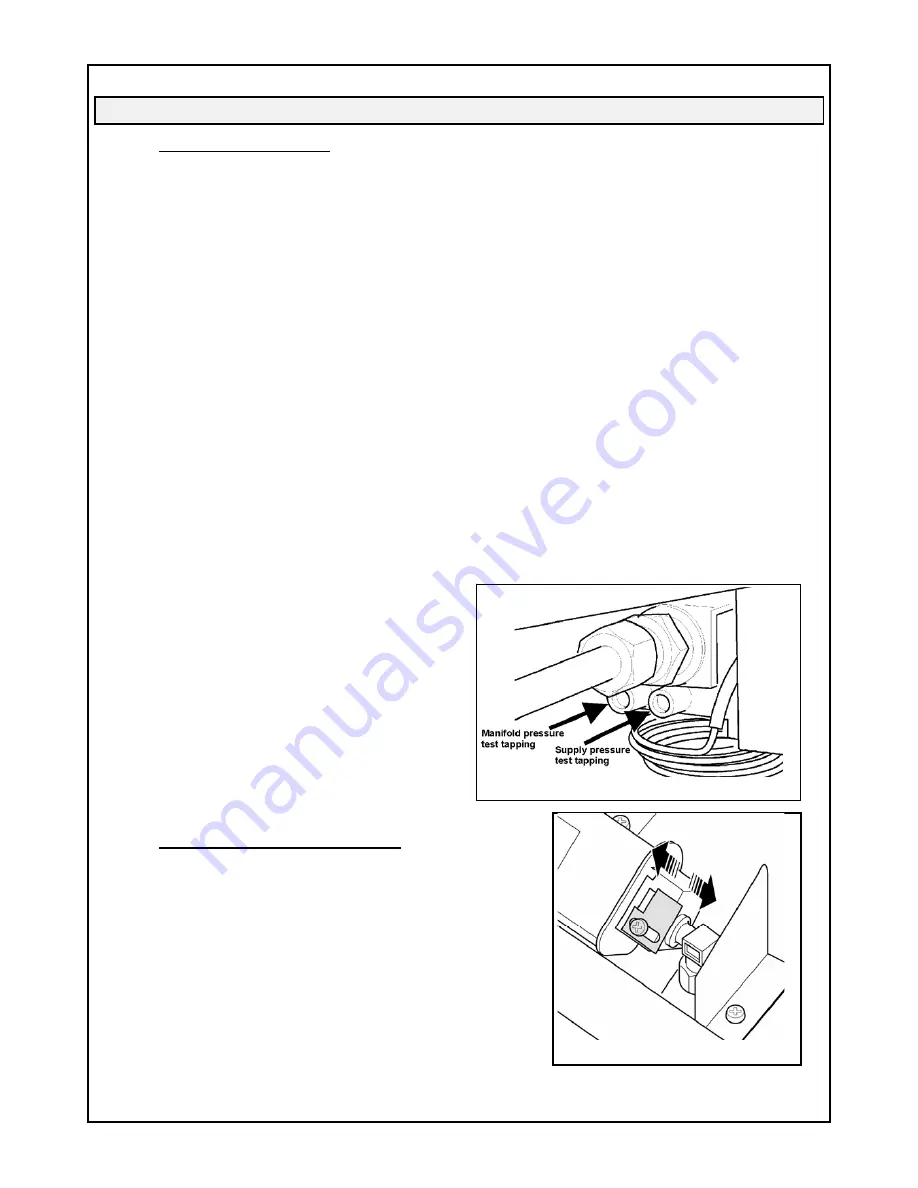
11.
GAS SUPPLY INSTALLATION & AERATION SETTING
11.1.
Gas Supply Installation
The gas supply pipe should enter the appliance case through the opening at the rear left side. The supply pipe should be
connected to the appliance gas inlet pipe situated at the left side of the control unit. Supply line connection to the inlet
pipe is
3
/
8
”NPT.
If the circulating fan is to be installed, be aware that the supply pipe run inside the case should be at the same height
as the appliance inlet pipe in order to clear the fan. If intending to fit an internal isolating valve, check that it will be
clear of the fan.
•
•
•
•
•
•
•
•
•
•
•
•
Use only new black iron or steel pipes or copper tubing if acceptable - check local codes.
Note that in USA copper tubing
must be internally tinned for protection against sulfur compounds.
Unions in gas lines should be of ground joint type.
The gas supply line must be sized and installed to provide a supply
of gas sufficient to meet the maximum demand of the
appliance without undue loss of pressure.
Sealant used must be resistant to the action of all gas constituents including LP gas. Sealant should be applied lightly to
male threads to ensure excess sealant does not enter gas lines.
The supply line should include a manual shut-off valve to allow the appliance to be disconnected for servicing.
A plugged 1/8”NPT tapping must be installed in the line. The tapping must be accessible for test gauge connection and be
immediately upstream of the gas supply connection to the appliance.
Pressure test the supply line for leaks.
f
The appliance and its individual shut-off valve must be disconnected from the gas supply piping system during any
pressure testing of that system at test pressures in excess of ½psig (3.5kPa).
f
The appliance must be isolated from the gas supply piping system by closing its individual manual shut-off valve
during any pressure testing of the gas supply piping system at test pressures equal to or less than ½psig (3.5kPa).
f
Failure to either disconnect or isolate the appliance during pressure testing may result in regulator or valve damage.
Consult your dealer in this case.
The minimum supply pressure is given in section 3 of this manual.
All piping and connections must be tested for leaks after installation or servicing. All leaks must be corrected
immediately.
When testing for leaks:
f
Make sure that the appliance is turned off.
f
Open the manual shut-off valve.
f
Test for leaks by applying a liquid detergent or soap
solution to all joints. Bubbles forming indicate a gas
leak.
Never use an open flame to check for leaks.
f
Correct any leak detected immediately.
The pressure test tapping locations are shown in figure 34. A
built-in non-adjustable regulator controls the burner
manifold pressure. The correct pressure range is shown in
the table in section 3 of this manual. The pressure check
should be made with the burner alight and the thermostat at
its highest setting. See lighting instruction section for full
operating details.
11.2.
AERATION SETTING CHECK
Aeration is factory set.
The setting is non-adjustable for LP appliances.
For natural gas appliances, the shutter is factory set at an aeration gap that
will give optimum performance for the vast majority of installations.
However, in a few unusual installations performance may be improved by
adjusting the aeration. The need for adjustment should be determined by
operating the appliance with the ceramic fuel effects and window installed.
See the “Final checks” section in this manual for adjustment details.
Adjust the aeration by slackening the aeration plate screw and sliding the
plate. In an extreme circumstance, the plate can be totally removed. See
figure 35.
19 of 23
Figure 35 Aeration setting
Figure 34 Pressure test tappings