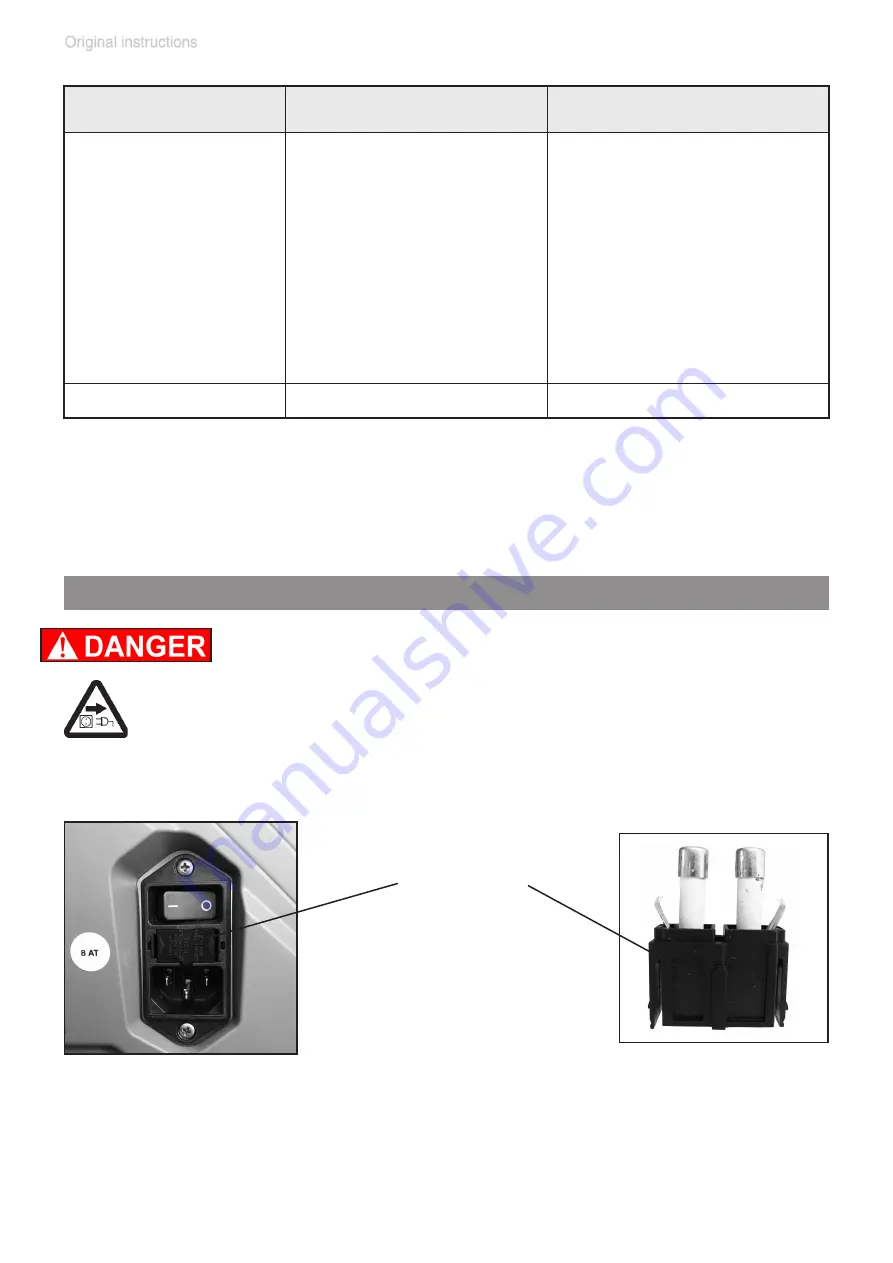
page 46 of 88
fuse holder
➨
Keep the snap-fits squeezed and pull the fuse holder out.
