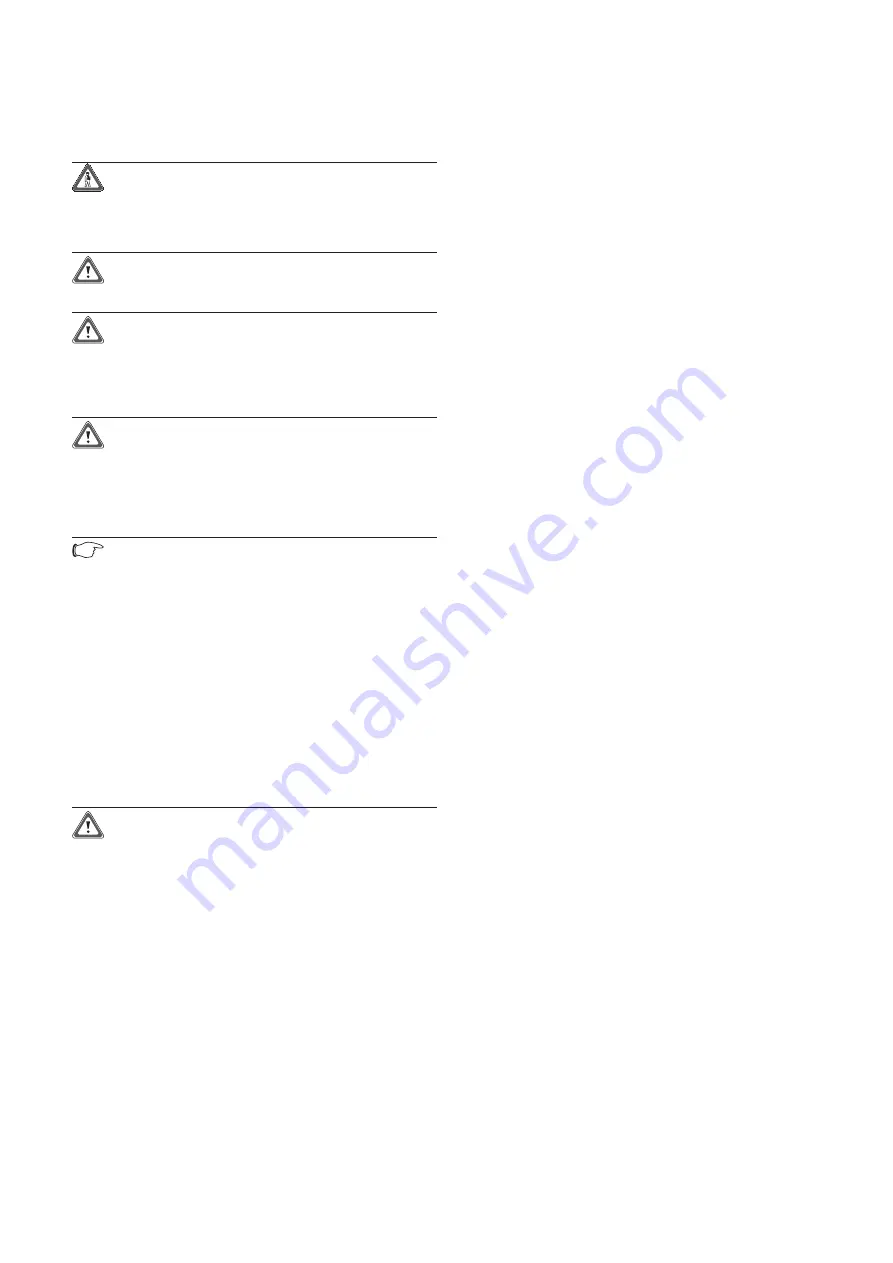
Installation and Servicing ecoTEC plus
20
4 Boiler installation sequence
4.3.3 Gas connection
Danger!
The gas connection may only be made by a
competent person.
The legal directives and the local regulations
for gas supply companies must be observed.
Caution!
Ensure a stress-relief assembly of the gas
pipes to avoid leakages!
Caution!
The gas regulating block may be tested for
leakage only with a maximum pressure of
150 mbar!
Higher testing pressures can damage the
gas fitting.
Caution!
When making final connection to the boiler, if
using soldered fittings, extra care should be
taken to avoid damage to isolation valves
through heat transfer.
Before connection check the supply of
local gas.
Note!
Ensure the gas supply pipe work is adequately
sized so that a 20 mbar gas pressure is
available at the boiler inlet at full flow rate.
• Tighten all connections.
• Check the gas connection with leak indicator
spray for leakage.
The gas supply can be connected from below, or
through the wall at the rear of the boiler. See fig 4.5.
and refer to section 3.4.
The whole of the gas installation, including the meter,
should be inspected, tested for soundness and purged
in accordance with the current issue of BS6891 and
in IE the current edition of I.S.813 “Domestic Gas
Installations”.
