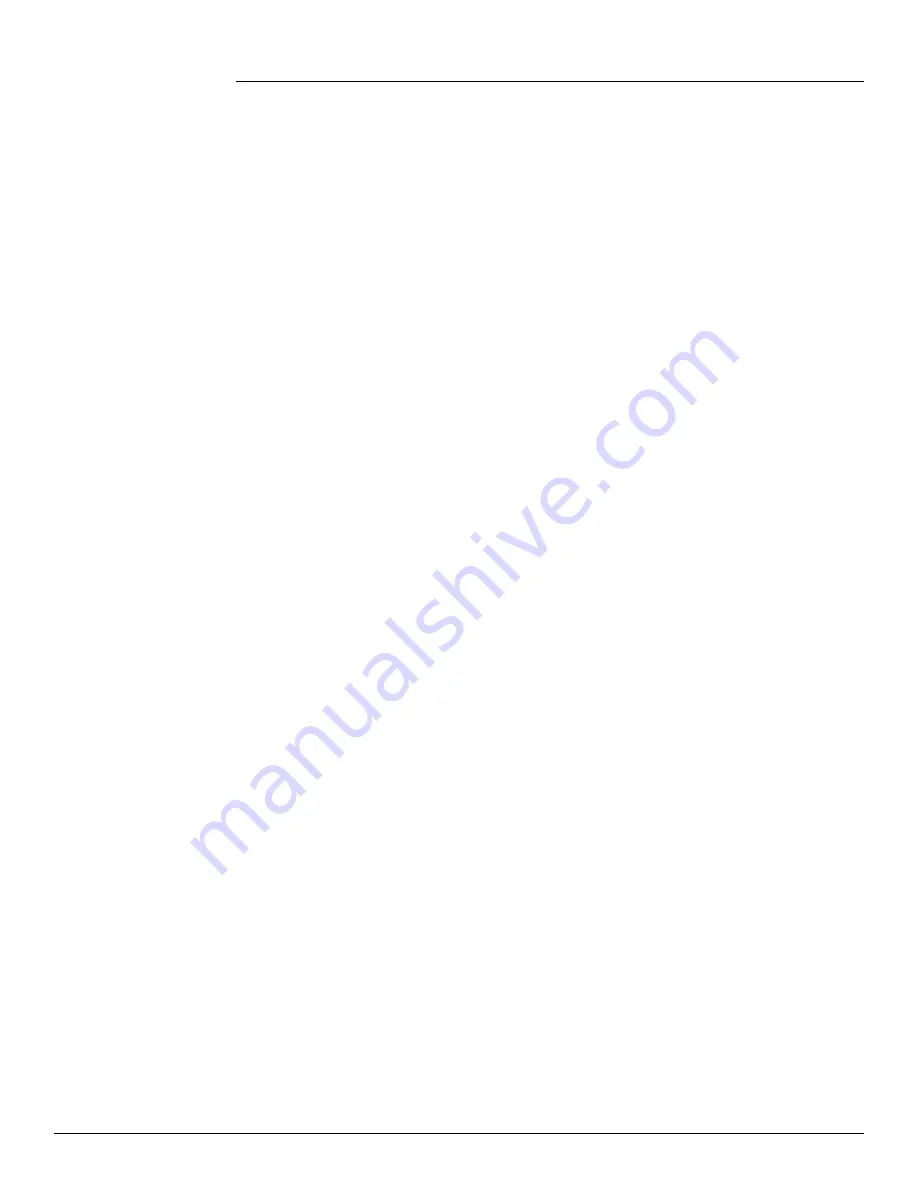
Varec, Inc.
57
Chapter 5
Operation
Caution Do not release the checker knob and allow the springs to return the mecha-
nism
. Over time the springs will break and jam the gauge.
Caution
Do not turn the operation checker knob on systems that have no float and that
are directly connected to a floating roof.
1. For non-crank gauge heads, use the operation checker knob to check gauge operation.
Turn it clockwise one-quarter turn, while observing the display.
Caution
For hand crank gauge heads, do not disengage the crank while the float is above
the surface of the liquid. Do not allow the float to free fall. Damage to the system may
result.
2. For hand crank gauge heads, use the crank to check gauge operation (refer to the initial
operation paragraphs above). If the float is not on the surface of the liquid, slowly rotate
the crank clockwise, while watching the display. When the counters stop, do not continue
to crank.
Note
If the tape becomes slack with the float on the surface, the tape may slip off the
elbow pulley, the tape storage sheave, or the tape keeper. If this occurs, refer to
Chapter 9, Troubleshooting on page 99.
3. Turn the crank counter-clockwise to raise the float about 2 inches (51 mm) above the prod-
uct, then lower it back to the surface. The float should not be left on the surface of prod-
ucts that are agitated. Raise it to the tank top in this situation, and latch the ratchet pawl.
Summary of Contents for 2500
Page 2: ......
Page 6: ...vi Installation and Operations Manual...
Page 10: ...2500 Automatic Tank Gauge 10 Installation and Operation Manual...
Page 16: ...2500 Automatic Tank Gauge 6 Installation and Operations Manual...
Page 66: ...2500 Automatic Tank Gauge 56 Installation and Operations Manual...
Page 68: ...2500 Automatic Tank Gauge 58 Installation and Operations Manual...
Page 108: ...2500 Automatic Tank Gauge 98 Installation and Operations Manual...
Page 112: ...2500 Automatic Tank Gauge 102 Installation and Operations Manual...
Page 118: ...2500 Automatic Tank Gauge 108 Installation and Operations Manual...
Page 123: ......