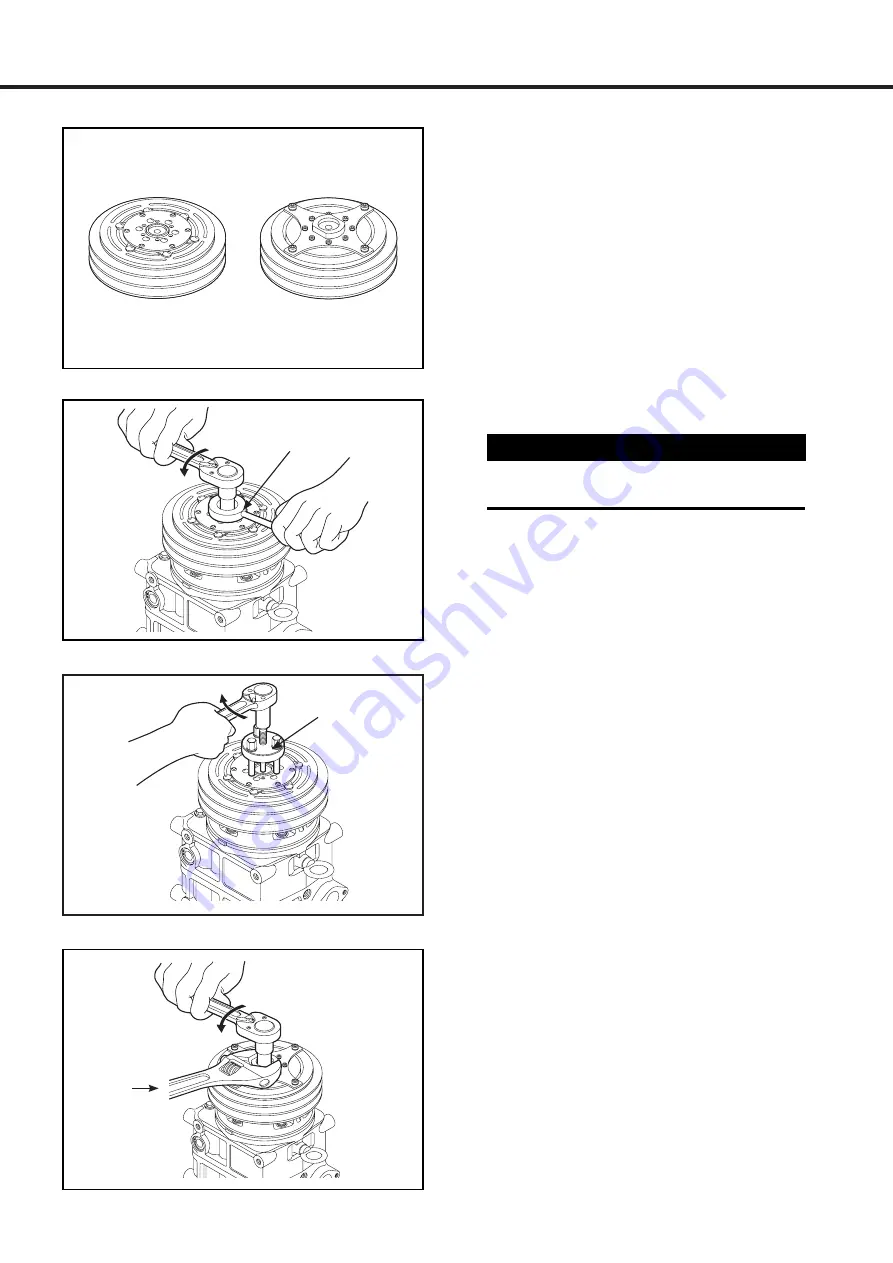
- 28 -
6- Service procedures - Magnetic clutch
Magnetic clutch
Removal
1. Check your armature type (see at left):
• 3-hole type (1)
• 2-way stopper type (2)
2. Remove the armature.
• If it is a 3-hole type armature (1)
a. Remove the center bolt using an armature
holder to prevent armature assembly rotation.
b. Remove the armature assembly using an
armature puller assembly. Remove the shims
from the compressor driveshaft or armature
assembly.
• If it is a 2-way stopper type armature (2)
a. Remove the center bolt using a spanner to
prevent armature assembly rotation.
Armature puller
assembly
Armature
holder
3-hole type (1)
2-way stopper type (2)
CAUTION!
The armature removal process differs
according to the armature type
Spanner