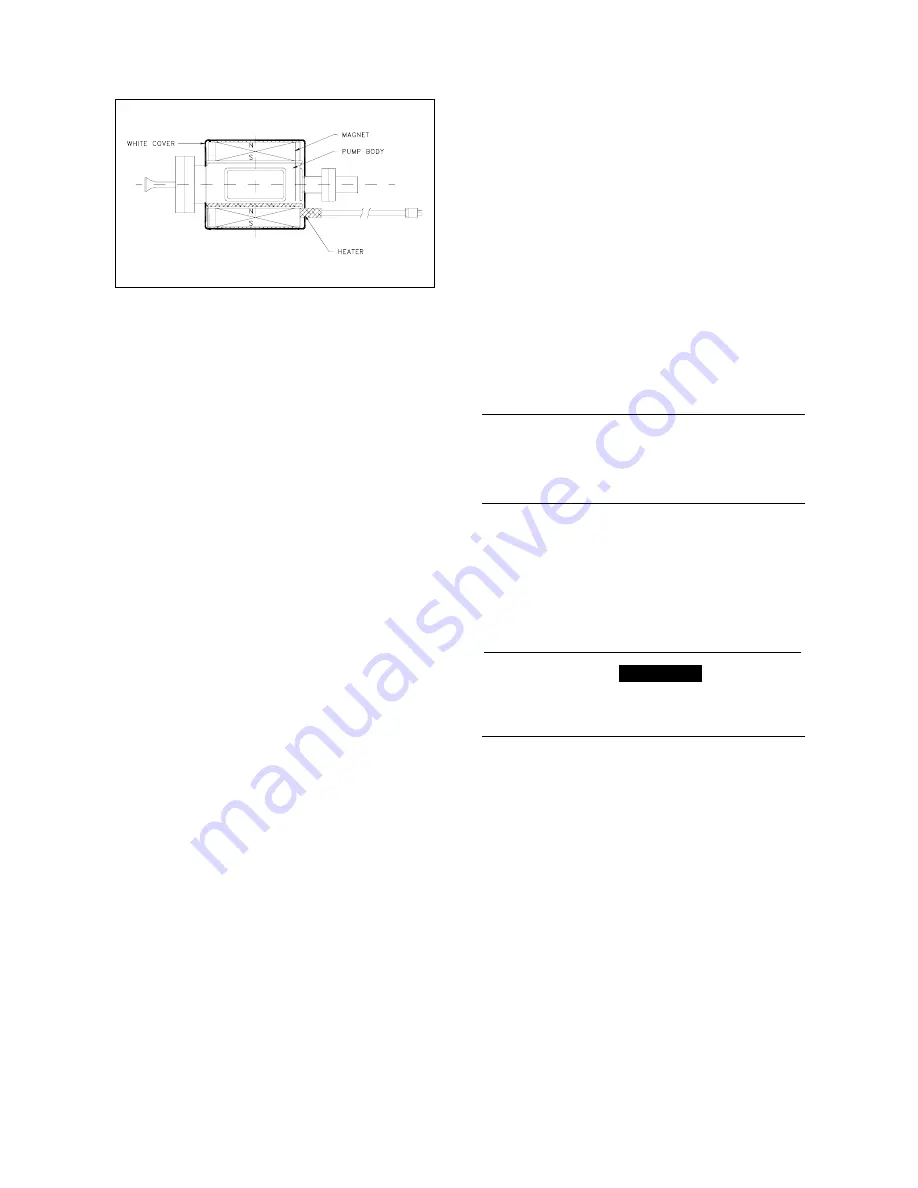
TECHNICAL INFORMATION
Fig. 18 - Heater element mounting
(cover removed)
HEATER REPLACEMENT
To replace the pump heaters, first remove the
faulty heater following, in the reverse order, the in-
structions of the paragraph “HEATER
INSTALLATION”, and then reassembly the new
heater following the instructions of the above men-
tioned paragraph.
BAKEOUT OPERATION
When a VacIon pump does not reach the desired
base pressure, and there are no leaks, it is neces-
sary to bake the system. This is done by heating
the pump and all the components in the system,
and is generally required to achieve base pres-
sures less than 10
-8
Torr (mbar).
1. Heat the pump body and the system with a
bakeout oven unit or heating strips to tempera-
tures between 150 °C and 250 °C (250 °C is
the maximum allowable for most bakeable high
voltage cables). This temperature is high
enough to degas the pump surfaces of water
vapor without damaging the magnet and high
voltage connector. Note that the system com-
ponents must be compatible with the bakeout
temperature. The heating must be approxi-
mately even on all surfaces or evaporated wa-
ter will condence on the colder surfaces
resulting in an incomplete bake and preventing
achievement of UHV vacuum pressure.
2. Leave the pump control unit on and monitor the
pressure. Varian recommends that current dur-
ing bake not exceed 10 mA; if this value is ex-
ceeded, turn the bakeout off and then on again
when low pressure is restored. To control the
heaters and to monitor the high pressure limit
during bakeout, an automatically controlled re-
lay may be used.
3. Bake the VacIon
Plus
pump for at least 24
hours. Longer bakeout periods are recom-
mended when the pump has been used with
heavy gas loads or when UHV pressure, 10
-9
Torr (mbar) or less is desired.
4. As the pump and system cool down to room
temperature, a drop in pressure should be ob-
served.
Note that the ion pump can be also baked when
switched off, into an external turbo pump through a
bakeable isolation valve. This method gives the
best vacuum performance.
Bakeout of VacIon pump with the integral
heaters
1. The integral heaters are to be powered with the
appropriate voltage. (Please refer to the
inscription on the heaters to apply correct volt-
age).
2. The integral heaters are designed to provide a
temperature of 250 °C to 300 °C when the
pump is wrapped in a 3-fold aluminum foil.
NOTE
A three-layer foil wrapping is advisable and suffi-
cient to achieve full bakeout/regeneration if the
standard European heaters (220 Vac) are oper-
ated at 240 Vac, thus preventing overheating.
3. Bakeout the VacIon pump for 24 hours. If the
pump is used in heavy gas load applications, it
is recommended to bakeout the pump for a
longer period.
4. Wait until the pump cools down to room tem-
perature and recovers its base pressure before
using it in the application.
,
WARNING!
Do not touch the pump during the heating and
cooling phases. The high temperature may cause
serious damage.
OPERATING PROCEDURE
1. Using a clean roughing pump, evacuate the
system to a minimum starting pressure per the
charts on pages from 10 to 12 for the type of
ion pump. 10
-4
Torr (mbar) or less is recom-
mended. A turbo-molecular roughing pump is
recommended.
2. When starting an ion pump, a slight increase
in vacuum pressure is normal as the internal
components are heated and outgassed. If
possible leave the roughing pump connected
to the system while starting the ion pump. This
will make the startup faster and easier.
3. Connect the control unit to a suitable power
source and switch the power on.
4. Switch on high voltage to the pump and ob-
serve the current and voltage. Fastest starting
is obtained using a high applied voltage, 7 kilo-
volts for example. The applied voltage may be
17
87-900-106-01(B)