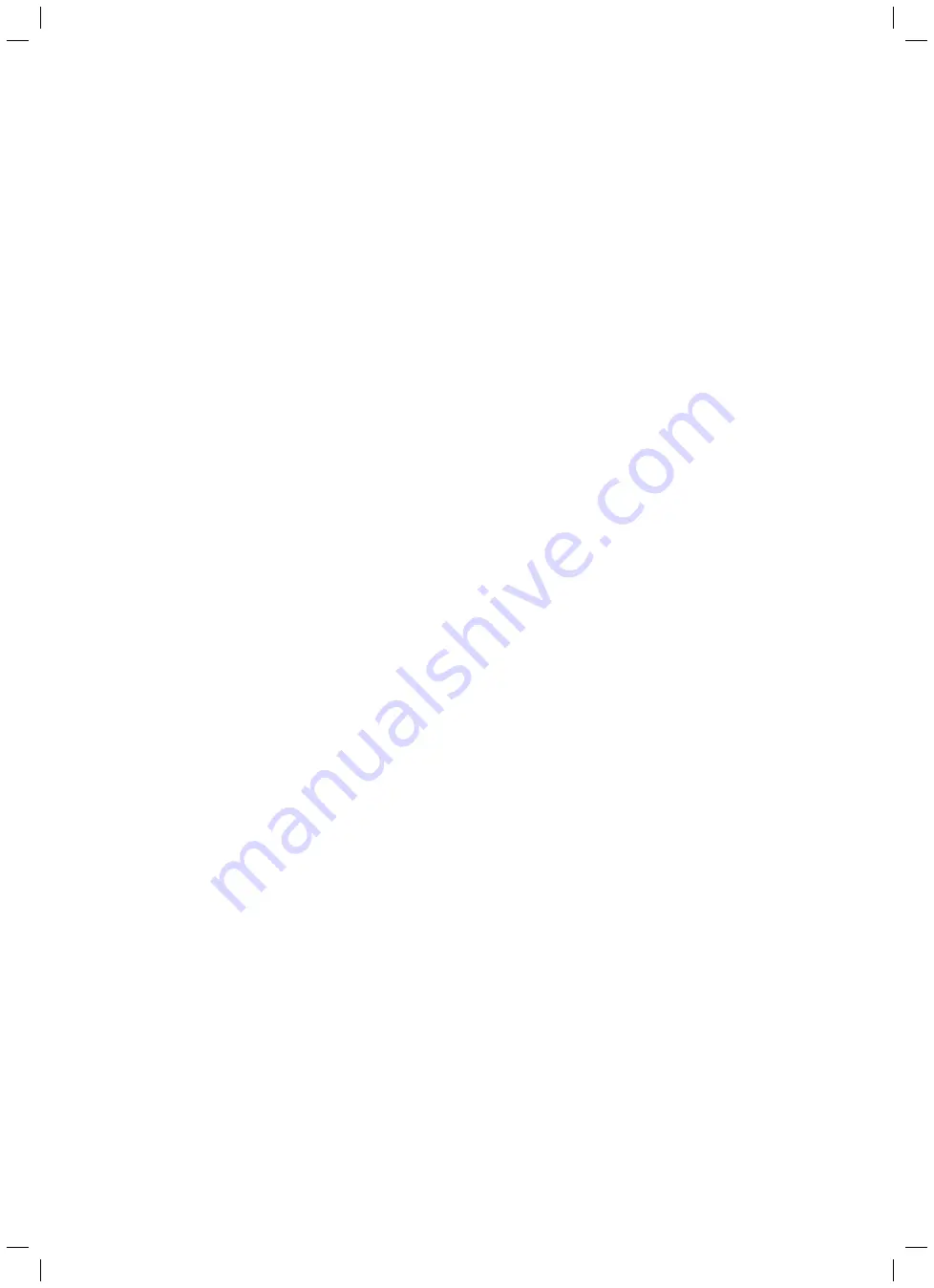
Instructions on commissioning, maintenance, and troubleshooting for auroSTOR 0020111119_02
19
Primary heating circuit control system
The primary heating circuit can be controlled in one
of the following ways:
Vaillant dual-channel eBUS controller with Vaillant
Control Centre (connection wiring diagrams 1 and 2,
¬ section 6.8)
Important:
Terminals
NTC
and
CYL.
of the Vaillant Control Centre
may not be connected at the same time.
