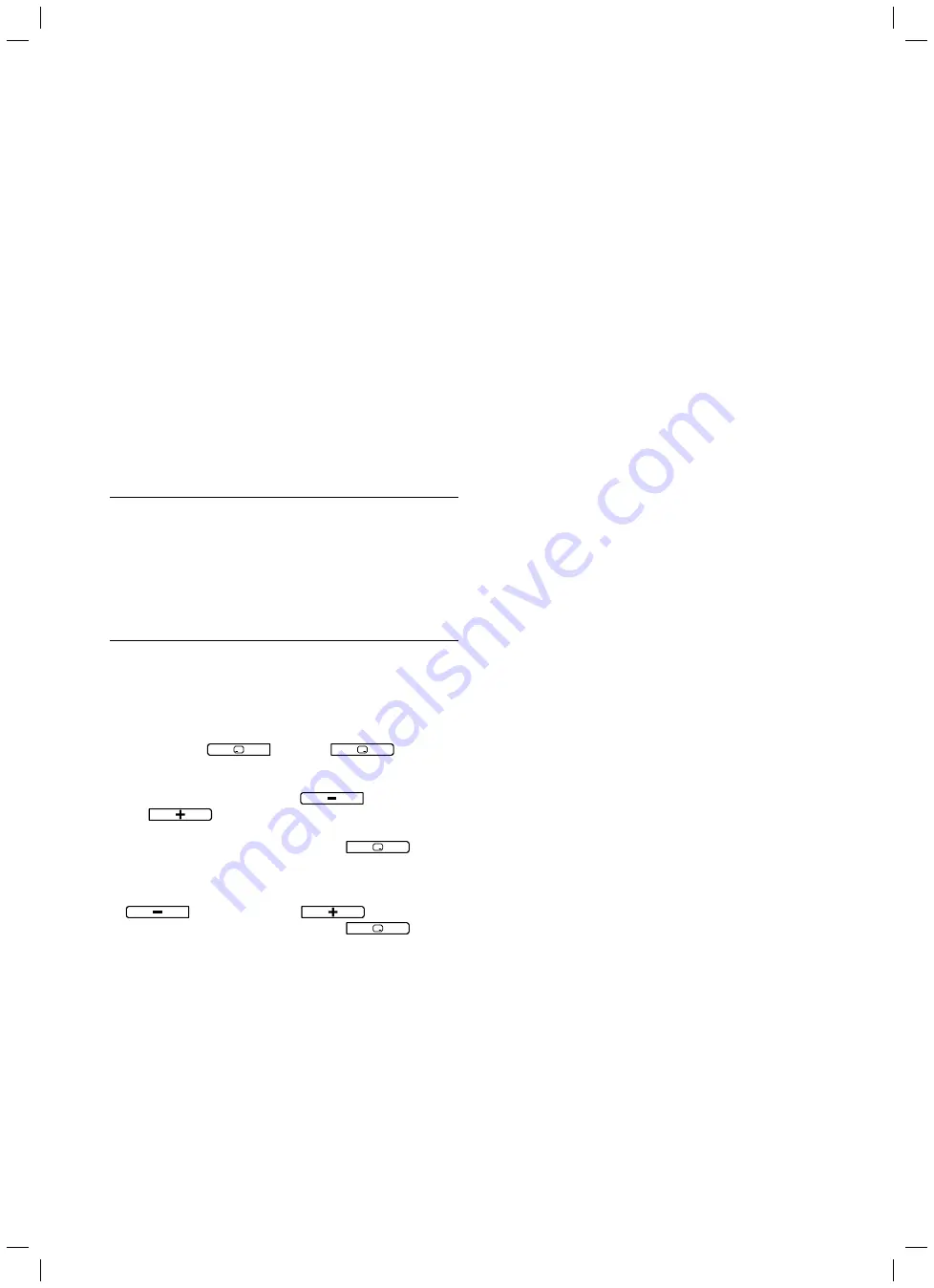
Operation
Installation and maintenance instructions ecoTEC plus 0020134833_01
37
9
9 Operation
The Vaillant ecoTEC plus boiler is fitted with a digital infor-
mation and analysis system (DIA). If additional settings are
required, which have not yet been configured using the
installation assistant, you can view and modify further
parameters using the DIA.
The operating concept and operation of the boiler is
described in the
¬ operating instructions
of the boiler. The
read-off and setting facilities of the operator level are also
described in the
¬ operating instructions
.
The following overview shows the read-off and setting facili-
ties of the installer level.
9.1
Calling up the installer level
b
Caution.
Risk of damage caused by incorrect han-
dling.
Incorrect settings at installer level can
cause damage to the heating installation.
>
You should only access the installer level
if you are an approved competent per-
son.
The installer level is secured against unauthorised access
with a password because incorrect parameter settings at
this level may cause functional faults and damage to the
heating installation.
>
Press the left
and right
selection
buttons ("i")
simultaneously
The following menu appears on the display.
>
Scroll using the minus button
or the plus but-
ton
until the menu point "Installer level"
appears.
>
Press the
right-hand selection button
to
select the menu point.
"Enter code" and the value "00" appear in the display.
>
Select the value 17 (code) using the minus button
or the plus button
.
>
Press the
right-hand selection button
to con-
firm the entered code.
The installer level appears with a selection of menu points.
i
In the following, a path specification at the
beginning of an action instruction specifies how
to access this function in the installer level, e.g.
Menu ¬ Installer level ¬ Test programs ¬ Test
programs
.
i
If you exit the installer level and then access it
again within 15 minutes, you do not have to
enter the code again.
Summary of Contents for ecoTEC plus VUI
Page 94: ......
Page 95: ......
Page 96: ...0020134833_01 GBIE 072012 Subject to change Manufacturer Supplier 0020134833 ...