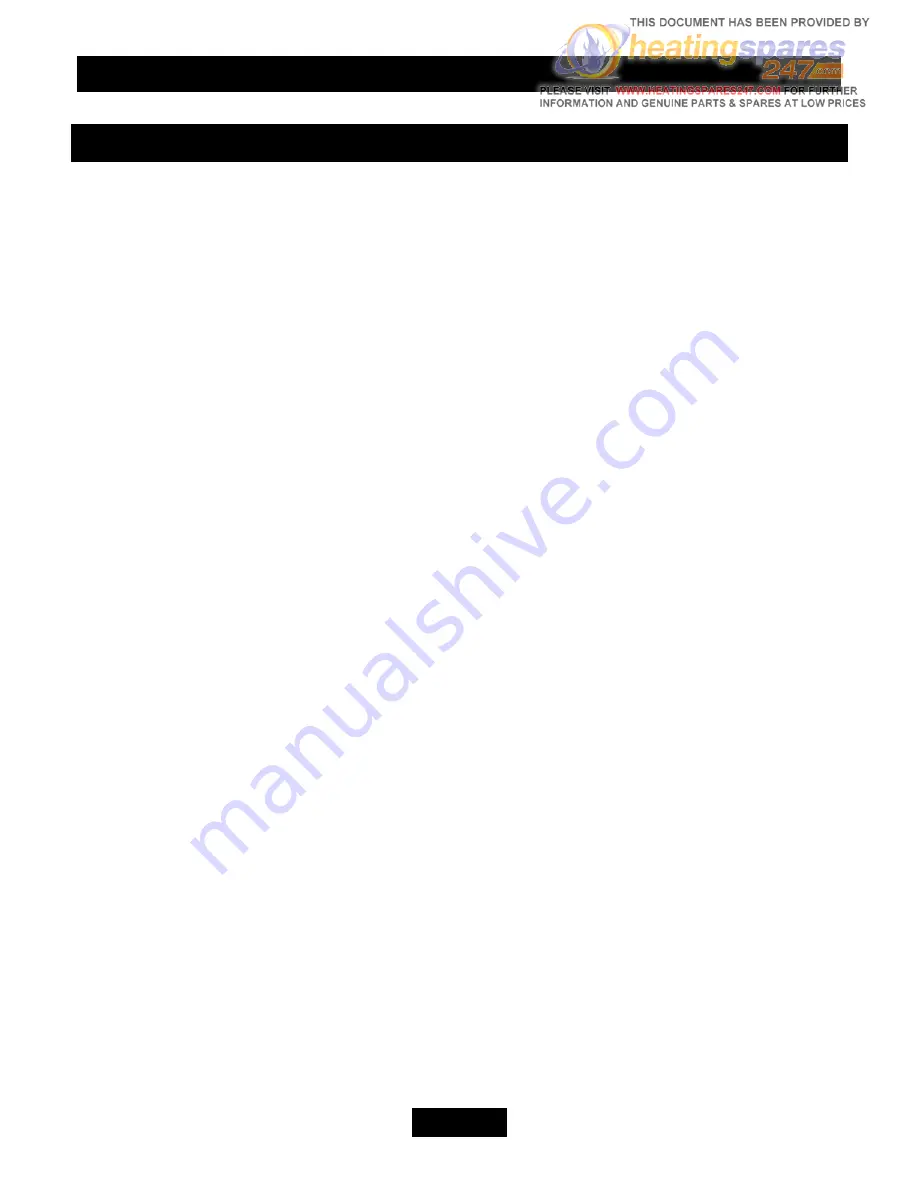
INSTALLER’S GUIDE
Page 19
1 1 S E R V I C I N G & P A R T S R E P L A C E M E N T
•
Always turn off the gas supply before commencing any servicing (The appliance
inlet “T” connector incorporates an isolating valve).
•
It is recommended that, at least once a year, the appliance is disconnected and
the catchment space behind the closure plate checked and cleared of any debris.
The closure plate must be resealed to the wall after checking.
•
Check that soot or debris is not impairing the electrode spark or pilot burner.
•
Check that soot or debris is not blocking any of the holes in the main burner.
•
Always test for gas soundness and spillage after servicing the appliance.
11.1
To Replace Radiant(s)
11.1.1.
Remove the dress guard by pressing down the two hooks at the top. Tilt the
guard forward and lift out.
11.1.2.
Remove the old radiant(s)
Fit the new radiant(s)
ensuring that their rear face
rests against the horizontal ribs in the rear panel.
There will be a small gap between
their bottom front edge and the retaining channel at the front of the radiant box.
11.1.3
Replace in the reverse order.
11.2
To Remove the Outer Case
11.2.1
Remove the control knob by pulling clear of the gas tap spindle.
11.2.2.
Remove the two case retaining screws located at the sides of the case near the
bottom.
11.2.3.
Lift the case up and forward to clear the rear top location.
11.2.4.
Replace in the reverse order. Make sure that the outer case top rear strip locates in
front of, but touching, the side extensions of the engine back panel. See figure 11 in the
installation section.
Make sure that the radiants are not dislodged when refitting the case.
11.3
To Replace the Pilot Unit
11.3.1.
Remove the outer case as section 11.2 above.
11.3.2.
Disconnect the thermocouple connection at the bottom of the gas tap.
11.3.3.
Disconnect the pilot pipe from the gas tap. It is the upper connection at the right
side of the tap.
11.3.4.
Remove the first screw securing the dust cage to the pilot unit & burner bracket.
Carefully remove the dust cage and place aside. Remove the second screw securing the
pilot unit to the burner bracket.
11.3.5.
Disconnect the electrode lead from below the pilot electrode.
11.3.6.
Carefully remove the pilot unit together with the pilot pipe then disconnect the
pipe from the pilot unit.