➨
The fuse holder contains two fuses of the same type. Replace the
defective fuse by a fuse of the same type (see “Technical data”, pg.
➨
Insert the fuse holder into the housing until it snaps.
Replacing the device fuse
➨
Switch off the pump.
➨
Disconnect the electrical power cord
before remov-
ing the fuse holder.
Identify and eliminate the cause of failure before switch-
ing on the pump again.
➨
A service manual with exploded view drawings, spare parts list and
directions for repair is available on request.
+
The service manual is intended for trained service people only.
Fault
Possible cause
Remedy
❑
Pump too noisy.
➨
Atmospheric or high
pressure at the pump
inlet?
✔
Connect hose or silencer
to pump outlet. Be careful
not to cause outlet over-
pressure, especially with
condensable vapors.
➨
Diaphragm crack or
diaphragm clamping
disc loose?
✔
Perform maintenance.
➨
Other than above men-
tioned causes?
✔
Contact local distributor.
❑
Pump seized.
✔
Contact local distributor.
Summary of Contents for ME 16C NT-ME 16C NT+EK
Page 29: ...page 29 of 88 ME 16C NT MD 12C NT MV 10C NT 1 5 3 2 6 4 8 7 9...
Page 49: ...page 49 of 88 Disassembling the pump housing 1 3 2...
Page 50: ...page 50 of 88 4 6 5 1 2 4 4x 2 5 mm 2 5 mm...
Page 51: ...page 51 of 88 7 9 8 4 4x without EK...
Page 52: ...page 52 of 88 10 12 11 4 2x 4 4x Don t loosen this screw...
Page 53: ...page 53 of 88 13 15 14 5 2x 5 2x...
Page 54: ...page 54 of 88 16 18 17 2 5 mm...
Page 56: ...page 56 of 88 Replacing the diaphragms 19 21 20 Clean 5 8x 20696867 20696839...
Page 57: ...page 57 of 88 22 24 23 1 2 3 Pay attention to number of washers...
Page 58: ...page 58 of 88 25 27 26...
Page 61: ...page 61 of 88 34 36 35 Clean 20696867 20696839...
Page 62: ...page 62 of 88 37 39 38 IN IN EX EX 4x...
Page 63: ...page 63 of 88 40 42 41 IN EX T20 4x 2 2 ft lbf 3 Nm...
Page 64: ...page 64 of 88 43 45A 44 Maintain all pump heads in the same way MD 12C NT...
Page 65: ...page 65 of 88 45B 45C 45D ME 16C NT MV 10C NT ME 16C NT MD 12C NT MV 10C NT...
Page 67: ...page 67 of 88 4A 3 2 size 2 2x Version A valve 24 4 mm...
Page 68: ...page 68 of 88 5A 20696839 24 4 mm 26 mm 4B 5B 20696839 37 mm 40 mm Version B valve 37 mm...
Page 69: ...page 69 of 88 6 7 size 2 2x 7A without EK size 2 2x...
Page 71: ...page 71 of 88 Assembling the pump housing 46 47 48 5 2x 8 9 ft lbf 12 Nm...
Page 72: ...page 72 of 88 50 49 5 2x 8 9 ft lbf 12 Nm 51...
Page 73: ...page 73 of 88 53 52 4 4x 3 7 ft lbf 5 Nm 54 4 2x 3 7 ft lbf 5 Nm...
Page 74: ...page 74 of 88 56 55 4 4x 3 7 ft lbf 5 Nm 57...
Page 75: ...page 75 of 88 59 58 60 4 4x 3 7 ft lbf 5 Nm...
Page 76: ...page 76 of 88 62 61 63...
Page 79: ...page 79 of 88 4 20638821 20638821 5 6...
Page 80: ...page 80 of 88 7 T20 4x size 1 4x 8...
Page 83: ...page 83 of 88 Declarations and certificates...
Page 84: ...page 84 of 88...
Page 87: ...page 87 of 88...