– Option 1: The upper cylinder sensor
NTC
is connected to
terminal
NTC
of the Vaillant Control Centre.
The recharging of the cylinder is controlled via the eBUS
controller. Here, the cylinder temperature is measured
using the cylinder sensor
NTC
. The temperature is com-
pared with the target value programmed in the eBUS
controller and the cylinder is reheated if necessary.
– Option 2: The cylinder thermostat is connected
up to terminal
CYL.
of the Vaillant Control Centre.
The recharging of the cylinder is triggered via the cylin-
der thermostat. If the actual value falls below the target
temperature set on the cylinder thermostat, the cylinder
thermostat is shut. The closing of the cylinder thermo-
stat is registered by the Vaillant Control Centre and
passed onto the eBUS controller.
The eBUS controller releases the recharging of the
cylinder for the programmed primary heating times:
The primary heating device activates and the Vaillant
Control Centre switches the zone valves into the correct
position for the recharging of the cylinder.
The required zone valve position differs depending
on whether the S plan is being used:
– S plan: Valve
CH
closed, valve
DHW
open.
VRS 560/2
(connection wiring diagrams 3 and 4, ¬
section 6.8)
The upper cylinder sensor is connected to the terminal
SP 1
of the VRS 560/2.
The output EP of the VRS 560/2 is connected to the
input
CYL.
of the Vaillant Control Centre.
The recharging of the cylinder is controlled via the
VRS 560/2. Here, the sensor
SP 1
measures the cylinder
temperature. The temperature is compared with the pro-
grammed target value in the VRS 560/2.
Within the primary heating times programmed in the
VRS 560/2, the contact
EP
is closed if the actual value
falls below the target temperature for the cylinder.
The closing of the contact
EP
is registered by the
Vaillant Control Centre and the recharging of the cylin-
der is triggered: The primary heating device activates
and the Vaillant Control Centre switches the zone valves
into the correct position for the recharging of the cylin-
der.
The required zone valve position differs depending
on whether the S plan is being used:
– S plan: Valve
CH
closed, valve
DHW
open.
Vaillant dual-channel eBUS controller with VR 68/2
(connection wiring diagram 5, ¬
section 6.8)
The upper cylinder sensor is connected to the terminal
SP 1
of the VR 68/2.
The recharging of the cylinder is controlled via the eBUS
controller, which is connected with the VR 68/2 and
VR 61/2 via eBUS. The zone valves are switched via the
VR 61/2 (valve DHW open, heating circuit valve closed).
VRS 560/2 in conjunction with non-eBUS-compatible
controllers (connection wiring diagram 6, ¬
section 6.8)
The upper cylinder sensor is connected to the terminal
SP 1
of the VRS 560/2.
The output
EP
of the VRS 560/2 is connected to the
wiring of the S plan via the cylinder thermostat.
Important:
The target temperature on the cylinder thermostat must
be set to the maximum temperature!
The recharging of the cylinder is controlled via the
VRS 560/2. Here, the sensor
SP 1
measures the cylinder
temperature. The temperature is compared with the pro-
grammed target value in the VRS 560/2.
Within the primary heating times programmed in the
VRS 560/2, the contact
EP
is closed if the actual value
falls below the target temperature for the cylinder.
The switching signal is coupled into an S plan and the
recharging of the cylinder is triggered.
Room heating control
The room heating can be controlled in one of the follow-
ing ways:
Vaillant dual-channel eBUS controller with Vaillant
Control Centre (connection wiring diagrams 1, 2, 3,
and 4, ¬
section 6.8)
The room heating is controlled by the Vaillant
eBUS controller.
The actuation of the valves (S plan plan)
is controlled by the Vaillant Control Centre.
Vaillant dual-channel eBUS controller with VR 61/2
(connection wiring diagram 5, ¬
section 6.8)
The room heating is controlled by the Vaillant eBUS
controller.
The actuation of the valves (S plan plan) is controlled by
the VR 61/2.
Programmable timer and room thermostat
(connection wiring diagram 6, ¬
section 6.8)
The room heating is controlled using a programmable
timer and a room thermostat.
The actuation of the valves (S plan) is realised
via the programmable timer and DHW timer.
Description of the components 4