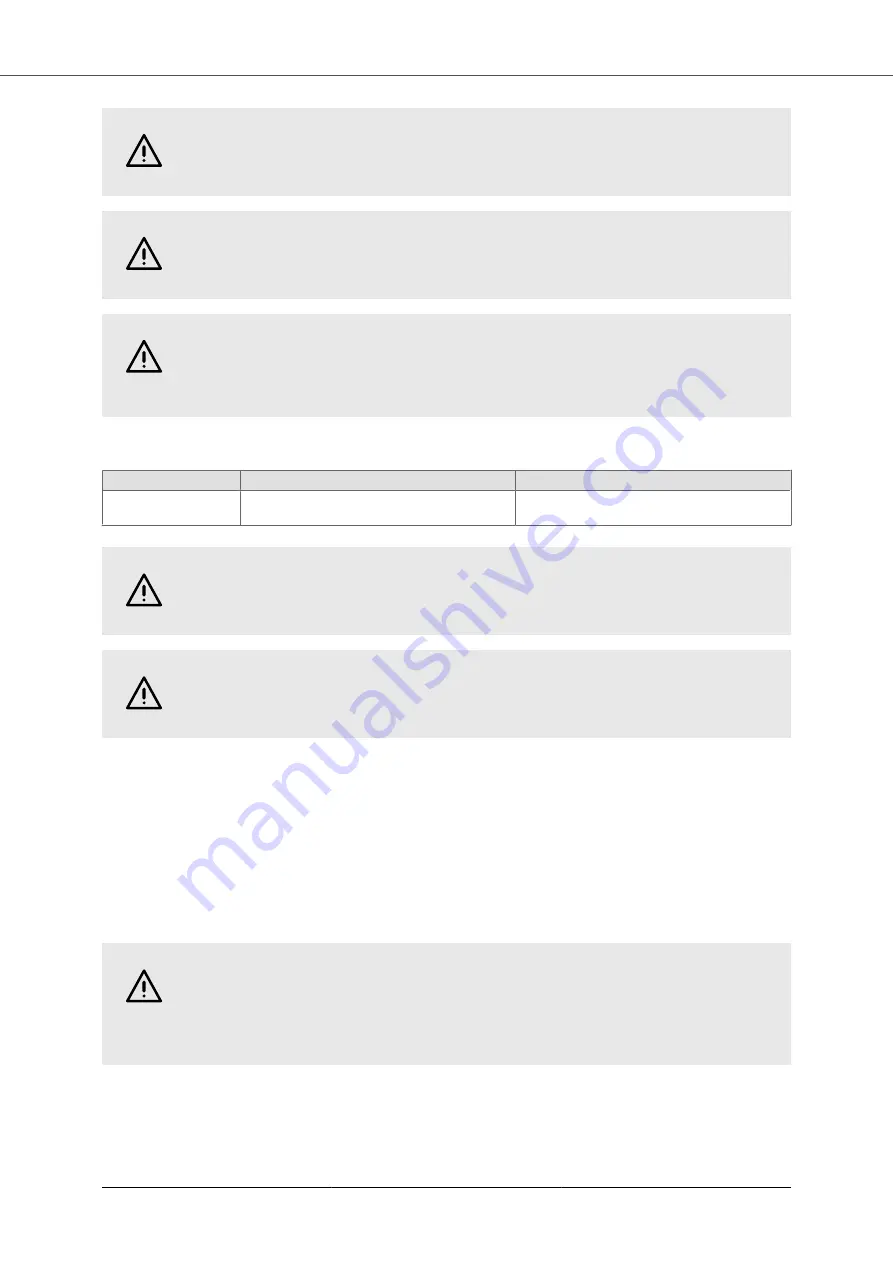
WARNING
Use unshielded cable for input cables and shielded cable for output cables.
WARNING
Always use cables with appropriate cable lugs, which may be supplied with the product.
WARNING
For motor cable lengths greater than 5 meters, the use of special output filters, available
on request, is recommended.
7.3.2. Control cables
Model
Maximum cross-section of control cables
Tightening torque [Nm]
Control terminals of
all models
1 mm
2
0,5
WARNING
Use shielded cable for control cables.
WARNING
Always use cables with appropriate cable lugs, which may be supplied with the product.
7.4. Electromagnetic compatibility (EMC)
The device meets the requirements for electromagnetic compatibility according to EN61800-3.
However, to ensure the electromagnetic compatibility of the system in which it is installed, the following
is necessary:
• Use ground cables that are as short as possible.
• use motor cables that are as short as possible and shielded with the shield connected at both ends.
• use shielded signal cables with the shield connected at one end only.
WARNING
Install signal, motor, and power cables separately from each other at a distance of at least
30 cm. If the interconnected signal cables are to meet the speaker cables, cross them at
right angles.
PSDrive
24