4.3.4 Water connections
Caution!
When making final connection to the boiler, if
using soldered fittings, extra care should be
taken to avoid damage through heat transfer.
Provision is made for the water connections to be
made from above the boiler, see fig 4.6 (using the two
22mm compression couplers supplied). The position is
shown on the wall template.
Flush out the domestic hot water and the heating
systems before connecting to the boiler.
4.3.5 Condensate trap and siphonic drain
connection
Refer to fig 4.5.
The condensate drain connection is at the underside
rear of the boiler.
The condense drain is suitable for use with standard
"Push fit" overflow pipe and couplings DO NOT use
adhesive when connecting to the spigot (1) The
condense drain pipe (2) should be non corrosive
plastic. The drain pipe should have a continuous fall
of a least (45mm per metre) away from the boiler.
Condensate should, if possible be discharged into the
household internal drainage system.
The condensate is discharged periodically in ‘slugs’ by
siphonic action.
It is not necessary to provide air breaks or extra traps
in the discharge pipe as there is already a 75mm high
trap inside the boiler. Fitting an extra trap may cause
the boiler siphon to work incorrectly.
Refer to BS5546 or BS6798 for advice on disposal of
boiler condensate.
(a) Preferably the drain pipe should run and terminate
internally to the house soil and vent stack at least
450mm above the invert of the stack. There must be
an air break in the discharge pipe upstream of the trap.
This should be designed so that the condensate cannot
be discharged into the house if the condensate drain
pipe becomes blocked.
(b) Connecting into the internal discharge branch
(e.g. sink waste or washing machine) with an external
termination, the condensate drain pipe should have a
minimum diameter of 22mm with no length restriction
and should incorporate a trap with a 75mm (3)
seal. The connection should preferably made down
stream of the sink waste trap, if the connection is
only possible up stream, then an air break is needed
between the two traps. This is normally provided by
the sink waste.
(c) Termination in a gully (5) below grid level (6) and
above the water level. The external pipe length should
be kept as short as possible to minimise the risk of
freezing and should not be more than 3 metres.
(d) At a condensate absorption point (soak away) (7).
The external pipe length should not be more than 3
metres.
Refer to the latest issue of BS 6798 Specification
for installation of gas fired boilers of rate input not
exceeding 70kW net for further information.
Before operating the boiler the condensate trap must
be filled with water.
4.3.6 Installing the flue system
• Install the flue system (refer to the separate air/flue
duct installation instructions).
Supplied by HeatingSpares247.com
Summary of Contents for eco TEC plus 415
Page 47: ...Installation and Servicing ecoTEC plus 47 Appendix 14 Supplied by HeatingSpares247 com...
Page 48: ...Installation and Servicing ecoTEC plus 48 Supplied by HeatingSpares247 com...
Page 49: ...Installation and Servicing ecoTEC plus 49 Supplied by HeatingSpares247 com...
Page 50: ...Installation and Servicing ecoTEC plus 50 Notes Supplied by HeatingSpares247 com...
Page 51: ...Installation and Servicing ecoTEC plus 51 Notes Supplied by HeatingSpares247 com...
Page 52: ...0020020828_02 GB 08 2006 Subject to alteration Supplied by HeatingSpares247 com...
Page 54: ...834449_09GB_082006 qxd 10 08 2006 12 20 Seite 2 Supplied by HeatingSpares247 com...
Page 88: ...36 834449_09GB_082006 qxd 10 08 2006 12 20 Seite 36 Supplied by HeatingSpares247 com...
Page 112: ...60 834449_09GB_082006 qxd 10 08 2006 12 20 Seite 60 Supplied by HeatingSpares247 com...
Page 113: ...61 834449_09GB_082006 qxd 10 08 2006 12 20 Seite 61 Supplied by HeatingSpares247 com...
Page 114: ...62 834449_09GB_082006 qxd 10 08 2006 12 20 Seite 62 Supplied by HeatingSpares247 com...
Page 115: ...63 834449_09GB_082006 qxd 10 08 2006 12 20 Seite 63 Supplied by HeatingSpares247 com...
Page 118: ...Supplied by HeatingSpares247 com...
Page 120: ...0020010870 01 GB 03 2006 2 Supplied by HeatingSpares247 com...
Page 138: ...0020010870 01 GB 03 2006 20 Supplied by HeatingSpares247 com...
Page 158: ...Notes 0020010870 01 GB 03 2006 40 Supplied by HeatingSpares247 com...
Page 159: ...Supplied by HeatingSpares247 com...
Page 171: ...Instructions for Use ecoTEC plus 11 Supplied by HeatingSpares247 com...
Page 172: ...0020020829_02 GB 08 2006 Subject to alteration Supplied by HeatingSpares247 com...