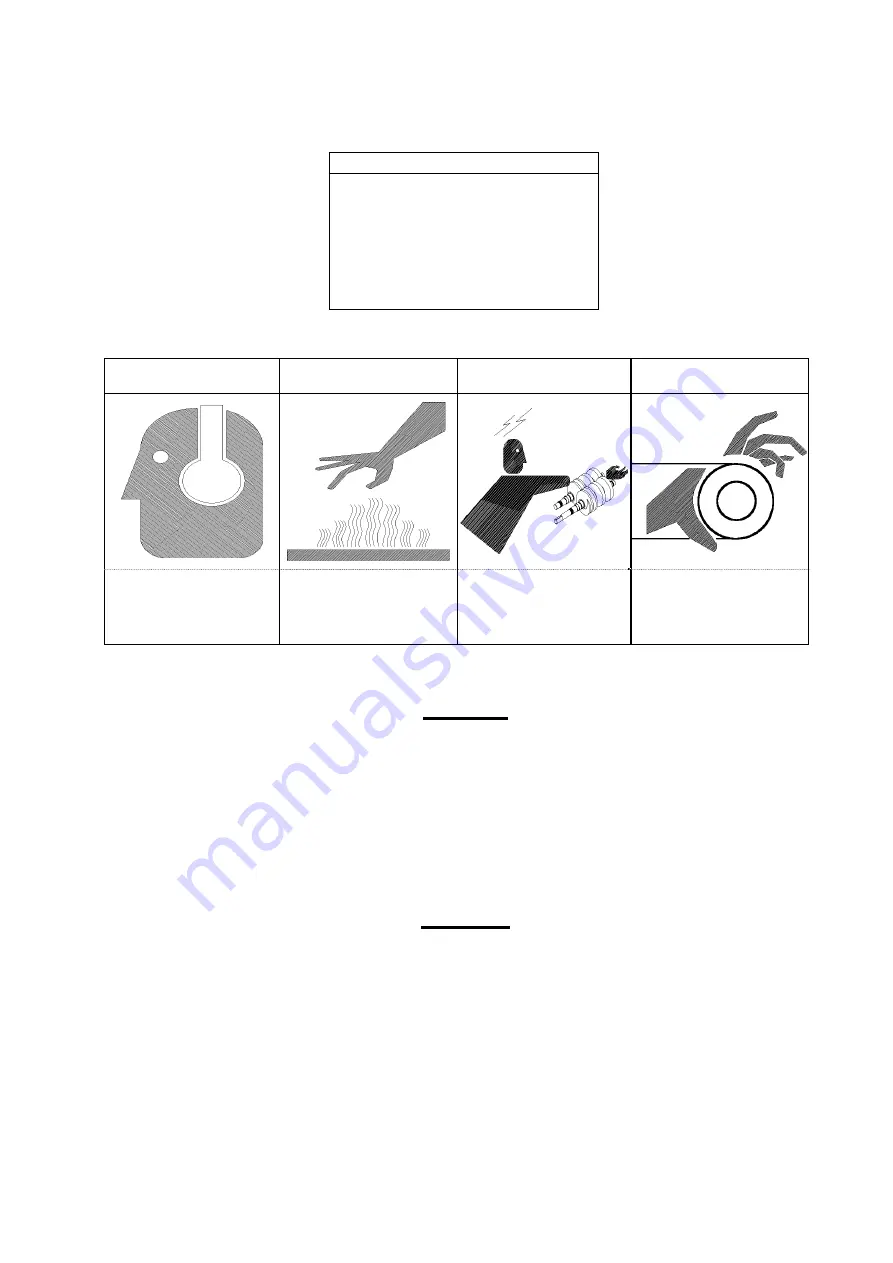
NOTICE
The above safety instruction tags were attached to your unit prior to shipment. Do not remove,
paint-over, or obscure in any manner.
Failure to heed these warnings could result in serious bodily injury to the personnel operating and
maintaining this equipment.
SAFETY
1. Avoid excessive weight due to the pipings flanged to the pumps.
2. Do not operate the pump without coupling guard. Also, the starting with a wrong rotating
direction could damage the pump.
3. Never operate the pump with suction side open to air.
4. Do not carry any maintenance while the pump is connected to the motor.
SAFETY INSTRUCTIONS
1. Do not operate before reading the
enclosed instruction manual.
2. Use adequate protection warning
and safety equipment necessary
to protect against hazards involved
in installation and operation of this
equipment.
WARNING CAUTI
ON
WARNING
WARNING
Heari ng
Protection
Requi red
Do not touch
hot surfaces
Keep body and
clothing away from
machine openings
Do not operate
without guards in
place