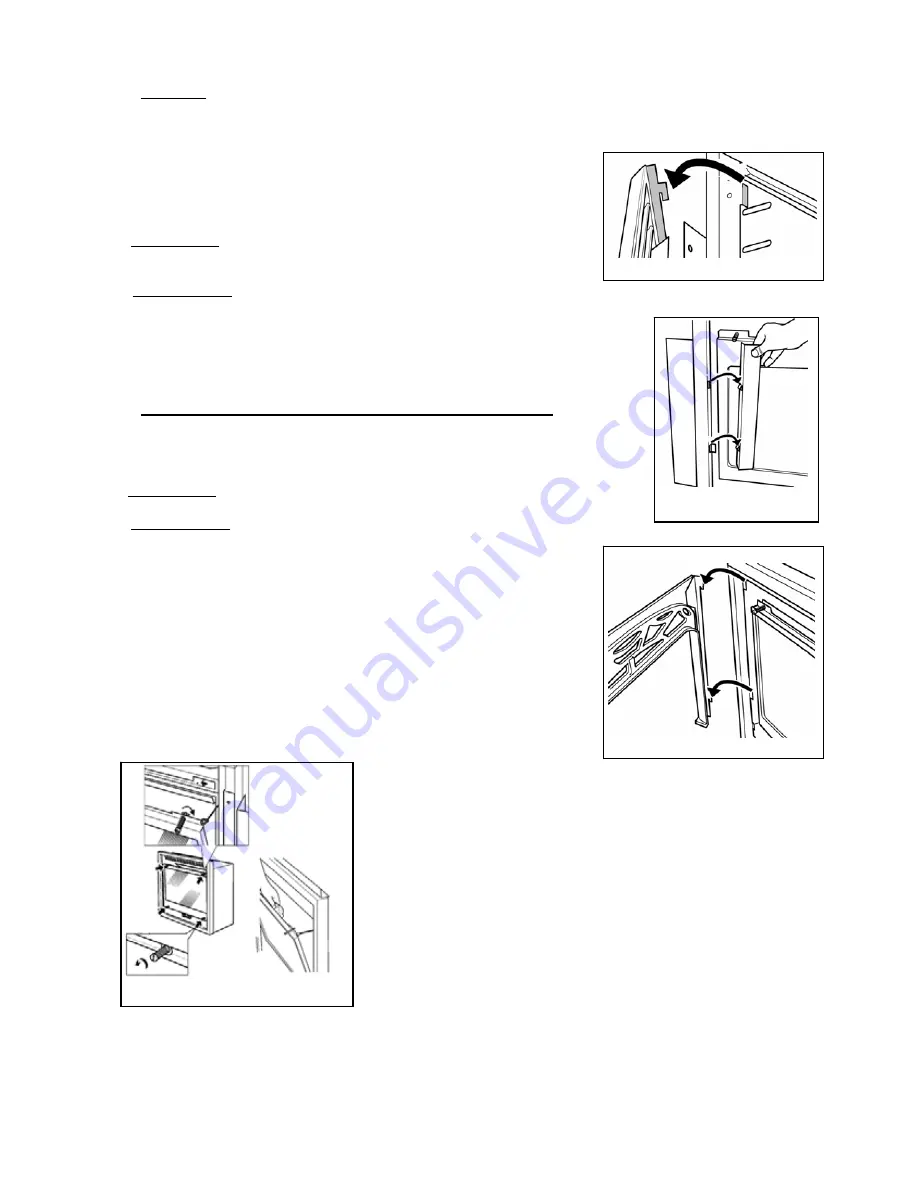
28
16.2.
Cleaning
It will be necessary to clean the glass periodically. During startup, condensation, which is normal, forms on the inside of the
glass and causes dust, lint etc. to cling to the glass surface. Initially paint, while curing, may deposit a slight film on the glass.
We therefore recommend that, during the first few weeks of use, the glass is cleaned two or three times with non-abrasive
common household cleaners and warm water.
Ammonia based cleaners should not be
used.
Subsequently the glass should be cleaned two or three times a season depending
on the circumstances.
Do not clean the glass while it is hot.
Always close the window securely before lighting
16.2.1.
To Clean the Inside of the Glass
•
Louver Fronts: Lift and unhook the top louver – see figure 59. Lift and unhook
the two side channels – see figure 60. Open the bottom louver – It does not need to be
removed.
•
Cast Iron Fronts: Lift up and unhook the upper casting. The bottom casting does
not need to be removed. See figure 61.
•
Push in the three spring loaded bolts at the top of the window and make a quarter turn so
that the slots in the bolt heads are horizontal. This will release the top of the window. Swing the
top of the window open as far as the chain will allow. The window should be open enough to let
you clean the inside of the glass. See figure 62.
Always securely fasten the window before lighting.
16.3.
Clean the Ceramic Fuel Effects, Firebox Walls & Burner
Dust, etc. can be brushed from the ceramic fuel effects and firebox walls after removing the
front unit and completely removing the window.
Dust etc. can also be removed from the burner using a soft brush after removing the ceramic fuel
effects.
•
Louver Fronts: Lift and unhook the top louver. Open the bottom louver – It does not need
to be removed. See figure 59.
Cast Iron Fronts: Lift up and unhook the upper casting. Lift up and unhook the bottom
casting. See figure 61.
•
Push in the three spring loaded bolts at the top of the window and make a quarter
turn so that the slots in the bolt heads are horizontal. This will release the top of
the window. See figure 62.
•
Remove the bottom three spring-loaded window bolts. See figure 62.
•
Detach the chain from the top right corner of the window. See figure 62.
•
Carefully lift the window away. Keep the window and bolts in a safe place.
Always completely remove the window before removing the ceramic fuel effects
.
When cleaning, make sure that no particles are brushed into the slots in the burner.
Always securely replace the window securely before lighting.
Figure 62 Window opening & removal
Figure 61 Cast top front removal
Figure 60 Side channel
removal
Figure 59 Louver removal
Summary of Contents for 535XAN
Page 15: ...15...