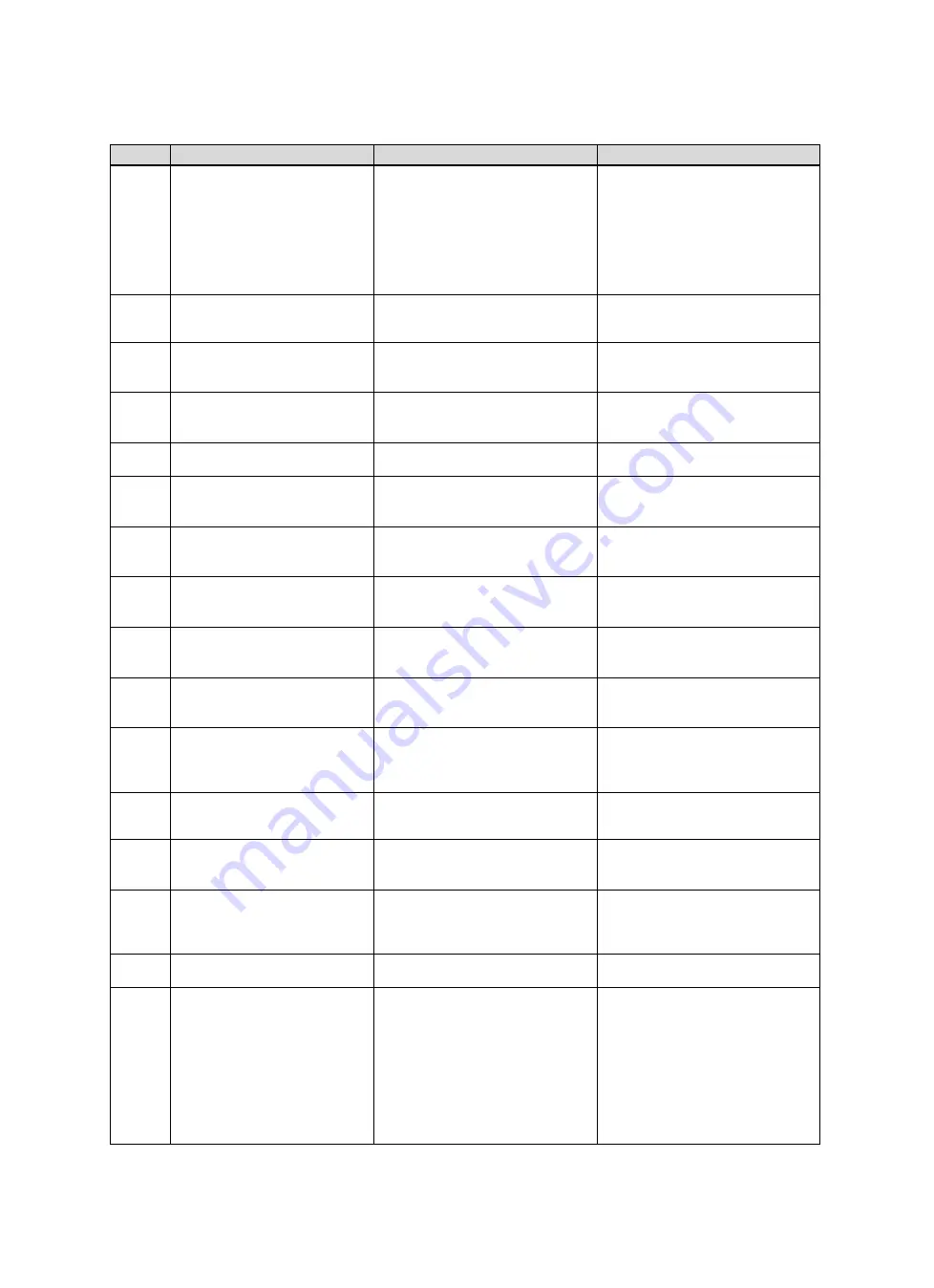
Appendix
0020291544_01 Hydraulic Station Installation and maintenance instructions
53
J
Fault codes
Code
Meaning
Cause
Remedy
F.022
Water pressure too low
–
Pressure loss in the building circuit
due to leakages or air pockets
–
Building circuit pressure sensor
defective
–
Check the building circuit for leaks
–
Top up with water, purge
–
Check the quality of the plug contact
on the PCB and on the cable har-
ness
–
Check that the pressure sensor is
working correctly
–
Replace the pressure sensor
F.042
Fault: Coding resistor
–
Coding resistor damaged or not set
–
Check that the coding resistor is
positioned correctly and, if required,
replace it.
F.073
Sensor fault: Build. circ. pressure
–
The sensor is not connected or the
sensor input has short-circuited
–
Check and, if required, replace the
sensor
–
Replace the cable harness
F.094
Fault: Vortex
–
Volume flow sensor not connected or
sensor input has short-circuited
–
Check and, if required, replace the
sensor
–
Replace the cable harness
F.103
Fault: Spare part ident.
–
Incorrect control PCB installed on
the outdoor unit
–
Installing the correct PCB
F.514
Sensor fault: Compr. inlet temp.
–
The sensor is not connected or the
sensor input has short-circuited
–
Check and, if required, replace the
sensor
–
Replace the cable harness
F.517
Sensor fault: Compr. outlet temp.
–
The sensor is not connected or the
sensor input has short-circuited
–
Check and, if required, replace the
sensor
–
Replace the cable harness
F.519
Sensor fault: Building circuit re-
turn temp.
–
The sensor is not connected or the
sensor input has short-circuited
–
Check and, if required, replace the
sensor
–
Replace the cable harness
F.520
Sensor fault: Building circuit flow
temp.
–
The sensor is not connected or the
sensor input has short-circuited
–
Check and, if required, replace the
sensor
–
Replace the cable harness
F.526
Sensor fault: EEV outlet temp.
–
The sensor is not connected or the
sensor input has short-circuited
–
Check and, if required, replace the
sensor
–
Replace the cable harness
F.546
Sensor fault: High pressure
–
The sensor is not connected or the
sensor input has short-circuited
–
Check the sensor (e.g. using an in-
stallation aid), and replace if neces-
sary
–
Replace the cable harness
F.582
Fault: EEV
–
EEV is not connected correctly or
there is a cable break to the coil
–
Check the plug connections and, if
required, replace the coil from the
EEV
F.585
Sensor fault: Capac. outlet temp.
–
The sensor is not connected or the
sensor input has short-circuited
–
Check and, if required, replace the
sensor
–
Replace the cable harness
F.703
Sensor fault: Low pressure
–
The sensor is not connected or the
sensor input has short-circuited
–
Checking the sensor (e.g. using an
installation aid), and replacing it if
necessary
–
Replace the cable harness
F.718
Fan unit 1: Fan blocked
–
There is no confirmation signal stat-
ing that the fan is rotating
–
Check the air route and, if required,
remove any blockages
F.729
Compressor outlet temperature
too low
–
The compressor outlet temperature
is lower than 0 °C for more than 10
minutes or the compressor outlet
temperature is lower than -10 °C
even though the heat pump is in the
operating characteristics.
–
Checking the high-pressure sensor
–
Checking that the EEV is working
correctly
–
Checking for condensate leaking
from the temperature sensor (under-
cooling)
–
Check whether the 4-port diverter
valve is in the intermediate position
–
Checking the refrigerant volume for
overfilling